jscherb
Expedition Leader
I block sanded the high-build primer yesterday and no additional imperfections were revealed, so this morning I shot two coats of epoxy primer to seal the high-build followed by several coats of clear. I'll let the clear harden up a few days and then the master will be ready to have the mold made from it.
So here's how the wooden master turned out - looking at the reflections in the gloss will give you an idea how the block sanding and finishing worked out...
Once the mold is made, the parts I make in that mold will look exactly like the photos above, except the parts will be fiberglass instead of wood
.
So here's how the wooden master turned out - looking at the reflections in the gloss will give you an idea how the block sanding and finishing worked out...
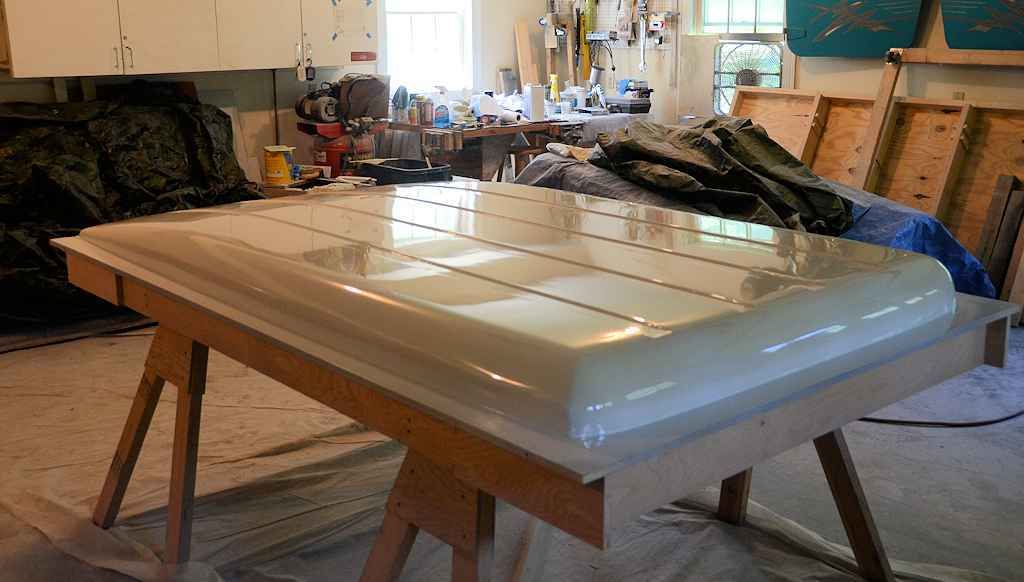
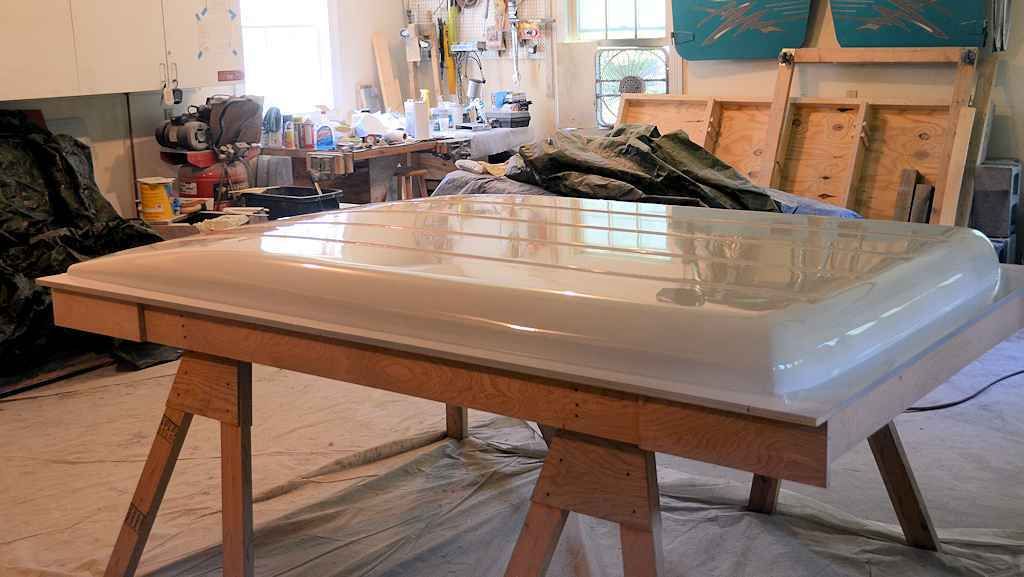
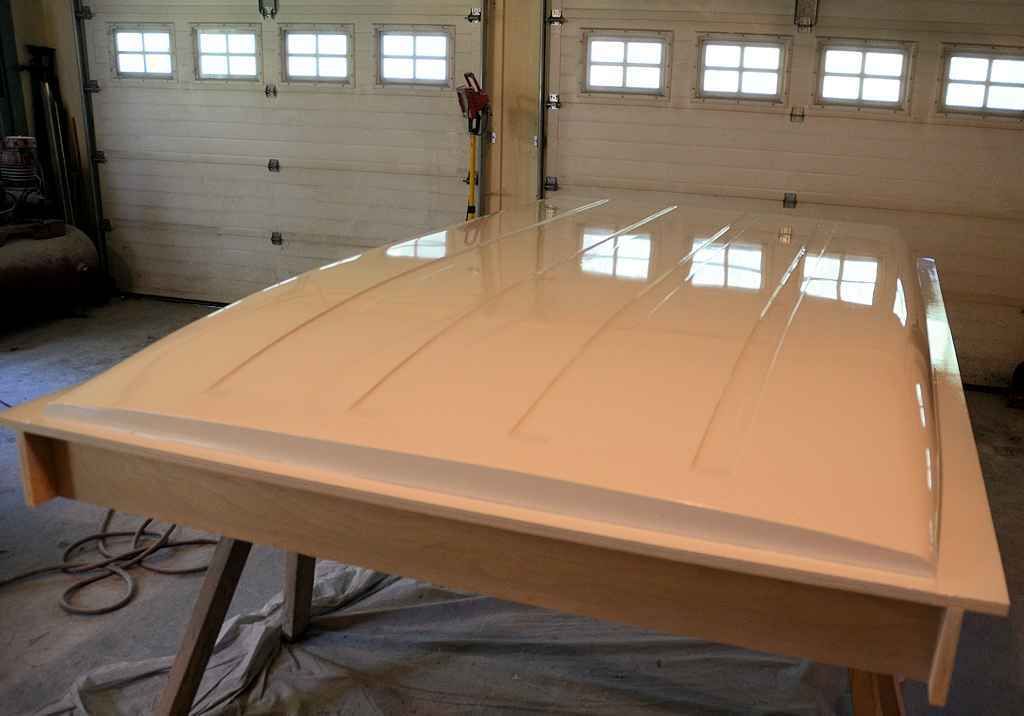
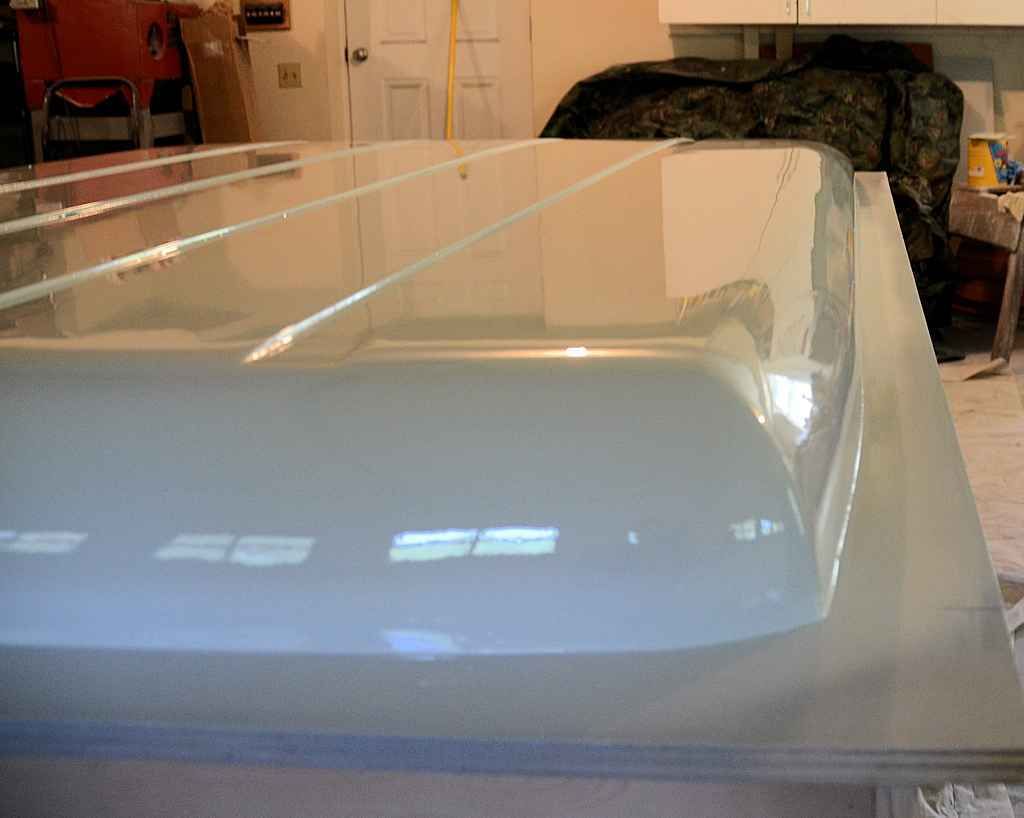
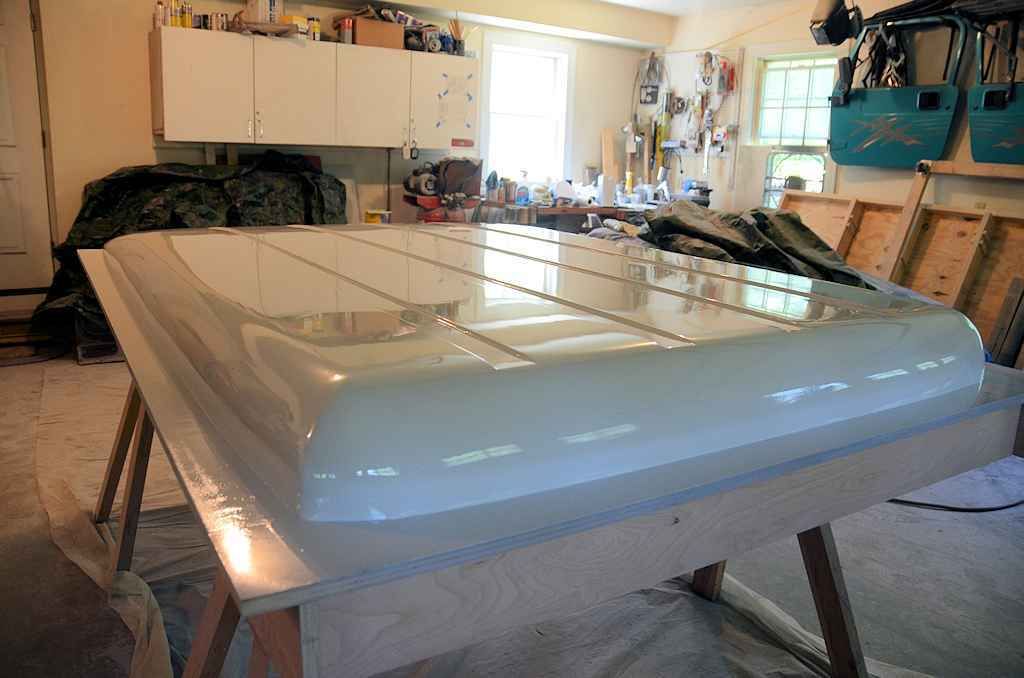
Once the mold is made, the parts I make in that mold will look exactly like the photos above, except the parts will be fiberglass instead of wood
Last edited: