8sixFabrication
Active member
Tonight I made more progress. It doesn't look like much, but we're slowly chipping away at the list.
On my way home from work, I stopped by my local Napa for a lower radiator hose that fits better. The dude there was kind enough to take the stock one into the back and find me one that was a little better fit. I did have to trim it, but it seems to fit nicely. The stock upper hose seems to fit fine.
I dug out the fan shroud to get the gears rolling on that, and it looks like I will have to pull the radiator to get that modified to fit. So I am shelving that for another day.
Then, I moved on to fiddling with the power steering hose. Put the pump back on and the high pressure line I kept. I got some measurements and made a diagram for the shop I'm dropping stuff off at, to make me a high pressure hose, utilizing the stock banjo end. I want to retain that because it has a sensor in it and I'd like to keep that in tact.
That's about all for about a week or so.
On my way home from work, I stopped by my local Napa for a lower radiator hose that fits better. The dude there was kind enough to take the stock one into the back and find me one that was a little better fit. I did have to trim it, but it seems to fit nicely. The stock upper hose seems to fit fine.
I dug out the fan shroud to get the gears rolling on that, and it looks like I will have to pull the radiator to get that modified to fit. So I am shelving that for another day.
Then, I moved on to fiddling with the power steering hose. Put the pump back on and the high pressure line I kept. I got some measurements and made a diagram for the shop I'm dropping stuff off at, to make me a high pressure hose, utilizing the stock banjo end. I want to retain that because it has a sensor in it and I'd like to keep that in tact.
That's about all for about a week or so.

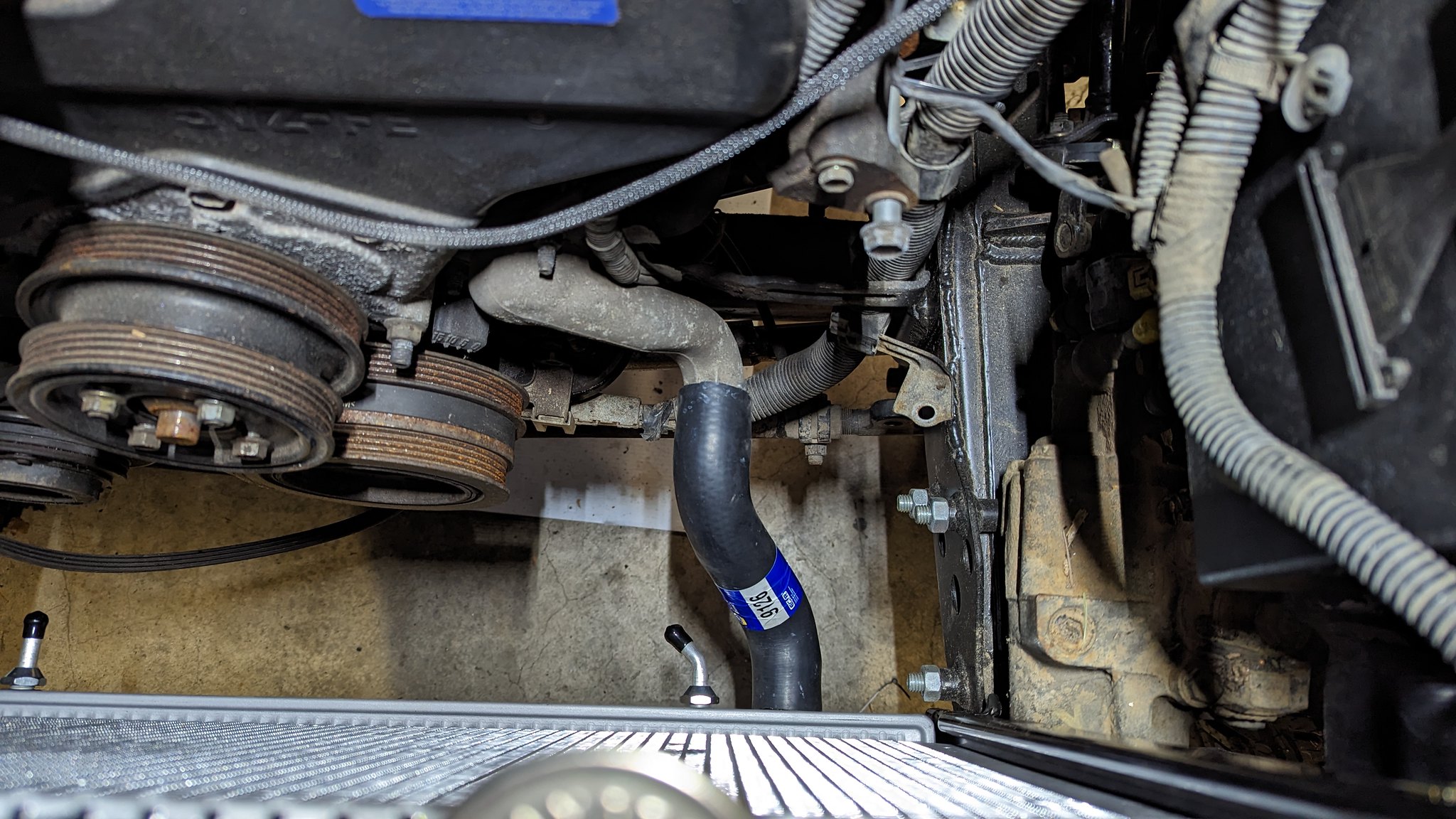
Last edited: