The final phase of swapping in an external slave is that the bearing retainer needs to be swapped out. The internal slave bearing retainer is shorter and reveals more spline. In the picture below you can see the final setup, the throw out bearing in the front, followed by the clutch fork, and finally the bearing retainer plate.
When swapping the transfer-case if you did not get an AX15/NP2321 combo you will need to get the correct input gear for the transfer case. The important thing to look for is the variations in the 231 transfer case input gear. The 231 comes in 21 spline (found behind the BA10/5, and I believe pre 91' AW4) and 23 spline (found behind the AX15 and post 91' AW4) versions. The input gear comes in three lengths, long, medium (rare) and short. To know which length input gear you have or will be pulling from the donor just take a quick measurement. The long shafts protrude 2.1" from the front mounting face of the transfer case. The short version protrudes 1.2". The rare medium shaft protrudes 1.7". You should also be careful when swapping any of these gears due to different bearing widths and gear teeth. For my specific situation I'm going from an AX15 internal slave to AX15 external slave, and both transferases had the short input gear. So it was a straight swap. While the 4WD shift linkage is the same in Jeeps equipped with the AX15 and will connect. I added in an aftermarket linkage that is simpler in setup and provides a smooth shift from Boostwerks. A google search returns several results of different manufacturers.
All buttoned up with the new external slave cylinder in place.
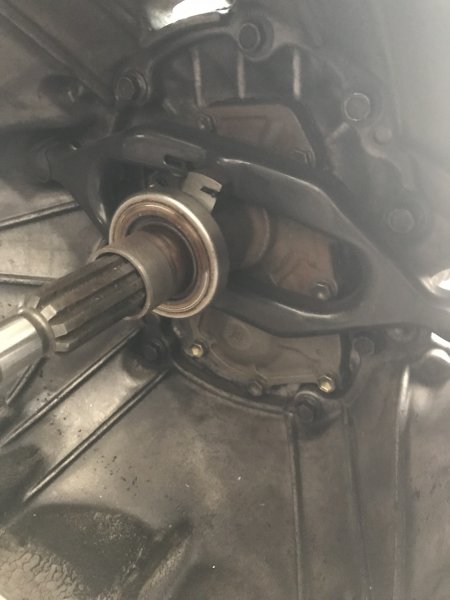
When swapping the transfer-case if you did not get an AX15/NP2321 combo you will need to get the correct input gear for the transfer case. The important thing to look for is the variations in the 231 transfer case input gear. The 231 comes in 21 spline (found behind the BA10/5, and I believe pre 91' AW4) and 23 spline (found behind the AX15 and post 91' AW4) versions. The input gear comes in three lengths, long, medium (rare) and short. To know which length input gear you have or will be pulling from the donor just take a quick measurement. The long shafts protrude 2.1" from the front mounting face of the transfer case. The short version protrudes 1.2". The rare medium shaft protrudes 1.7". You should also be careful when swapping any of these gears due to different bearing widths and gear teeth. For my specific situation I'm going from an AX15 internal slave to AX15 external slave, and both transferases had the short input gear. So it was a straight swap. While the 4WD shift linkage is the same in Jeeps equipped with the AX15 and will connect. I added in an aftermarket linkage that is simpler in setup and provides a smooth shift from Boostwerks. A google search returns several results of different manufacturers.
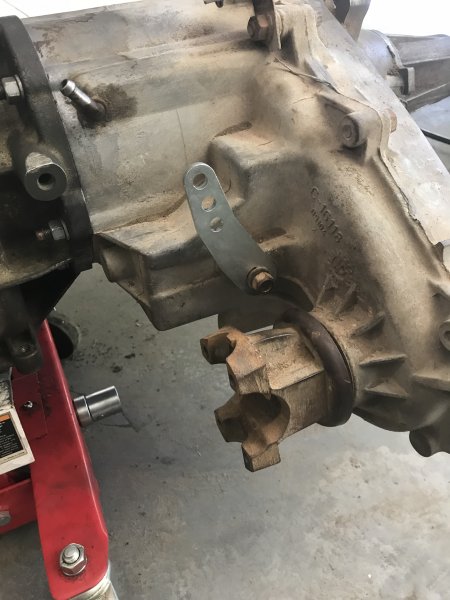
All buttoned up with the new external slave cylinder in place.
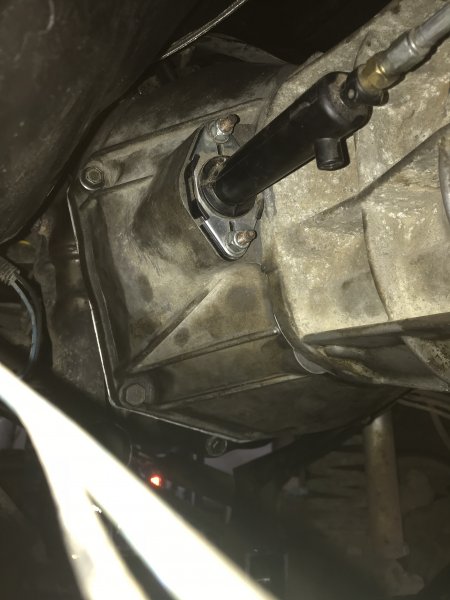