As of posting this on 2/23/15, I've been building my jeep for the last 3 years. I wanted it to take no more than a year at most, but that obviously didn't happen. So, step into my journey of frustration, joy, and reward in seeing my Jeep transform from a totaled mess to what it will hopefully become.
I've always been a jeep guy, I've had a wrangler, scrambler, cherokee, and now another wrangler. For a while I wanted to swap a diesel of some kind into my jeeps, but never had the time or money. To be honest, I still don't, as I attend college full time and work part time, so what little time extra I have I have devoted to my Jeep.
I scanned Davey's Jeep's for a while and finally found a rolled 04' that was mechanically sound, and only had a little body damage, save for the hood, fenders, grill, and roll bar. I ended up selling my cherokee in a hurry and getting the wrangler for a little under 4k. I wanted an LJ for the extra wheel base and space, and I think they look good. This is what I came up with.
I drove up from Tennessee to Ohio with my good friend and trailered it back down here, getting 12mpg up, and a solid 9mpg back down with his Powerstroke f550, haha.
These were the original plans for the build, and they have changed slightly since. This is just the basic setup.
- Cummins 4bt out of a bread van
- Ford ZF5 transmission out of an F250
- Dana 300 transfer case out of a CJ7
- 14bolt and Dana 60 with Detroit lockers out of a CUCV truck
- Clayton Pro series long arms, with 5 inch springs
- H1 double beadlocks, recentered, in 37 inch Goodyear Mt's
- Blue Torch Fab Tube fenders, Genright Corner Armor
- Genright full roll cage.
- Corbeau Seats and harnesses
I got the jeep home, and I began to disassemble it. I didn't really know what I was doing, so I just started taking things apart and putting them in bags.
I completely removed the interior, save for the dash.
I took out both axles, and sold them for $900 on craigslist.
Sold the engine for $1000
Sold the transmission and tranfercase for $350
I sold the wheels and tires, roll bar, and just about everything else I didn't need, coming close to breaking even with the original price of the jeep.
My cousin has a construction company in VA, and he had his crane down here in TN, helping remove some of the downed trees during the tornadoes here several years ago. I got lucky and was able to use it to remove the body.
With the two separated, I was ready to begin some work.
I've always been a jeep guy, I've had a wrangler, scrambler, cherokee, and now another wrangler. For a while I wanted to swap a diesel of some kind into my jeeps, but never had the time or money. To be honest, I still don't, as I attend college full time and work part time, so what little time extra I have I have devoted to my Jeep.
I scanned Davey's Jeep's for a while and finally found a rolled 04' that was mechanically sound, and only had a little body damage, save for the hood, fenders, grill, and roll bar. I ended up selling my cherokee in a hurry and getting the wrangler for a little under 4k. I wanted an LJ for the extra wheel base and space, and I think they look good. This is what I came up with.
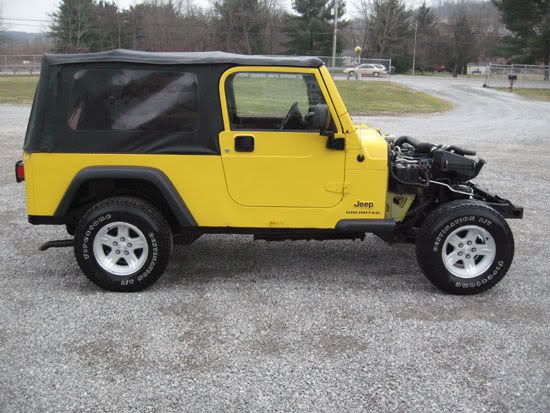
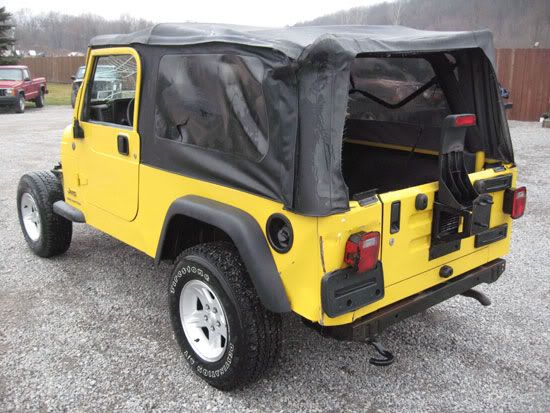
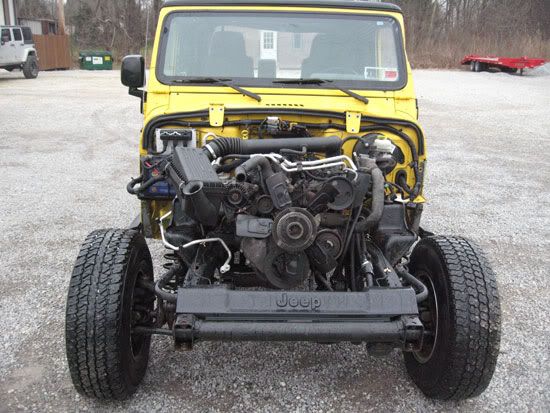
I drove up from Tennessee to Ohio with my good friend and trailered it back down here, getting 12mpg up, and a solid 9mpg back down with his Powerstroke f550, haha.
These were the original plans for the build, and they have changed slightly since. This is just the basic setup.
- Cummins 4bt out of a bread van
- Ford ZF5 transmission out of an F250
- Dana 300 transfer case out of a CJ7
- 14bolt and Dana 60 with Detroit lockers out of a CUCV truck
- Clayton Pro series long arms, with 5 inch springs
- H1 double beadlocks, recentered, in 37 inch Goodyear Mt's
- Blue Torch Fab Tube fenders, Genright Corner Armor
- Genright full roll cage.
- Corbeau Seats and harnesses
I got the jeep home, and I began to disassemble it. I didn't really know what I was doing, so I just started taking things apart and putting them in bags.
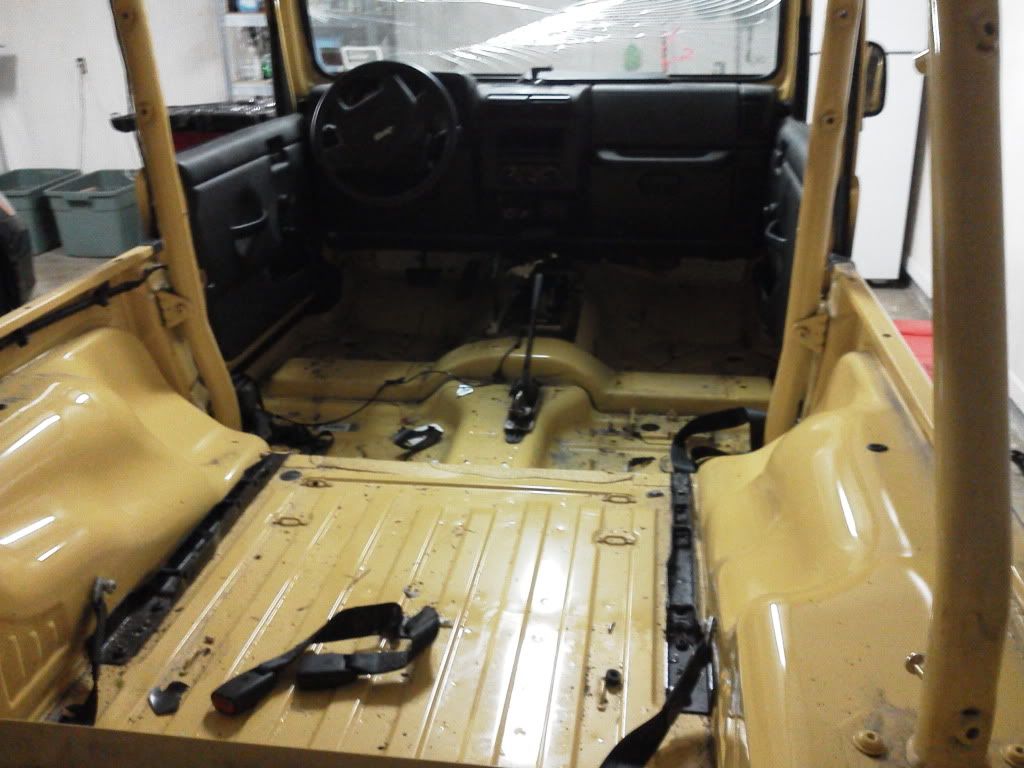
I completely removed the interior, save for the dash.
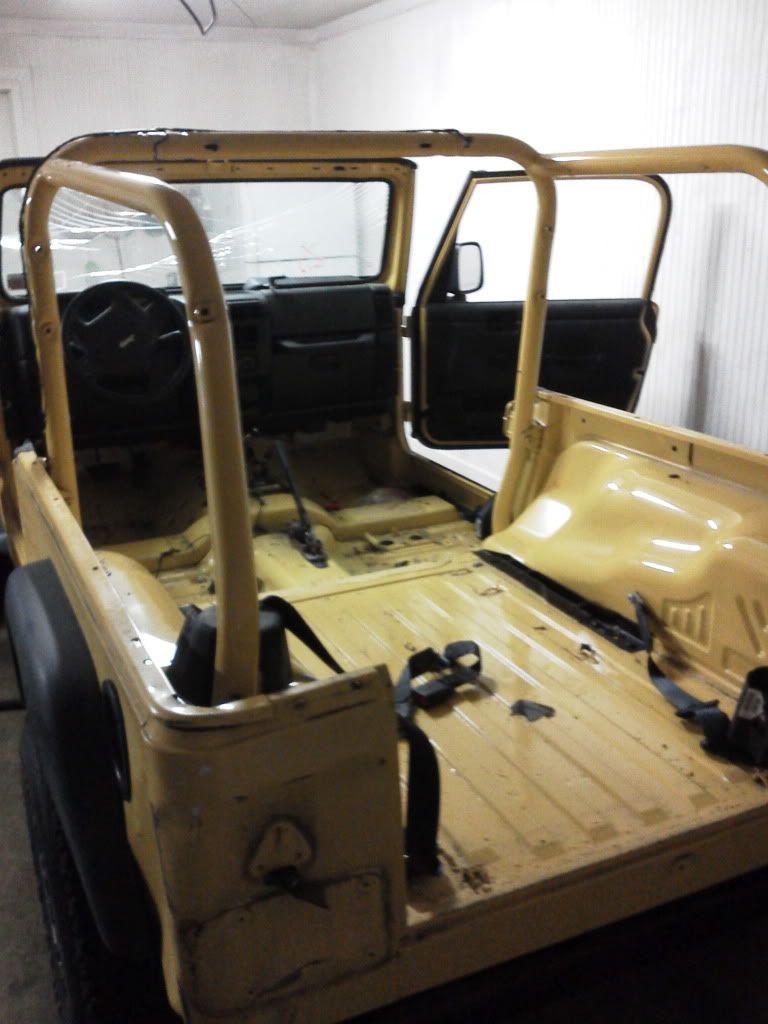
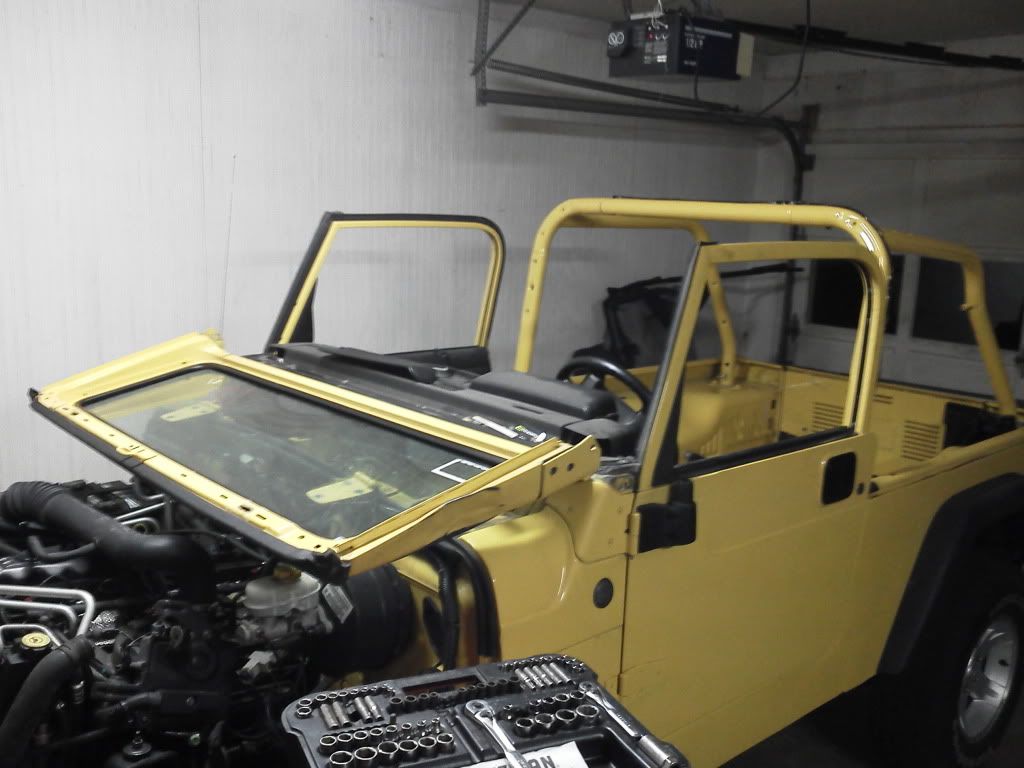
I took out both axles, and sold them for $900 on craigslist.
Sold the engine for $1000
Sold the transmission and tranfercase for $350
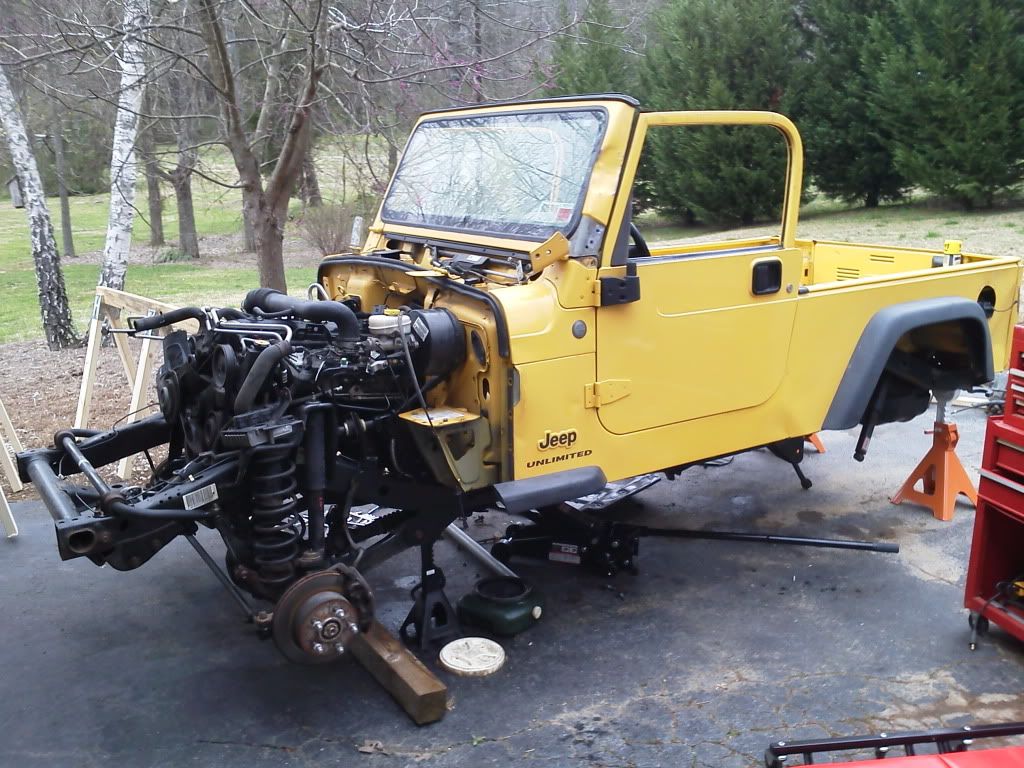
I sold the wheels and tires, roll bar, and just about everything else I didn't need, coming close to breaking even with the original price of the jeep.
My cousin has a construction company in VA, and he had his crane down here in TN, helping remove some of the downed trees during the tornadoes here several years ago. I got lucky and was able to use it to remove the body.
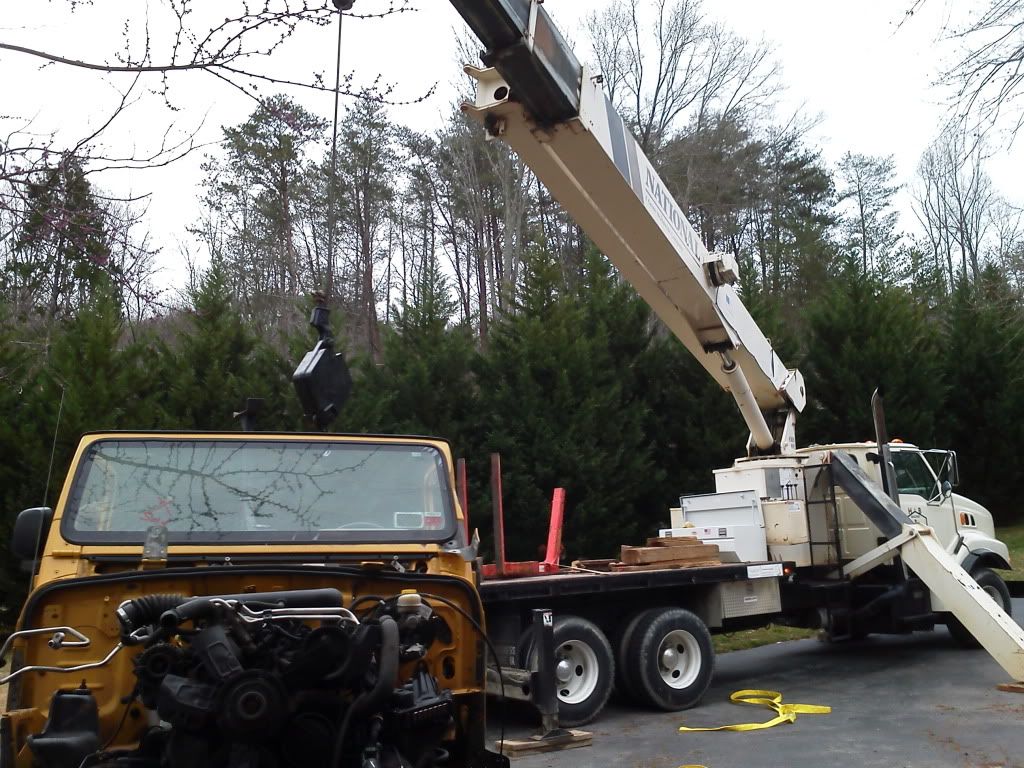


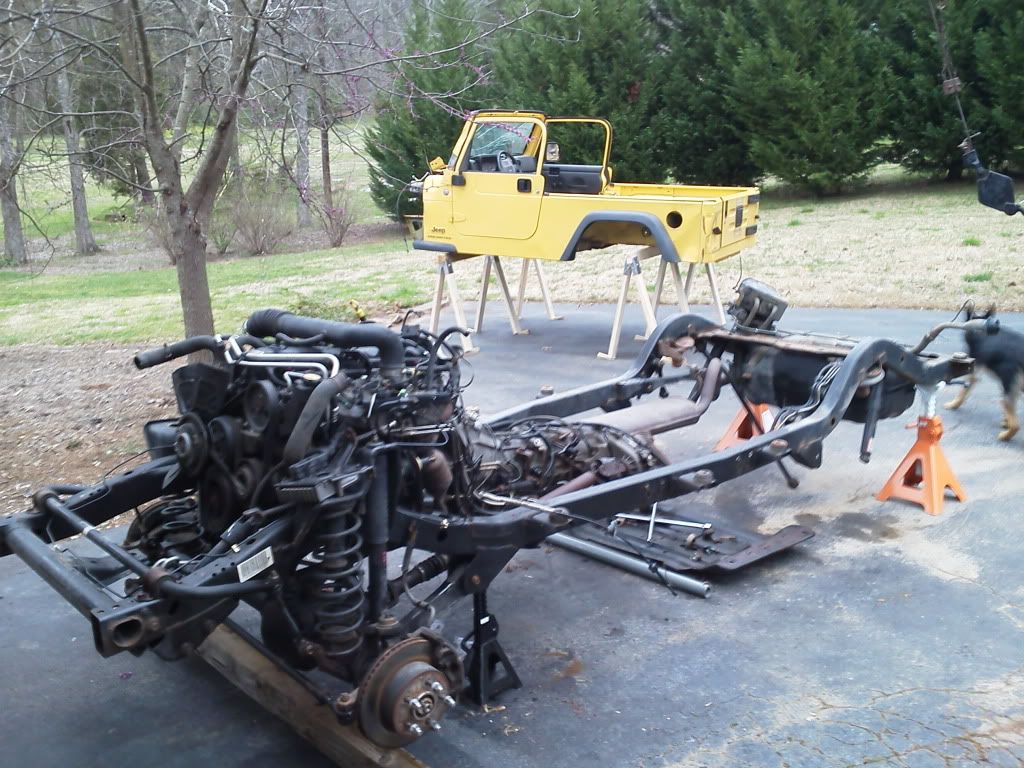
With the two separated, I was ready to begin some work.