squirelmurphy
Member
I lurked around the site for awhile, getting ideas. When I couldn't take it any longer, the search for the right van began. I finally found what I was looking for in Mesa, Arizona. Not exactly around the block considering that I live in the North OC/Long Beach area of So Cal. It was a bit older than what I had originally set out looking for, but it had everything I was looking for and then some. Plus, the price was right. I drove it back without a single issue. The odometer turned 118k on the ride home.
A few specs on the van, 97 E350 V10, Chateau package, 4.10 gears, barn doors.
Vanessa just happens to be my wife's name. I know you guys love a van pun, so this one became VANessa. Enough talking, meet VANessa...
At the Baja 500 in June. Slept in it for 5 nights.
Parked next to my buddy's class 10 racecar.
Pitting out near Coyote Cals on the Pacific side of the peninsula. The racecar won his class, and the van ran great.
A few specs on the van, 97 E350 V10, Chateau package, 4.10 gears, barn doors.
Vanessa just happens to be my wife's name. I know you guys love a van pun, so this one became VANessa. Enough talking, meet VANessa...
At the Baja 500 in June. Slept in it for 5 nights.
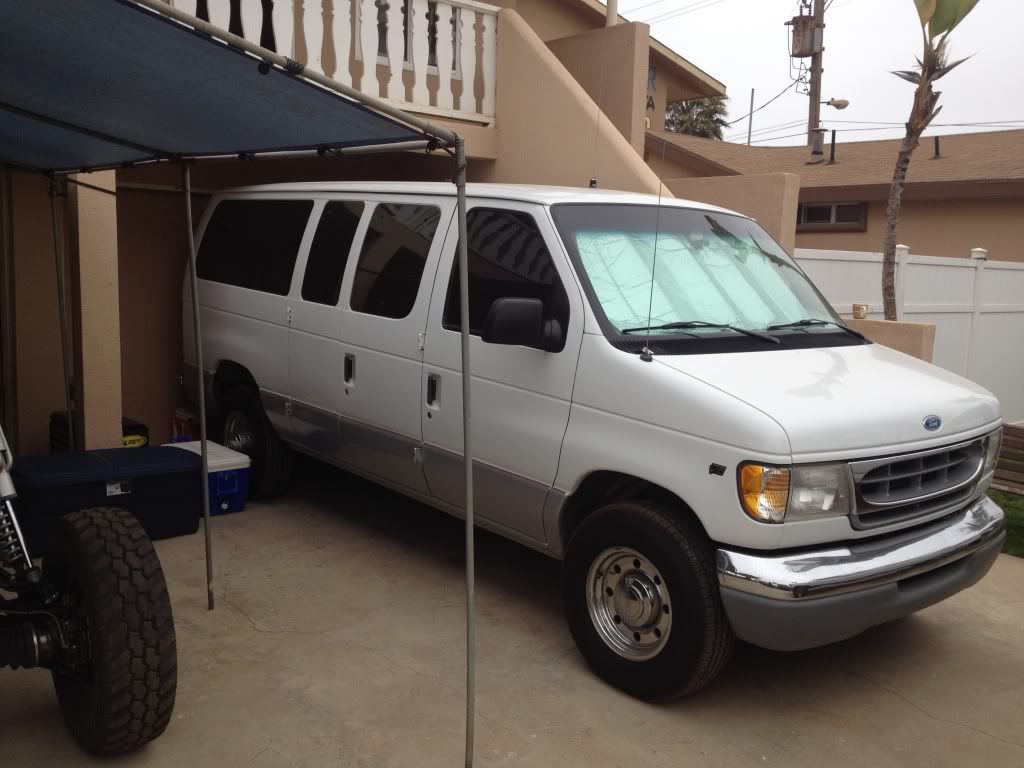
Parked next to my buddy's class 10 racecar.
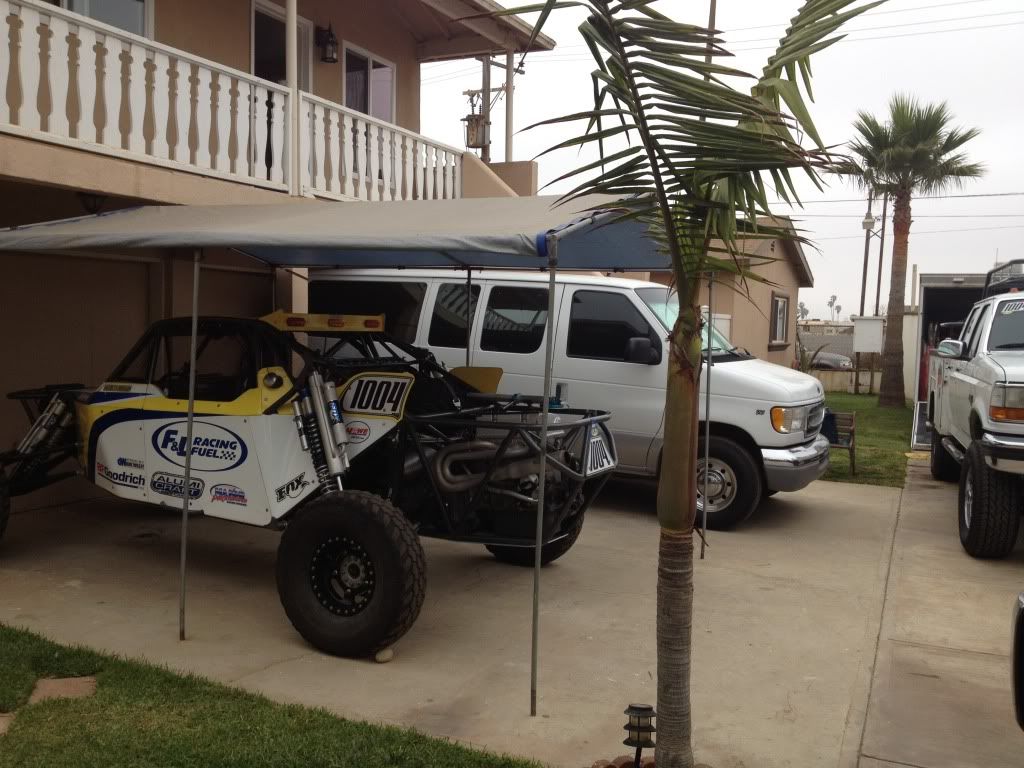
Pitting out near Coyote Cals on the Pacific side of the peninsula. The racecar won his class, and the van ran great.
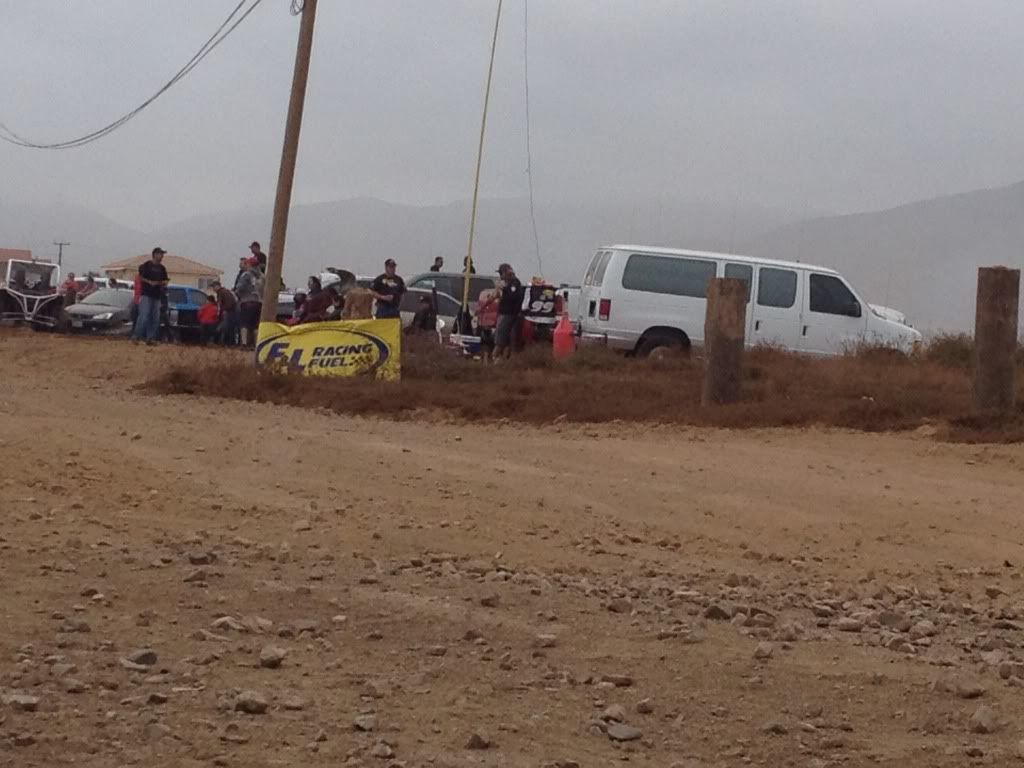