Hi. I'm Rob. Perhaps you gathered that from my username. Mandy will probably chime in here at some point. We're building a teardrop from scratch. Perhaps you gathered that from the title.
This is what's going on. It will have a queen size bed because I'm tall, and we have a large dog, who I'm sure you'll see here. He takes up quite a bit of space, and most times a queen seems a tad too small. The trailer will have a grill, of course. And a fridge/freezer. It will have an outdoor shower and support equipment (propane, water tank, and water heater). It will also have a sink. The trailer will be off-road capable and has decent ground clearance (~20" if I remember correctly).
Anyway, you probably came here for pictures, so here goes.
This is a very early design we had looked at:
It had a hatch at the rear which we didn't love, so we scrapped that. I've read enough stories here and elsewhere of water leaks around this hinge to stay well away.
We were also concerned about tongue weight, so we moved the fridge to the front here:
We made a full scale mock-up of the layout as a sanity check, to make sure the height of the galley was in the right ballpark.
This layout had the grille and sink "stacked" but on separate drawer slides, so the sink would pull out beyond the grill for use. I thought this was clever, but I had a really hard time finding a good faucet option that wouldn't be super tall.
We were concerned about overall height of the trailer, so we moved the sink out from under the grill to bring everything down a bit:
This isn't exactly where we're headed, but it's pretty close to the final design. Of course there are constant changes to the details, but the layout has been pretty constant for a time now.
So we got to work on fabricating. Well, not quite. We got a whole bunch of tubing that was reclaimed from Rockingham Park in Salem, NH. Since it was used, it needed some cleaning before we could do anything with it. So all the tubes got a bath in rust remover, and then in paint.
We used a big PVC pipe with a cap for the rust remover bath:
Then took off the old paint with an abrasive wheel on the drill press. Here you can see (left to right) before - after - during:
Then the tubes got filled with a rusty-metal primer/sealer, the excess dumped out, and left out to dry. We're in New England, so as much rust-prevention as possible is maybe barely enough. So once all THAT was done, we got to fabricating.
This is what's going on. It will have a queen size bed because I'm tall, and we have a large dog, who I'm sure you'll see here. He takes up quite a bit of space, and most times a queen seems a tad too small. The trailer will have a grill, of course. And a fridge/freezer. It will have an outdoor shower and support equipment (propane, water tank, and water heater). It will also have a sink. The trailer will be off-road capable and has decent ground clearance (~20" if I remember correctly).
Anyway, you probably came here for pictures, so here goes.
This is a very early design we had looked at:
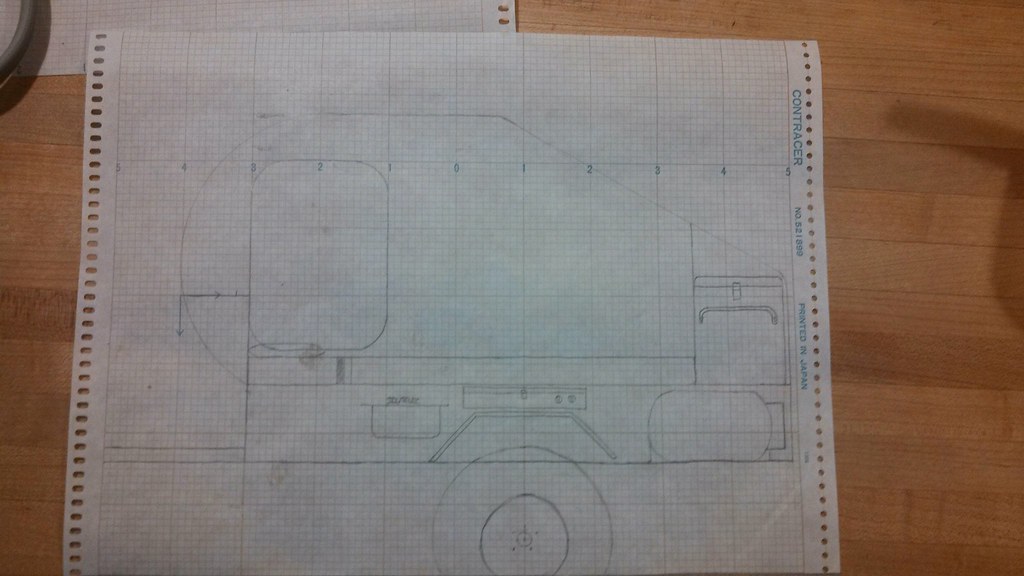
It had a hatch at the rear which we didn't love, so we scrapped that. I've read enough stories here and elsewhere of water leaks around this hinge to stay well away.
We were also concerned about tongue weight, so we moved the fridge to the front here:

We made a full scale mock-up of the layout as a sanity check, to make sure the height of the galley was in the right ballpark.
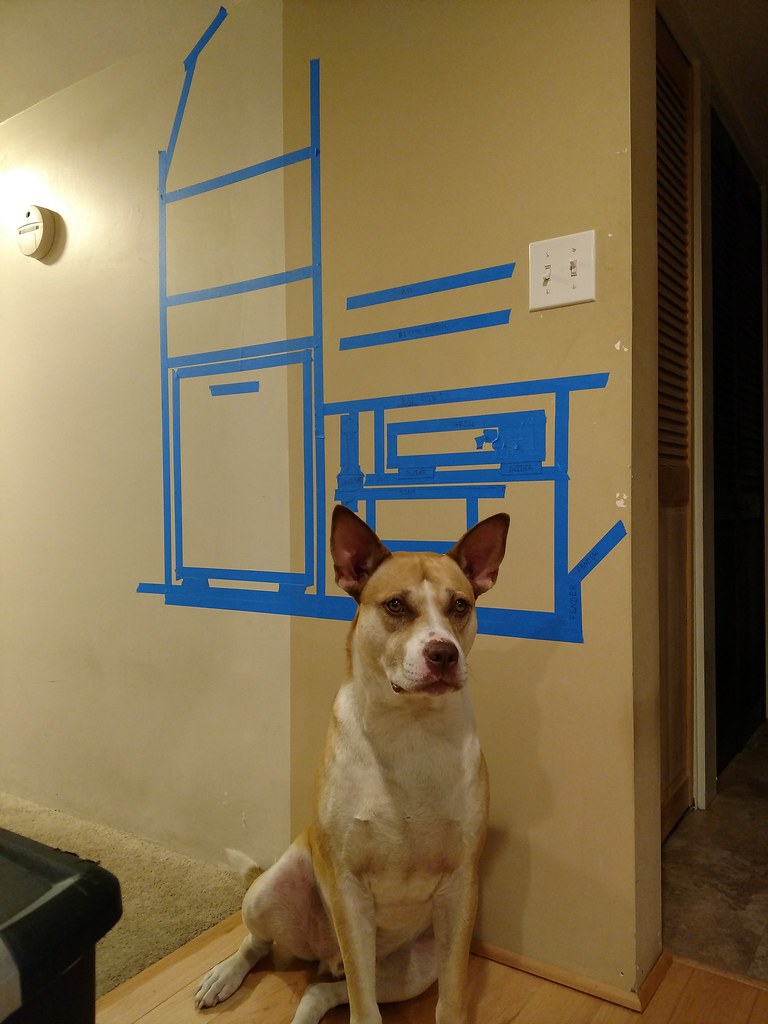
This layout had the grille and sink "stacked" but on separate drawer slides, so the sink would pull out beyond the grill for use. I thought this was clever, but I had a really hard time finding a good faucet option that wouldn't be super tall.
We were concerned about overall height of the trailer, so we moved the sink out from under the grill to bring everything down a bit:

This isn't exactly where we're headed, but it's pretty close to the final design. Of course there are constant changes to the details, but the layout has been pretty constant for a time now.
So we got to work on fabricating. Well, not quite. We got a whole bunch of tubing that was reclaimed from Rockingham Park in Salem, NH. Since it was used, it needed some cleaning before we could do anything with it. So all the tubes got a bath in rust remover, and then in paint.
We used a big PVC pipe with a cap for the rust remover bath:
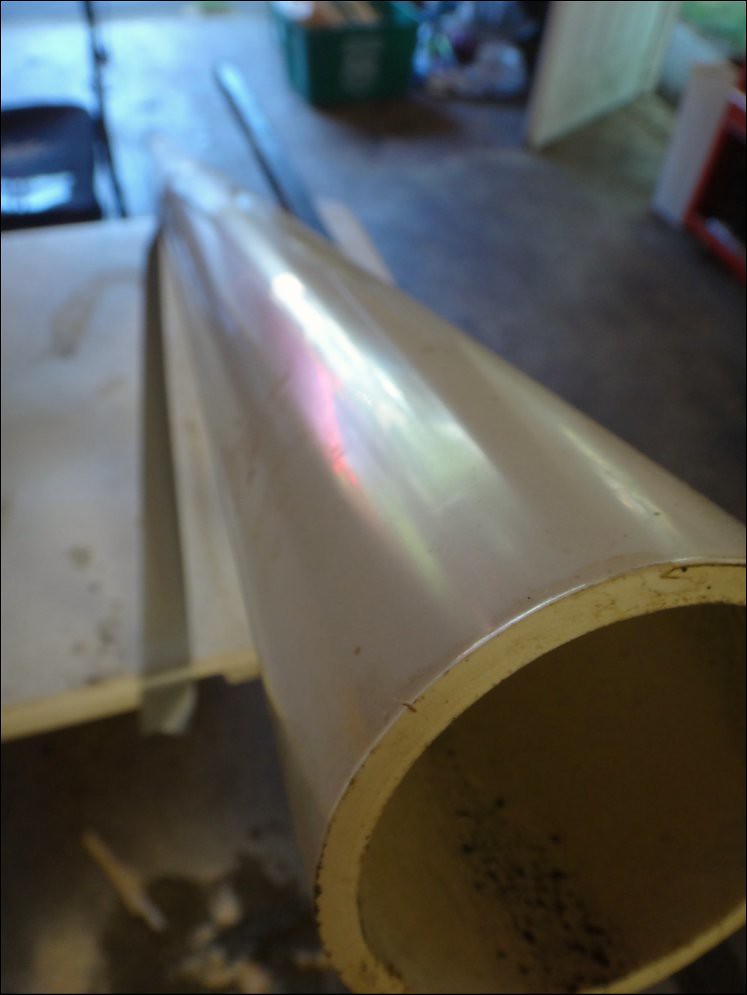
Then took off the old paint with an abrasive wheel on the drill press. Here you can see (left to right) before - after - during:

Then the tubes got filled with a rusty-metal primer/sealer, the excess dumped out, and left out to dry. We're in New England, so as much rust-prevention as possible is maybe barely enough. So once all THAT was done, we got to fabricating.
Last edited: