4307
Adventurer
G-Day!
I'm 4307 and this is my Canadian flavored Taco. :26_7_2:
The purpose of my build.... " head for the bush! " Overland style.
The project is a Silver, 2004, D-Cab, TRD. Bought it off the lot, new. Actually it was one of three last, new, late 04 D-Cabs available in Canada, before the 05 model change.
I've been lurking in the shadows of Expedition Portal for some time now and occasionally occupy a corner in TTORA land.
I've been driving the truck with stock suspension since day one. I'm a cheap ***. I chose to drive the truck, stock, off road and push it's limits. So far I'm very impressed, errrr! Except for the BFG Rugged trails! They are, what they are! Oh did I mention I was a cheap ***?
Anyway, the real reason it's still stock is budget. I feel more comfortable paying down 3/4's of the payments and keep the Kilometers down to a realistic level until I get the missing parts for the suspension, gears, tires. (sitting @ 55,000km right now).
Before the truck purchase, I've been buying tools, building up a home fab shop (in the basement). Tool shop is my other, other hobby. Now I have the main tools. Its time to build. Building is half the fun for me.
O.K. the cheap *** thing isn't totally true. I'm actually sitting on a pile-O-parts. There's a few goodies in the pile. I'm cheap for not putting them on yet.
ARB bull bar
Donahoe Coilovers
63' Chevy leaf springs ( junkyard specials.... rebuilt them, post to come)
255/ 75R16 Maxxis Bighorns
Ammo can on drawer slide.... Page 1, post # 2 - 7
Leer canopy.
Thule roof rack on the Leer cap
Yakima roof rack over the double cab.
Custom rear bumper.... Page 1-3... post # 8 and counting...
Hi-lift jack and shovel
KEW 8000 budget winch ($300 Cdn). Identical to the Mile Marker PE 8000. If it saves my *** a few times it payed for it's self. We'll see how it holds up.
Xantrex Xpower 1200 power inverter.
Blue Sea fuse box
ARB air compressor
8- 5'' rubber sealed tractor lights. Future rock lights.
A couple of 12v remote control modules. hehehe.... this is pretty cool!
Optima Yellow top. (I've been using it quite a bit as a stand alone, recharging on a charger. Great battery it will be installed in the truck, dual battery.)
Sure Power Battery Isolator
12v lights - for the interior of my truck cap and rear roof rack bar.
Uniden PRO 520 XL CB radio (future home... the ash tray)
K 40 antenna
in cab power inverter.
Cheap rear view camera. hmmm.... should be interesting, Cheapness!
Garmin 60c GPS
Mac GPS Pro software - for Garmin controlled moving map software, Ontario maps @ the moment. Running this on a Mac 17'' Powerbook, a little big for wheeling, but great to look at with the help of a co-pilot (Still in negotiations. Oh Dear can you....)
Other pile-o-parts for a distant future project....
Dana 44 front Wagoneer shop ornament.
K- 10 brakes, calipers
O.K. I have half the parts for a SAS project. I don't want to think of that right now, it's not in my current budget.
Anyway. This coming spring my truck will see the bulk of the transformation. I still need some parts.
This summer I was able to do some fabrication. My free time went to fabricating instead of traveling. Thats O.K. there is always next year.
Here is a pic of my truck the day after I bought it....
At the beach.....
Dorset Ontario....
It's still great to get away in a Stock-o Taco.
I can't wait until spring, too glue all this stuff on.
I wish I had a garage, so I can work on the truck during the winter. Oh well. I'll live!
I'll be posting all my builds as mega posts :sombrero: . I hope thats cool with everyone.
The posts will be step by step format with pics....
Completed projects will have page #'s beside the above mod's list to guide people to the start - finish of the project build, that way the build for particular projects are easier to find. Other wise, it would be a complete pain to flip through every confusing page to find a particular build.
I hope this will make it easier for Expedition portal members.
I will also post my build links from TTORA, so people can view all the questions and comments, good and bad.
If you have questions for me, post in these threads or P.M. me, I'll answer then as soon as I can.
I'm 4307 and this is my Canadian flavored Taco. :26_7_2:
The purpose of my build.... " head for the bush! " Overland style.
The project is a Silver, 2004, D-Cab, TRD. Bought it off the lot, new. Actually it was one of three last, new, late 04 D-Cabs available in Canada, before the 05 model change.
I've been lurking in the shadows of Expedition Portal for some time now and occasionally occupy a corner in TTORA land.
I've been driving the truck with stock suspension since day one. I'm a cheap ***. I chose to drive the truck, stock, off road and push it's limits. So far I'm very impressed, errrr! Except for the BFG Rugged trails! They are, what they are! Oh did I mention I was a cheap ***?
Anyway, the real reason it's still stock is budget. I feel more comfortable paying down 3/4's of the payments and keep the Kilometers down to a realistic level until I get the missing parts for the suspension, gears, tires. (sitting @ 55,000km right now).
Before the truck purchase, I've been buying tools, building up a home fab shop (in the basement). Tool shop is my other, other hobby. Now I have the main tools. Its time to build. Building is half the fun for me.
O.K. the cheap *** thing isn't totally true. I'm actually sitting on a pile-O-parts. There's a few goodies in the pile. I'm cheap for not putting them on yet.
ARB bull bar
Donahoe Coilovers
63' Chevy leaf springs ( junkyard specials.... rebuilt them, post to come)
255/ 75R16 Maxxis Bighorns
Ammo can on drawer slide.... Page 1, post # 2 - 7
Leer canopy.
Thule roof rack on the Leer cap
Yakima roof rack over the double cab.
Custom rear bumper.... Page 1-3... post # 8 and counting...
Hi-lift jack and shovel
KEW 8000 budget winch ($300 Cdn). Identical to the Mile Marker PE 8000. If it saves my *** a few times it payed for it's self. We'll see how it holds up.
Xantrex Xpower 1200 power inverter.
Blue Sea fuse box
ARB air compressor
8- 5'' rubber sealed tractor lights. Future rock lights.
A couple of 12v remote control modules. hehehe.... this is pretty cool!
Optima Yellow top. (I've been using it quite a bit as a stand alone, recharging on a charger. Great battery it will be installed in the truck, dual battery.)
Sure Power Battery Isolator
12v lights - for the interior of my truck cap and rear roof rack bar.
Uniden PRO 520 XL CB radio (future home... the ash tray)
K 40 antenna
in cab power inverter.
Cheap rear view camera. hmmm.... should be interesting, Cheapness!
Garmin 60c GPS
Mac GPS Pro software - for Garmin controlled moving map software, Ontario maps @ the moment. Running this on a Mac 17'' Powerbook, a little big for wheeling, but great to look at with the help of a co-pilot (Still in negotiations. Oh Dear can you....)
Other pile-o-parts for a distant future project....
Dana 44 front Wagoneer shop ornament.
K- 10 brakes, calipers
O.K. I have half the parts for a SAS project. I don't want to think of that right now, it's not in my current budget.
Anyway. This coming spring my truck will see the bulk of the transformation. I still need some parts.
This summer I was able to do some fabrication. My free time went to fabricating instead of traveling. Thats O.K. there is always next year.
Here is a pic of my truck the day after I bought it....
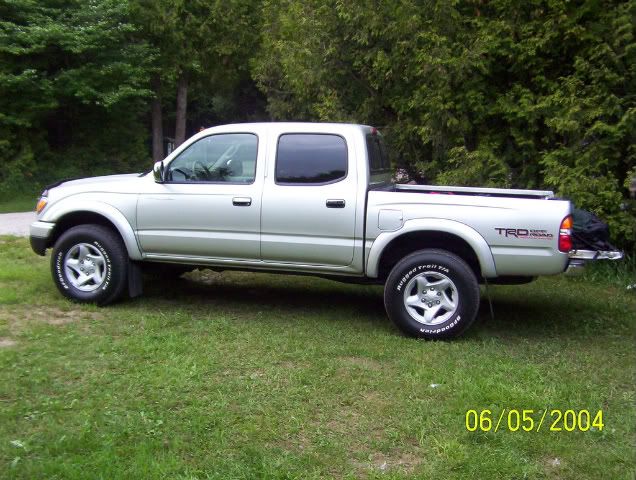
At the beach.....
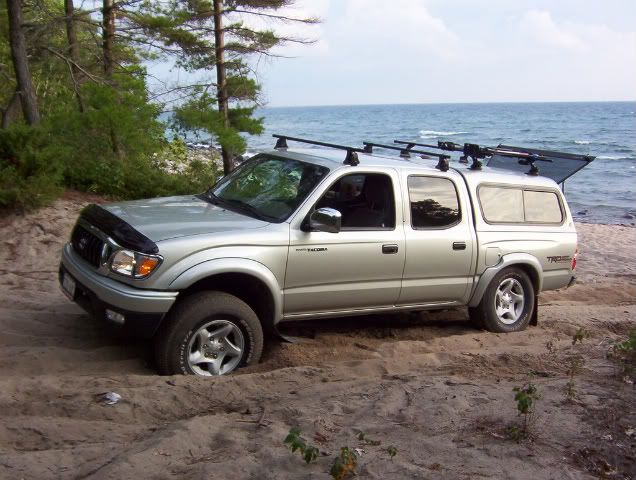
Dorset Ontario....
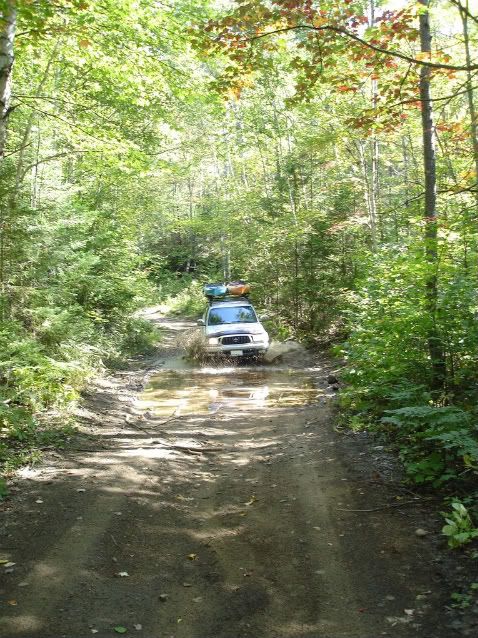
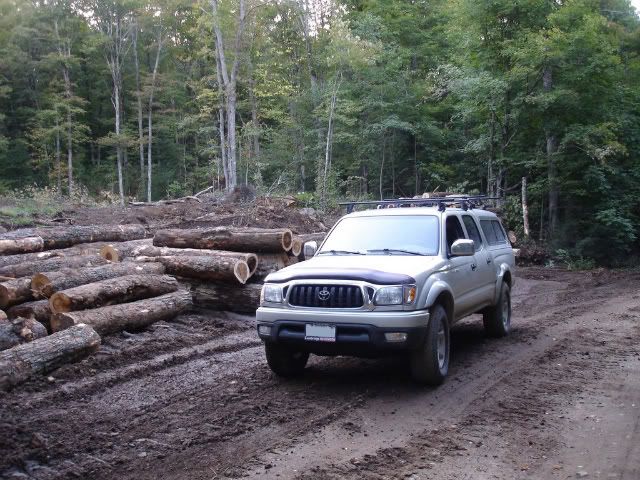
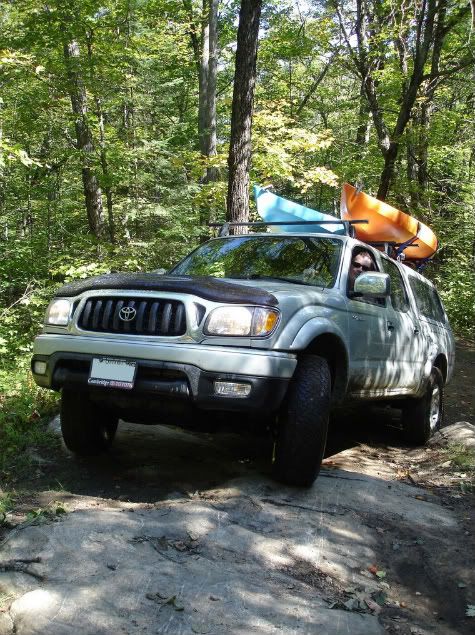
It's still great to get away in a Stock-o Taco.
I can't wait until spring, too glue all this stuff on.
I wish I had a garage, so I can work on the truck during the winter. Oh well. I'll live!
I'll be posting all my builds as mega posts :sombrero: . I hope thats cool with everyone.
Completed projects will have page #'s beside the above mod's list to guide people to the start - finish of the project build, that way the build for particular projects are easier to find. Other wise, it would be a complete pain to flip through every confusing page to find a particular build.
I hope this will make it easier for Expedition portal members.
I will also post my build links from TTORA, so people can view all the questions and comments, good and bad.
If you have questions for me, post in these threads or P.M. me, I'll answer then as soon as I can.
Last edited: