jayshapiro
Adventurer
Eco-Roamer Update
Hi Guys,
OK, here is the long overdue update on the Eco-Roamer project. It's been a packed month...
The truck has spent the past few weeks in Tulsa, Oklahoma with Ron Turner and his guys at Tulsa Truck Manufacturing. They have been working on the 4x4 conversion and stretching out the frame. I can't recommend them enough, as they have been amazingly helpful and Ron has 30yrs of experience which he's been happy to share in advice with me.
I was in the states last week on a business trip, and stopped by Tulsa for a day to see my baby... Here are some latest pics:
4x4 CONVERSION:
We swapped out the Ford front axle for a Meritor 14,000lb drive axle, it's HUUUGE:
The differential is offset to the right hand side.
The truck cab had to be raised substantially to clear the new axle and all the drive parts. (The old axle was U shaped to bend under the cab/transmission.
(Sorry about the dust in the photo - just to give it some scale, those are 43" tires!)
Here's the Meritor transfer case, the whole thing is activated with air solenoids run off the existing compressor for the air-bags and brakes:
Here's the controls they mounted on the dash in the cab. Very clean I think. One activates the 4x4, the other switches between high and low gears:
FRAME EXTENSION:
While the truck is in Tulsa, they also stretched out the frame to make room for the camper box. I really would have preferred to buy a truck from Ford with a solid single frame that was long enough (to save strength) but since we wanted the slightly used 2007 truck (to avoid the emissions changes) we had to take what we could find.
Here's how they did it:
STEP ONE: "The first cut is the deepest"
Slice the existing frame rails, and add length with an angle weld joint. Talk about your scary cuts. Make sure you get the right spot!
STEP TWO: "Make a Sandwich"
Sandwich the joint with another 18" piece of steel to reinforce that section.
STEP THREE: "The L word"
Add 2 pieces of BIG L-Channels running the entire length of the frame (up to just under the cab) to strengthen the entire truck and reduce any frame flex.
STEP FOUR: "Test, Test & Test some more"
They then re-mounted the rear axle in its new position further back, swapped in new gears for the differential and had a new drive shaft custom made to the right length.
Finally, I took a lesson from Joaquim Suave (Thanks!) and decided to do a simple test on the chassis flex. We attached the very rear corner of just one of the frame rails to a chain-block lift in the shop and picked up the rear end by about 3ft.
The deflection between the two frame rails at the rear end was just 1.5 inches, and at the front end (just behind the cab wall) it was only 3/4 inch. I'm really impressed with how much that has stiffened up, and I think that all of our concerns about the dynamic sub-frame mount may not come in to play.
Thank you to everyone who made great suggestions, but given the lack of flex I think we may be ok with some substantial rubber bushings...
Hi Guys,
OK, here is the long overdue update on the Eco-Roamer project. It's been a packed month...
The truck has spent the past few weeks in Tulsa, Oklahoma with Ron Turner and his guys at Tulsa Truck Manufacturing. They have been working on the 4x4 conversion and stretching out the frame. I can't recommend them enough, as they have been amazingly helpful and Ron has 30yrs of experience which he's been happy to share in advice with me.
I was in the states last week on a business trip, and stopped by Tulsa for a day to see my baby... Here are some latest pics:
4x4 CONVERSION:
We swapped out the Ford front axle for a Meritor 14,000lb drive axle, it's HUUUGE:
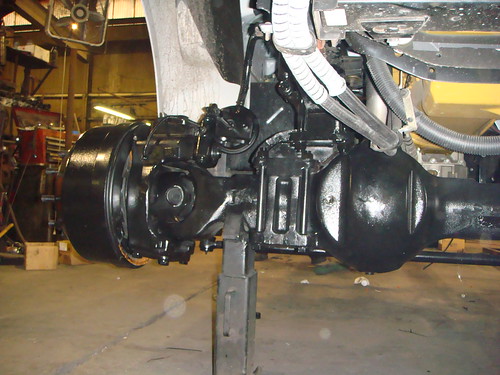
The differential is offset to the right hand side.
The truck cab had to be raised substantially to clear the new axle and all the drive parts. (The old axle was U shaped to bend under the cab/transmission.

(Sorry about the dust in the photo - just to give it some scale, those are 43" tires!)
Here's the Meritor transfer case, the whole thing is activated with air solenoids run off the existing compressor for the air-bags and brakes:

Here's the controls they mounted on the dash in the cab. Very clean I think. One activates the 4x4, the other switches between high and low gears:

FRAME EXTENSION:
While the truck is in Tulsa, they also stretched out the frame to make room for the camper box. I really would have preferred to buy a truck from Ford with a solid single frame that was long enough (to save strength) but since we wanted the slightly used 2007 truck (to avoid the emissions changes) we had to take what we could find.
Here's how they did it:
STEP ONE: "The first cut is the deepest"
Slice the existing frame rails, and add length with an angle weld joint. Talk about your scary cuts. Make sure you get the right spot!


STEP TWO: "Make a Sandwich"
Sandwich the joint with another 18" piece of steel to reinforce that section.


STEP THREE: "The L word"
Add 2 pieces of BIG L-Channels running the entire length of the frame (up to just under the cab) to strengthen the entire truck and reduce any frame flex.

STEP FOUR: "Test, Test & Test some more"
They then re-mounted the rear axle in its new position further back, swapped in new gears for the differential and had a new drive shaft custom made to the right length.

Finally, I took a lesson from Joaquim Suave (Thanks!) and decided to do a simple test on the chassis flex. We attached the very rear corner of just one of the frame rails to a chain-block lift in the shop and picked up the rear end by about 3ft.
The deflection between the two frame rails at the rear end was just 1.5 inches, and at the front end (just behind the cab wall) it was only 3/4 inch. I'm really impressed with how much that has stiffened up, and I think that all of our concerns about the dynamic sub-frame mount may not come in to play.
Thank you to everyone who made great suggestions, but given the lack of flex I think we may be ok with some substantial rubber bushings...