Revco
Adventurer
So I built my winch mount/receiver the other day, thought I'd share the process. Since my rig isn't a full time offroader, and I use my winch on my 18' car hauler trailer, I needed to it be versatile. I looked into buying the pre-made winch mounts, but none of them looked sturdy enough to get the job done. Most are made of 3/16" material for the plate and .120" wall for the receiver tube. I built mine out of scrap metal I had laying around in the shop...
First, a piece of 1/4" steel plate...
Cleaned it off and sprayed on some Dykem Steel Blue and scribed some lines into it, marking the holes for the winch bolts, and cut lines...
Then cut the piece to size and drilled the holes...
Then I cut a piece of 2x2x.250" tubing down to length and cleaned it up...
Marked the center of the tube for quick alignment...
Drilled a small hole dead center of the plate for alignment...
Laid the plate on top, aligning the marked centers with the hole int he center of the plate...
Then I got to welding. I had some 3/8" thick suspension tabs in the toolbox so I used them as gussets and finished welding it all up...
I cleaned off all the slag and Dykem, gave it a coat of black industrial enamel paint (no pics, as I was high and tired by then)
I still need to weld a front section on to mount the fairlead, so the paint was just to prevent flash rust. I loaned my plasma cutter to a neighbor, so once I get it back I'll cut out the fairlead bracket and get it welded up. I'll toss the whole thing in the sandblaster and give it a good coat of paint or drop it off at the powdercoating shop since I need to drop off some other parts for a hot rod project there soon anyway. I'll try to get more pics.
First, a piece of 1/4" steel plate...
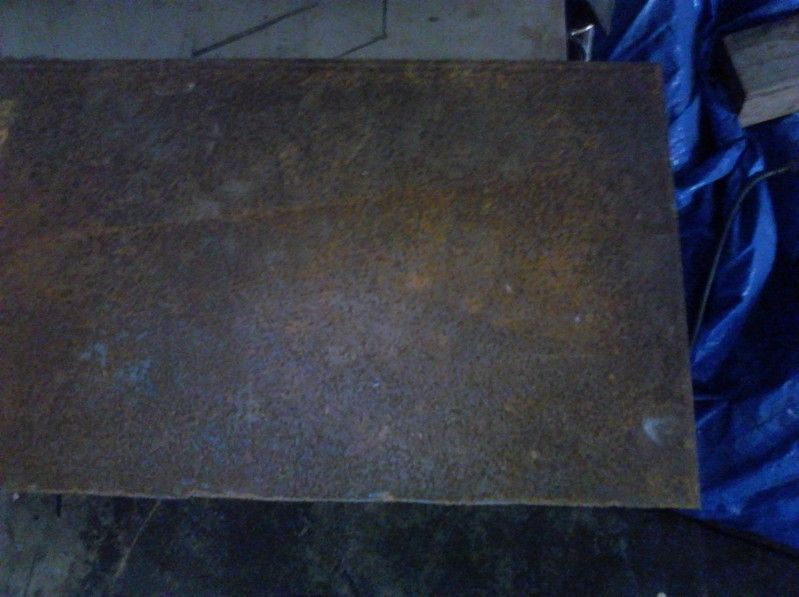
Cleaned it off and sprayed on some Dykem Steel Blue and scribed some lines into it, marking the holes for the winch bolts, and cut lines...
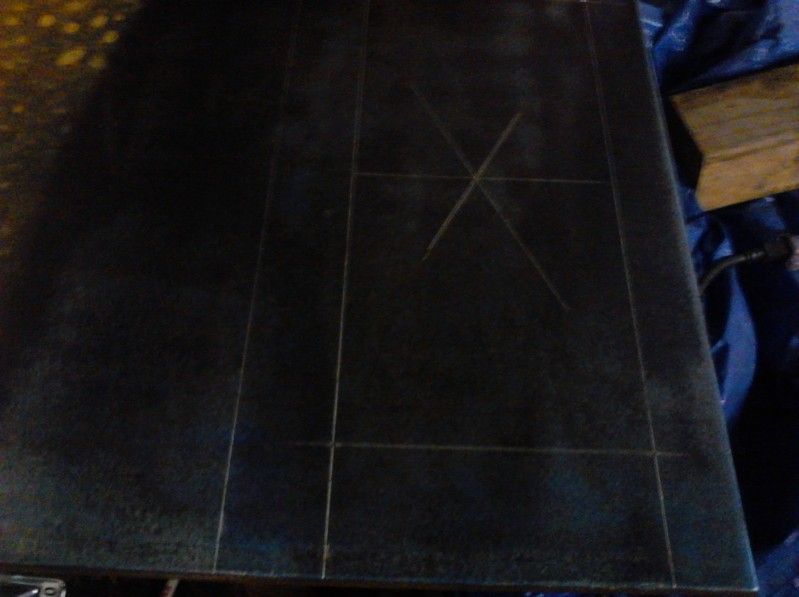
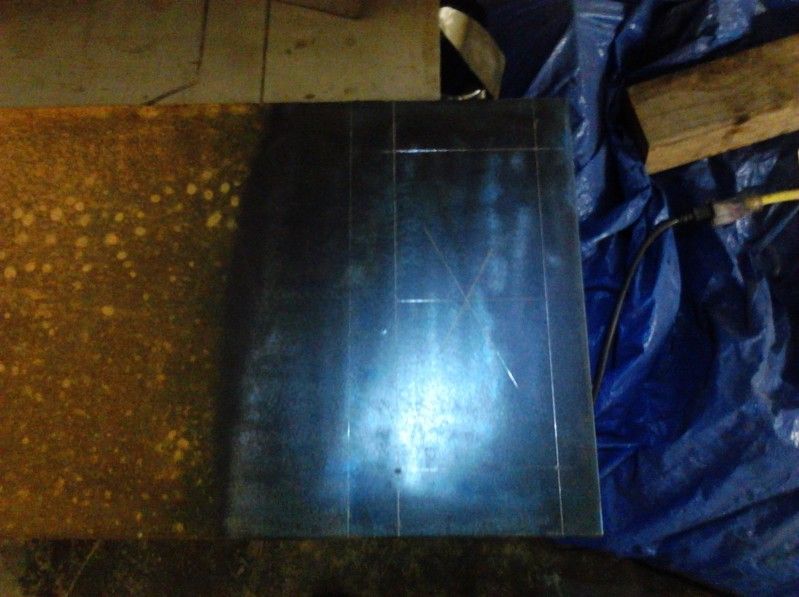
Then cut the piece to size and drilled the holes...
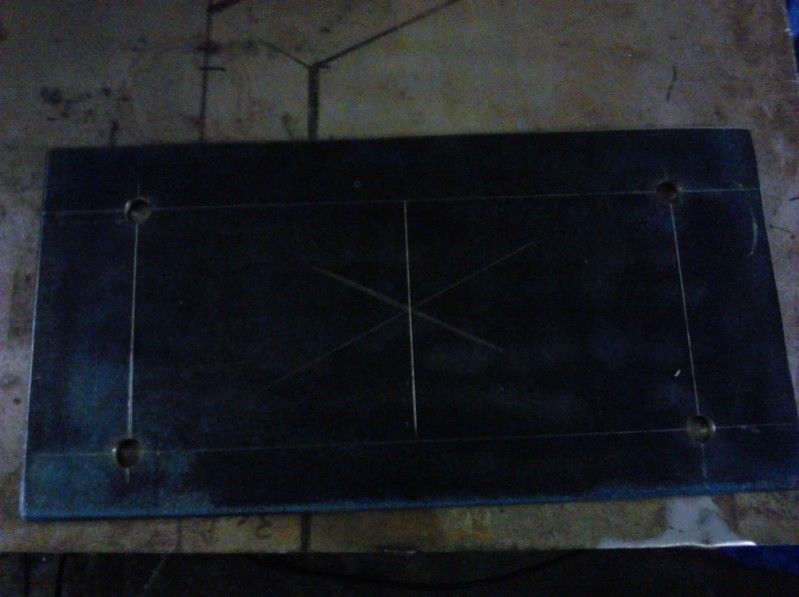
Then I cut a piece of 2x2x.250" tubing down to length and cleaned it up...
