MikeBabs
New member
I realized that I made my original post in the wrong forum, so I am restarting here. You can view the original post here:
expeditionportal.com
Before I begin, huge shoutout to @97heavyweight for documenting his build, I referenced it extensively.
You can check his build out here:
expeditionportal.com
First of all, the camper had to be Light Weight due to the limited weight capacity of the truck - Limited compared to a 3/4 or 1 ton. As such, materials like Steel, Wood, etc. were out, Aluminum was what I chose
Second, this had to be low budget.... ie. much less than it would cost me to buy a project M, or something similar (so under $10,000cdn)
(Oh, and I chose to do a popup to save weight and keep ground clearance reasonable).
I was doing a ton of research on building with aluminum till I came across this build thread where @97heavyweight built a camper with 8020.
expeditionportal.com
It was more expensive than aluminum but since I didn't have a way to weld aluminum, 8020 seemed the way to go. But what really sold me on it were the free tools I found!
FrameXpert and the "Tech Toolkit" from 8020!
8020.net
Why was the Tool Kit critical to me? Because this program gives me the ability to do deflection tests for the cantilever part of the build with various loads and lengths. I wasn't able to find anything like this for boxed aluminum, so this pretty much sealed the deal for me choosing to go with 8020 style extrusion.
I started my design with the cantilever part of the design and worked my way from there. Using Tech Toolkit, I figured out the loading and what I wanted my maximum deflection to be.
View attachment 734957
This gave me the profile of 8020 that I needed as well as the length of the cantilever. from there I added supports down to the truck bed and enclosed it.
View attachment 734958
I went with a flip or full-width access door for weight and simplicity. I also designed this so I can take the tailgate off, enclose the back and put in an RV door if I so desire.
I decided to run a support down to the truck bed to take some of the weight loading off the bedsides and transfer it down to the truck bed.
Lastly, I used 1.5x3" for the roof to give it rigidity and braced it with 2 horizontal supports. If this ends up being flimsy, then I can easily add more support. Another benefit of using 8020.
View attachment 734959View attachment 734960View attachment 734961
So that the design of the camper structure.
The next step was sourcing the 8020. This proved to be a big challenge as I am not located anywhere near a big city. After an extensive google search, I came across Faztek in Canada.
www.faztek.ca
The pricing was better than 8020 and the shipping wasn't too bad. Plus they had black anodized extrusions in stock, which I was a fan of especially since that didn't cost much more. But the big drawback aside from the shipping costs, was the fact they only shipped up to 97" lengths and I needed 110" for my main support beams. So, after a lot of thought, I decided to order the longest continuous length I could and then use a ton of butt joints and plates to secure the pieces together. Not overly happy with this, but there shouldn’t be too much force at that point of the frame as I have a support leg placed before the joint (This location will vary and I might even change it to a 1530 support spanning the joint.
From here I will be siding the camper with .040 aluminum, mostly because I cannot find ACM (Aluminum comp panels) anywhere near me.
I will be using 1/2" or 3/4" plywood for the sleeping area and will be custom-making a 6" foam bed to be full width and 80" long. so, somewhere between a Queen and a King mattress.
I do have a removable panel that supports approximately 3 feet of the bed that can be easily removed and pushed to the forward part of the camper when the top is deployed. This gives me the full dimensions of the bed as a living space when not in sleeping mode. I am planning on designing the foam here to be used as cushions on a bench or seats below.
The interior will be designed after the camper is built; I have designed this camper to give me the max amount of space for the least amount of weight so the interior will be determined after the shell is built, the truck is weighted and I see how much axle payload I have remaining.
Where I better at CAD, I probably should have designed this all in Sketch up and planned out every little detail. But I am not good at CAD and not about to tackle that learning curve just for this project. lol
So, I'm sure I am leaving a ton of questions unanswered, so please feel free to ask away in the comments section and I will do my best to address them!
I am also documenting this build on YouTube if you'd like to follow along:
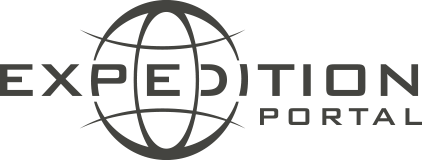
DIY 8020 Pop-up Topper Build (2014 GMC Sierra 1500)
Hi all! I have started the process of building a pop up topper for my truck and thought I'd share the progress. I will be videoing my progress on YouTube but I don't think I can post the links here so I'll just be posting written updates with photos. My truck is a 2014 GMC Sierra 1500 and...
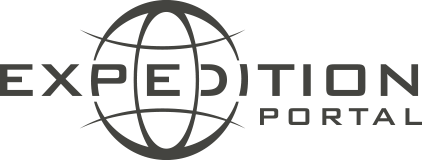
Before I begin, huge shoutout to @97heavyweight for documenting his build, I referenced it extensively.
You can check his build out here:
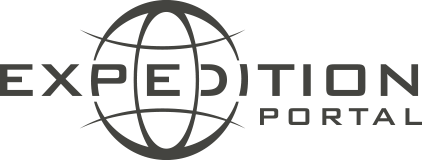
I decided to build my own Pop Top camper
Last November I started to plan out a custom built pop top camper. In January I started the build. The following is a collection of pictures and thoughts of my build. So I do not know how to weld very well and I certainly don't know how to weld aluminum. So I decided to do my build with 80/20...
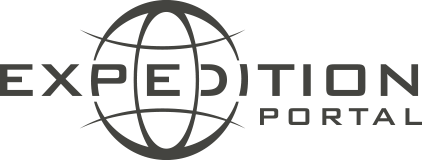
First of all, the camper had to be Light Weight due to the limited weight capacity of the truck - Limited compared to a 3/4 or 1 ton. As such, materials like Steel, Wood, etc. were out, Aluminum was what I chose
Second, this had to be low budget.... ie. much less than it would cost me to buy a project M, or something similar (so under $10,000cdn)
(Oh, and I chose to do a popup to save weight and keep ground clearance reasonable).
I was doing a ton of research on building with aluminum till I came across this build thread where @97heavyweight built a camper with 8020.
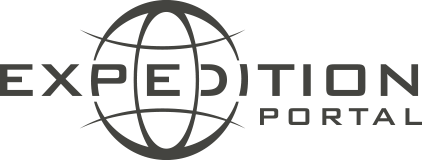
I decided to build my own Pop Top camper
Last November I started to plan out a custom built pop top camper. In January I started the build. The following is a collection of pictures and thoughts of my build. So I do not know how to weld very well and I certainly don't know how to weld aluminum. So I decided to do my build with 80/20...
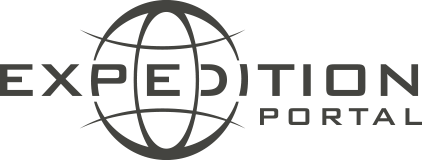
It was more expensive than aluminum but since I didn't have a way to weld aluminum, 8020 seemed the way to go. But what really sold me on it were the free tools I found!
FrameXpert and the "Tech Toolkit" from 8020!
80/20 Tech Toolkit | 80/20 T-Slot Aluminum Extrusions | 80/20, Inc.
The Tech Toolkit speeds up design time, assists in profile and fastening methods, creates custom miter drawings, analyzes design criteria, and converts units of measure. It is in one convenient download and provides access to the conversion and deflection calculators as well as the miter cut...

Why was the Tool Kit critical to me? Because this program gives me the ability to do deflection tests for the cantilever part of the build with various loads and lengths. I wasn't able to find anything like this for boxed aluminum, so this pretty much sealed the deal for me choosing to go with 8020 style extrusion.
I started my design with the cantilever part of the design and worked my way from there. Using Tech Toolkit, I figured out the loading and what I wanted my maximum deflection to be.
View attachment 734957
This gave me the profile of 8020 that I needed as well as the length of the cantilever. from there I added supports down to the truck bed and enclosed it.
View attachment 734958
I went with a flip or full-width access door for weight and simplicity. I also designed this so I can take the tailgate off, enclose the back and put in an RV door if I so desire.
I decided to run a support down to the truck bed to take some of the weight loading off the bedsides and transfer it down to the truck bed.
Lastly, I used 1.5x3" for the roof to give it rigidity and braced it with 2 horizontal supports. If this ends up being flimsy, then I can easily add more support. Another benefit of using 8020.
View attachment 734959View attachment 734960View attachment 734961
So that the design of the camper structure.
The next step was sourcing the 8020. This proved to be a big challenge as I am not located anywhere near a big city. After an extensive google search, I came across Faztek in Canada.
www.faztek.ca
The pricing was better than 8020 and the shipping wasn't too bad. Plus they had black anodized extrusions in stock, which I was a fan of especially since that didn't cost much more. But the big drawback aside from the shipping costs, was the fact they only shipped up to 97" lengths and I needed 110" for my main support beams. So, after a lot of thought, I decided to order the longest continuous length I could and then use a ton of butt joints and plates to secure the pieces together. Not overly happy with this, but there shouldn’t be too much force at that point of the frame as I have a support leg placed before the joint (This location will vary and I might even change it to a 1530 support spanning the joint.
From here I will be siding the camper with .040 aluminum, mostly because I cannot find ACM (Aluminum comp panels) anywhere near me.
I will be using 1/2" or 3/4" plywood for the sleeping area and will be custom-making a 6" foam bed to be full width and 80" long. so, somewhere between a Queen and a King mattress.
I do have a removable panel that supports approximately 3 feet of the bed that can be easily removed and pushed to the forward part of the camper when the top is deployed. This gives me the full dimensions of the bed as a living space when not in sleeping mode. I am planning on designing the foam here to be used as cushions on a bench or seats below.
The interior will be designed after the camper is built; I have designed this camper to give me the max amount of space for the least amount of weight so the interior will be determined after the shell is built, the truck is weighted and I see how much axle payload I have remaining.
Where I better at CAD, I probably should have designed this all in Sketch up and planned out every little detail. But I am not good at CAD and not about to tackle that learning curve just for this project. lol
So, I'm sure I am leaving a ton of questions unanswered, so please feel free to ask away in the comments section and I will do my best to address them!
I am also documenting this build on YouTube if you'd like to follow along: