4307
Adventurer
Finally it's time to weld the angle plate pieces in place, to box up the bumper and get the bumper shape I was after.
The plate pieces tacked in place. The pieces butt up together create a ''V'' this gave me the opportunity to get deeper weld penetration.
With a deeper weld penetration I could grind the weld too a smooth shape without loosing too much weld integrity. All the plate welds on the front of the bumper were treated this way. I would only grind off enough weld to smooth them out.
Now, its time to tame the bumper corners, make it less of a weapon.....
Earlier I mentioned I was planning to trim the rear bed quarter panels for higher clearance and add side protection using 2'' square tube. This is still in the design stage. Although I did get a head start.
As mentioned earlier, I was going to mount the square tube, square to the ground, but instead I decided to clock the tube 45*, just too be different....
I was going to "weld in" full length tube to meet the edge of the wheel well, but decided to make the side protection detachable. This would make the bumper easier to man handle during the install, and removable incase I need to replace or change side protection, or just leave the bumpity bump the way it is without side protection. I like having these options. I have all winter to think about it.
Now, this is my plan too make it all fit together and make it one unit, strong enough to carry the weight of the truck using the Hi-Lift on the side protection....
I'm still using the 2'' tube, clocked to 45*, from the bumper too the wheel well. The side protection tube on the bumper end will have a short inner square tube just big enough to fit inside the 2'' tube and weld in place to make it one piece. This inner tube will be slightly protruding out of the 2'' tube, enough to fit into the 2'' tubed corner of the bumper, It will be bolted in place possibly welded later in life. The intersecting side protection and bumper corner will be strong enough to carry the truck weight with the jack. Have I lost you yet? LOL!
Here is a picture of the back side of the bumper corner to give you some idea. Like I said the side pro. is still in the design stage. If I decide to keep the bumper as is, without side protection, I can simply cap off the open corner so animals don't nest in there. I could weld in a thin plate or cap it off using trailer hitch receiver plastic caps. I'll mount the bumper in the spring and plastic cap the corners until the side protection is done ready for install.
The plate pieces tacked in place. The pieces butt up together create a ''V'' this gave me the opportunity to get deeper weld penetration.
With a deeper weld penetration I could grind the weld too a smooth shape without loosing too much weld integrity. All the plate welds on the front of the bumper were treated this way. I would only grind off enough weld to smooth them out.
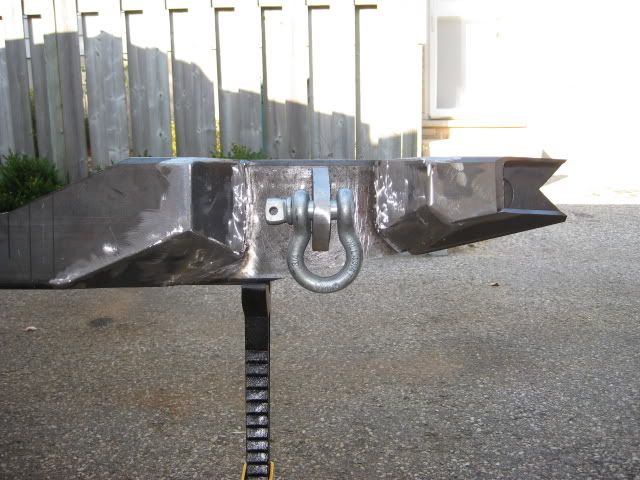
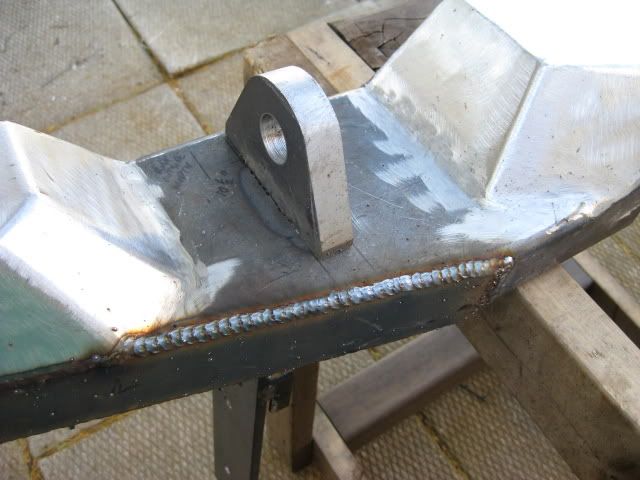
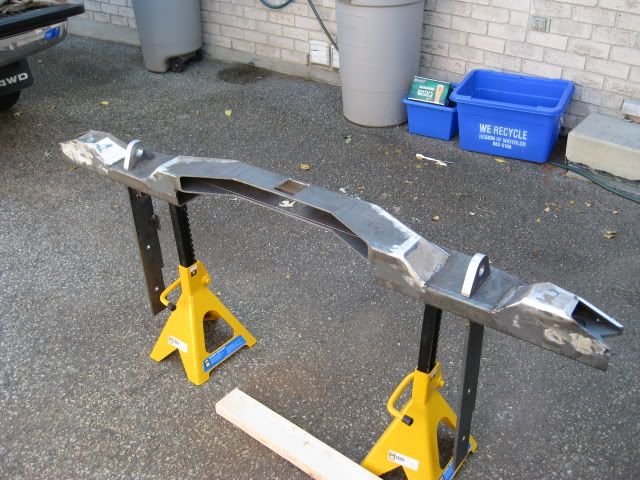
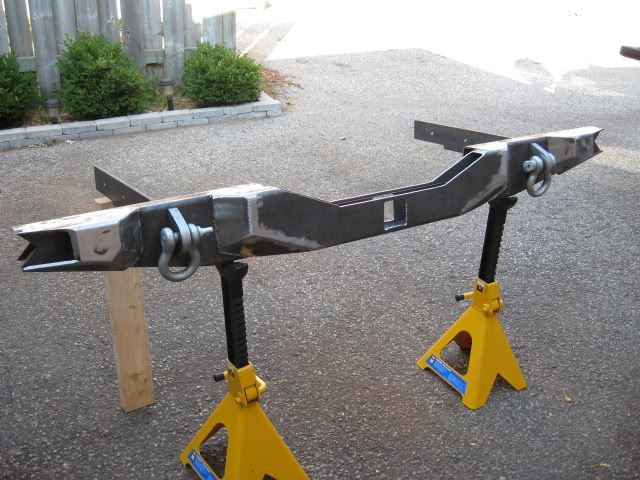
Now, its time to tame the bumper corners, make it less of a weapon.....
Earlier I mentioned I was planning to trim the rear bed quarter panels for higher clearance and add side protection using 2'' square tube. This is still in the design stage. Although I did get a head start.
As mentioned earlier, I was going to mount the square tube, square to the ground, but instead I decided to clock the tube 45*, just too be different....
I was going to "weld in" full length tube to meet the edge of the wheel well, but decided to make the side protection detachable. This would make the bumper easier to man handle during the install, and removable incase I need to replace or change side protection, or just leave the bumpity bump the way it is without side protection. I like having these options. I have all winter to think about it.
Now, this is my plan too make it all fit together and make it one unit, strong enough to carry the weight of the truck using the Hi-Lift on the side protection....
I'm still using the 2'' tube, clocked to 45*, from the bumper too the wheel well. The side protection tube on the bumper end will have a short inner square tube just big enough to fit inside the 2'' tube and weld in place to make it one piece. This inner tube will be slightly protruding out of the 2'' tube, enough to fit into the 2'' tubed corner of the bumper, It will be bolted in place possibly welded later in life. The intersecting side protection and bumper corner will be strong enough to carry the truck weight with the jack. Have I lost you yet? LOL!
Here is a picture of the back side of the bumper corner to give you some idea. Like I said the side pro. is still in the design stage. If I decide to keep the bumper as is, without side protection, I can simply cap off the open corner so animals don't nest in there. I could weld in a thin plate or cap it off using trailer hitch receiver plastic caps. I'll mount the bumper in the spring and plastic cap the corners until the side protection is done ready for install.