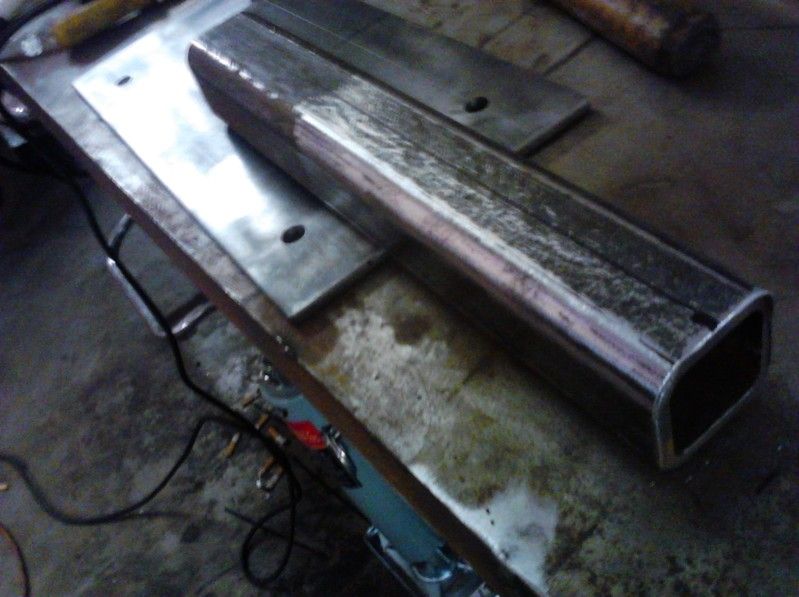
Marked the center of the tube for quick alignment...
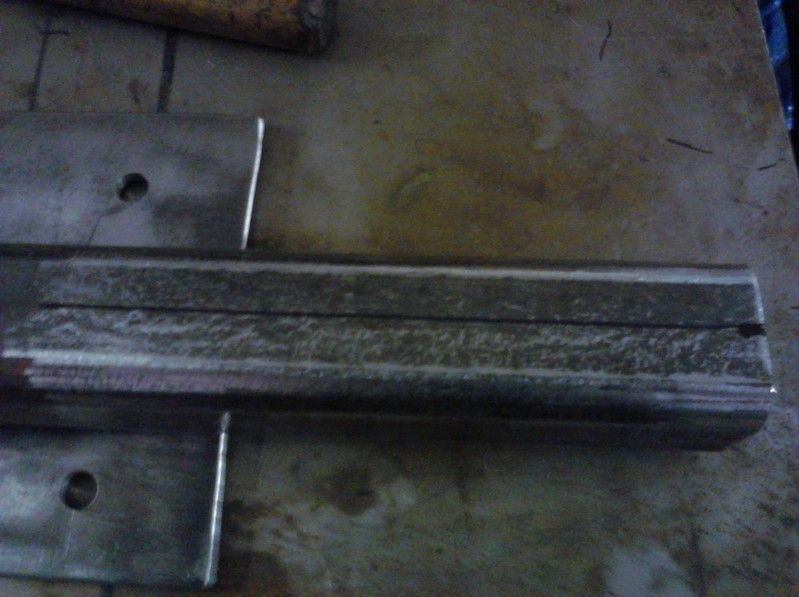
Drilled a small hole dead center of the plate for alignment...
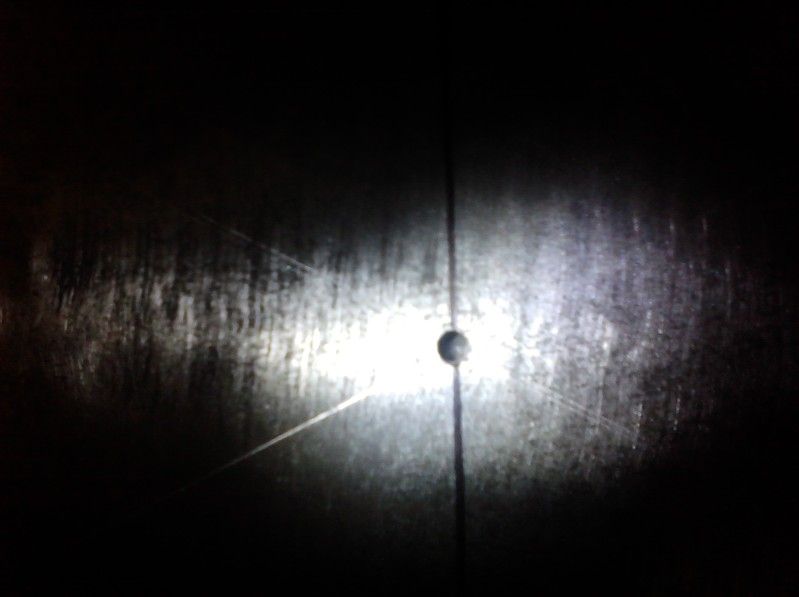
Laid the plate on top, aligning the marked centers with the hole int he center of the plate...
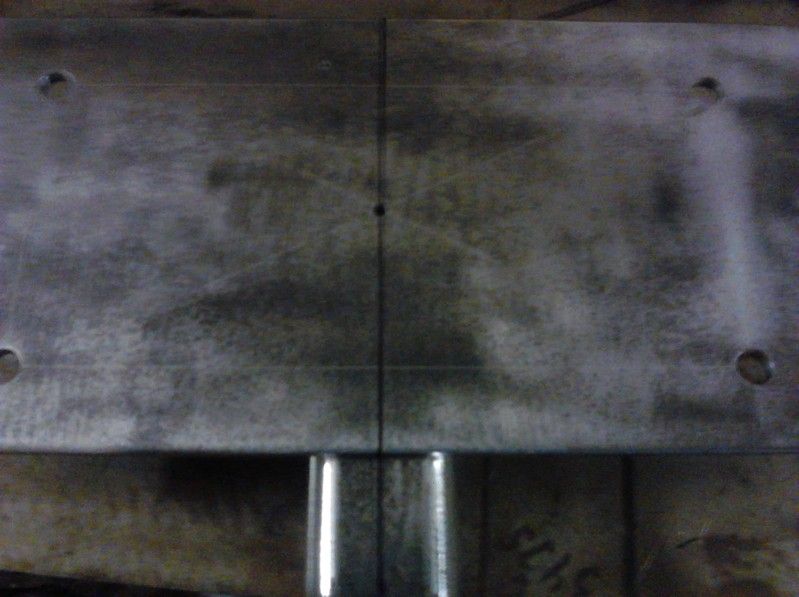
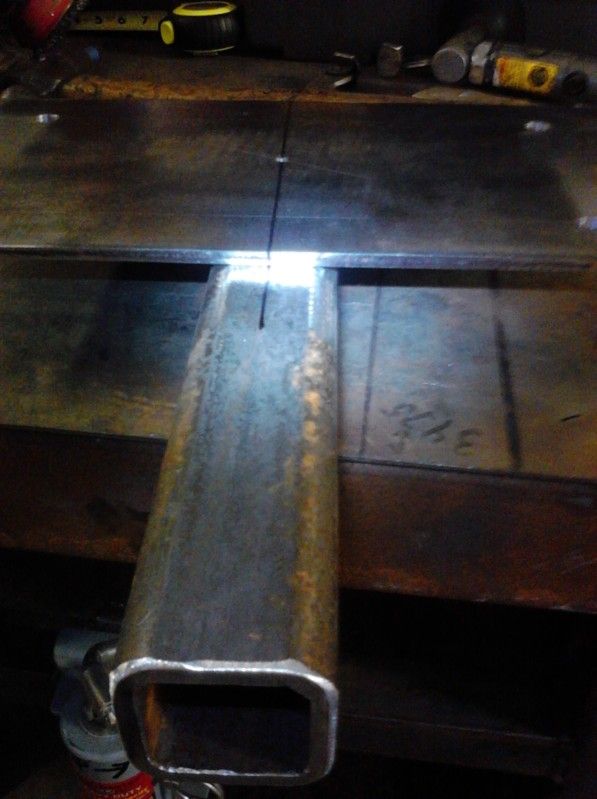
Then I got to welding. I had some 3/8" thick suspension tabs in the toolbox so I used them as gussets and finished welding it all up...
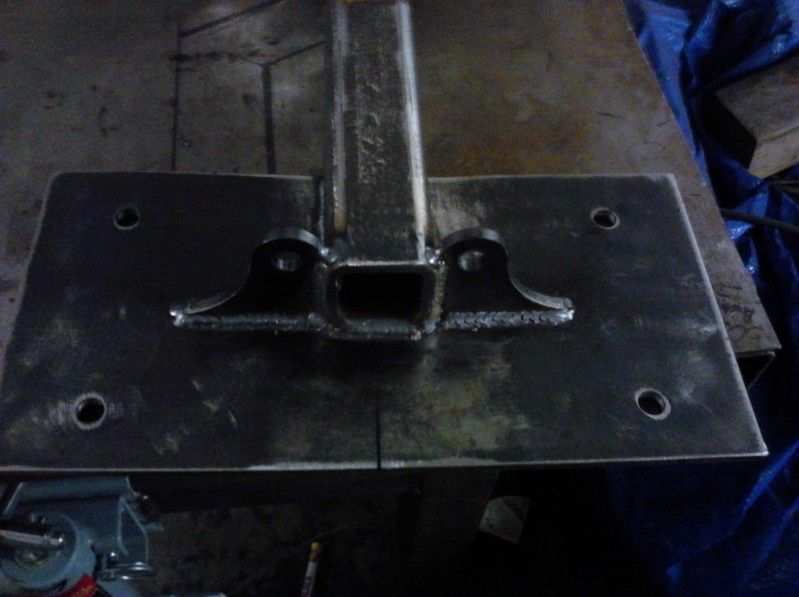
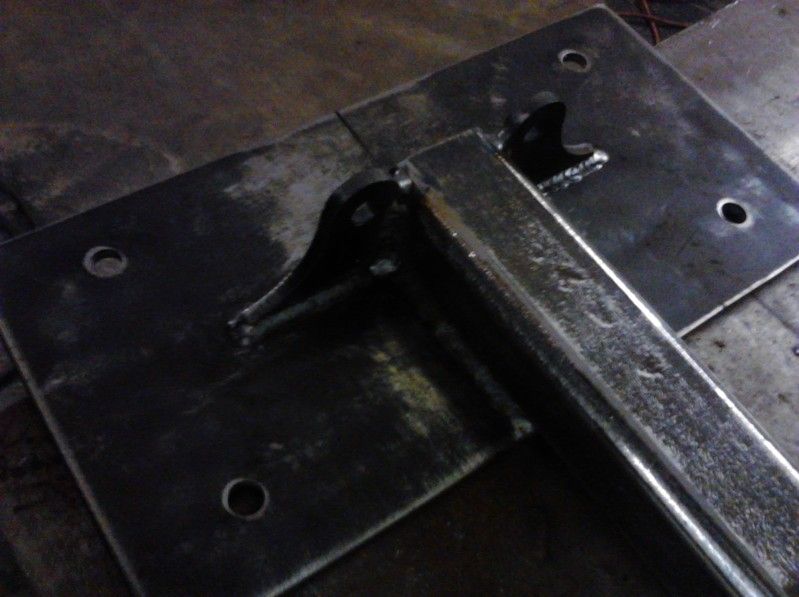
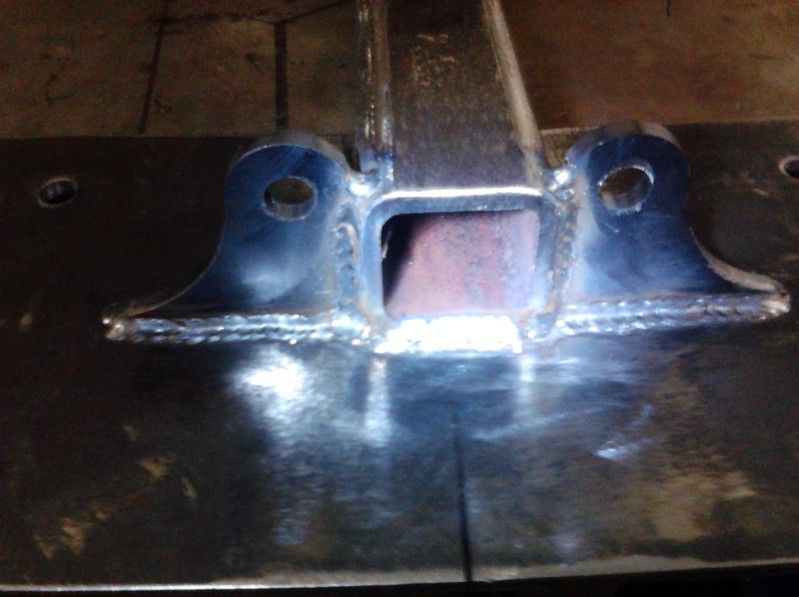
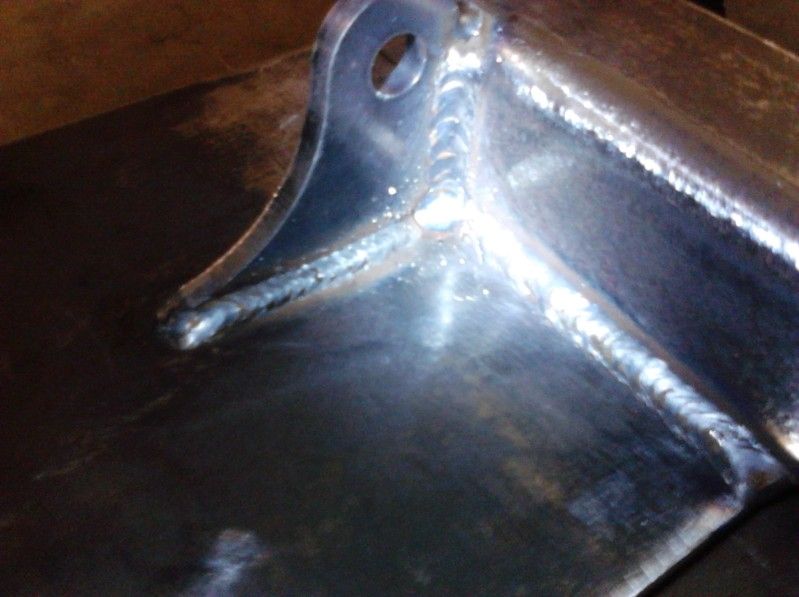
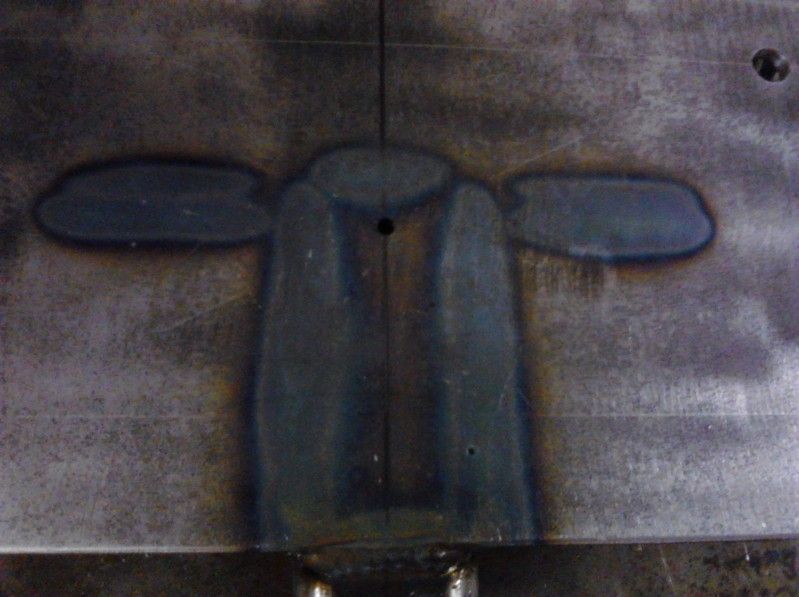
I cleaned off all the slag and Dykem, gave it a coat of black industrial enamel paint (no pics, as I was high and tired by then)
I still need to weld a front section on to mount the fairlead, so the paint was just to prevent flash rust. I loaned my plasma cutter to a neighbor, so once I get it back I'll cut out the fairlead bracket and get it welded up. I'll toss the whole thing in the sandblaster and give it a good coat of paint or drop it off at the powdercoating shop since I need to drop off some other parts for a hot rod project there soon anyway. I'll try to get more pics.