Oh, I could! There are quite a few US/Canada-based options (and at least one German manufacturer). But $30k+ for just the box is pretty high for my budget.
I'm planning to do a more traditionally framed build (wood frame + marine ply + structural foam boards for insulation). I'll probably use fiberglass cloth + epoxy (ie. the West System) on the exterior.
It's all tradeoffs, right? I'm sacrificing a fair bit of my time to have something that's 100% what I want at a lower cost.
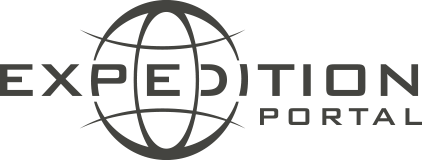
FRP Composite panels ( US Source)
Does anyone know of a US source for the high quality FRP foam composite habitat panels? Just curious if i can buy the panels and build a basic habitat myself. I'm seeing prices of bare habitats in the $30,000-$45,000 range. Are materials really so high now?
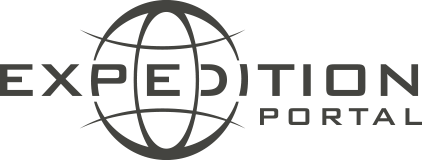
I just posted that as I'm in the same boat. Having a hard time getting my head around a $35,000 box. A box it a pretty simple building design and I'd think someone would be able to make a box for $15,000 with plenty of margin. Not sure how we got to double that in a few years as you could get a kit in the past for $6000. Even a small "professional" should be able to setup templates and jigs to make these reasonably fast.