Switch
Observer
I didn't like any of the portable grills available for sale. The good ones were bulky and expensive and the cheap ones were, well, cheap. I wanted something lightweight and compact but not flimsy, that had an adjustable grill height, and that could be covered to keep the heat in and the rain out.
When I built this I just wanted to see if it worked & planned to do a larger one in stainless steel. But I've been using this for over a year now and it works much better than I expected so I haven't seen the need to make another. I've used this to make dinner for up to 6 adults but it is better suited for 4 or 5 people. It is very efficient using few coals and cooking faster.
This measures 25 x 33 by 5 cm when packed up and weighs 4.5 kg. The top and double bottom are 1/4 sized aluminum cookie sheets. The second cookie sheet on the bottom keeps the bottom from getting to hot. The sides are 22 gauge steel.
The tools required to make this were: drill, reciprocating saw, pop-rivet gun and a file.
It takes about a minute and a half to assemble.
6:20 PM Just started the coals.
The sides are attached to the back by piano hinges using pop-rivets. The front is held in place by two tabs that latch onto screw posts. Once assembled its dimensions are 25 x 33 by 30 cm . I painted the sides with Rust-Oleum High Temperature black paint.
6:45 The coals are ready.
There are air holes along the bottom on all four sides. The coals rest are on 13 gauge expanded metal.
The cooking surface is also 13 gauge expanded metal. It rests on two stainless steel tubes that have press fitted washers to keep them snug in the slide channels for raising and lowering the grill. The handles are ½” wood dowel fitted into skewers that slide into the stainless steel tubes.
Here, the grill is on the lowest setting, just above the coals. Great for squeezing that last bit of heat from the dying coals.
The Front is hinged to completely enclose the grill.
Here's a close up of the handle and slot for changing grill height. You can also see the air holes at the bottom and the latch the secures the front to the screw post.
Here is a close up of the inside. You can see the press-fitted washer that secures the stainless steel grill rod and the piano hinge that allows the front to fold down.
Time to grill up some tri-tip!
The grill can be completely enclosed by adding the top cookie sheet. The temperature inside is hotter than 220 degrees F - that's as high as my thermometer goes. Here you can also see a pair of skewers that support the expanded metal that the coals rest on.
The top cookie sheet can also be set at an angle so the door can be opened.
7:00 PM First side is done.
The expanded metal is difficult to clean but it has the advantage of letting you grill veggies that tend to fall between traditional grill bars.
Here you can see the bottom cookie sheet.
I use two cookie sheets on the bottom to provide enough insulation to keep the bottom from getting too hot. It would have been easy enough to fabricate a stand but I use the cookie sheets for other purposes.
Here is tonight's eggplant. Even though the grill surface is only 8 x 12, it can grill 5 large hamburgers. I just had to stack them and rotate which one was on bottom until they had shrunk so that I could grill them side by side. I did the same thing with the eggplant.
Bon Appétit!
When I built this I just wanted to see if it worked & planned to do a larger one in stainless steel. But I've been using this for over a year now and it works much better than I expected so I haven't seen the need to make another. I've used this to make dinner for up to 6 adults but it is better suited for 4 or 5 people. It is very efficient using few coals and cooking faster.
This measures 25 x 33 by 5 cm when packed up and weighs 4.5 kg. The top and double bottom are 1/4 sized aluminum cookie sheets. The second cookie sheet on the bottom keeps the bottom from getting to hot. The sides are 22 gauge steel.
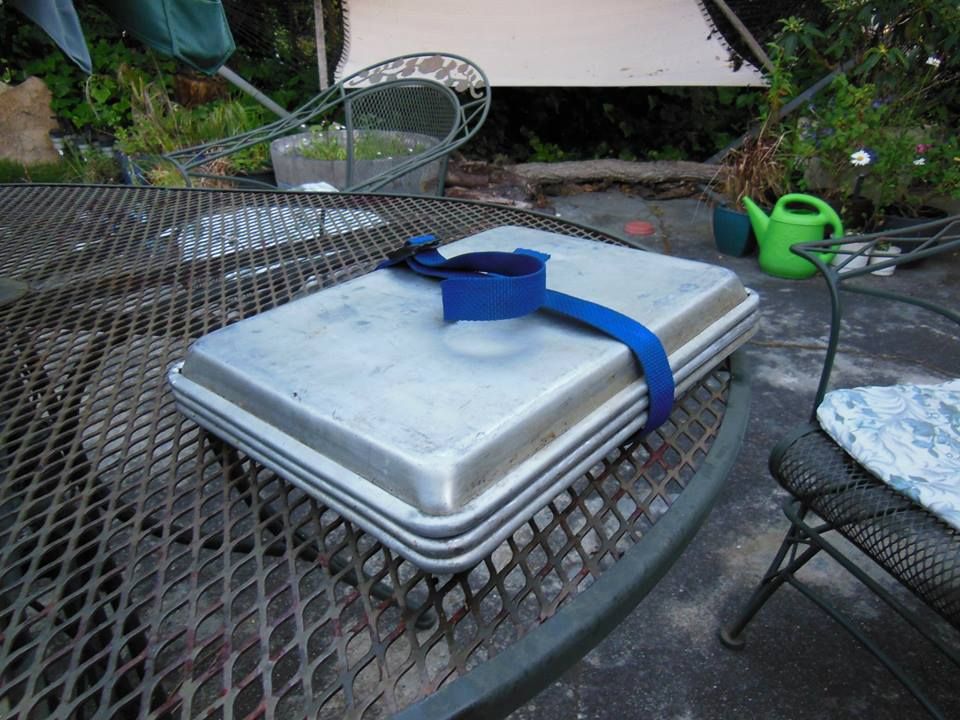
The tools required to make this were: drill, reciprocating saw, pop-rivet gun and a file.
It takes about a minute and a half to assemble.
6:20 PM Just started the coals.
The sides are attached to the back by piano hinges using pop-rivets. The front is held in place by two tabs that latch onto screw posts. Once assembled its dimensions are 25 x 33 by 30 cm . I painted the sides with Rust-Oleum High Temperature black paint.
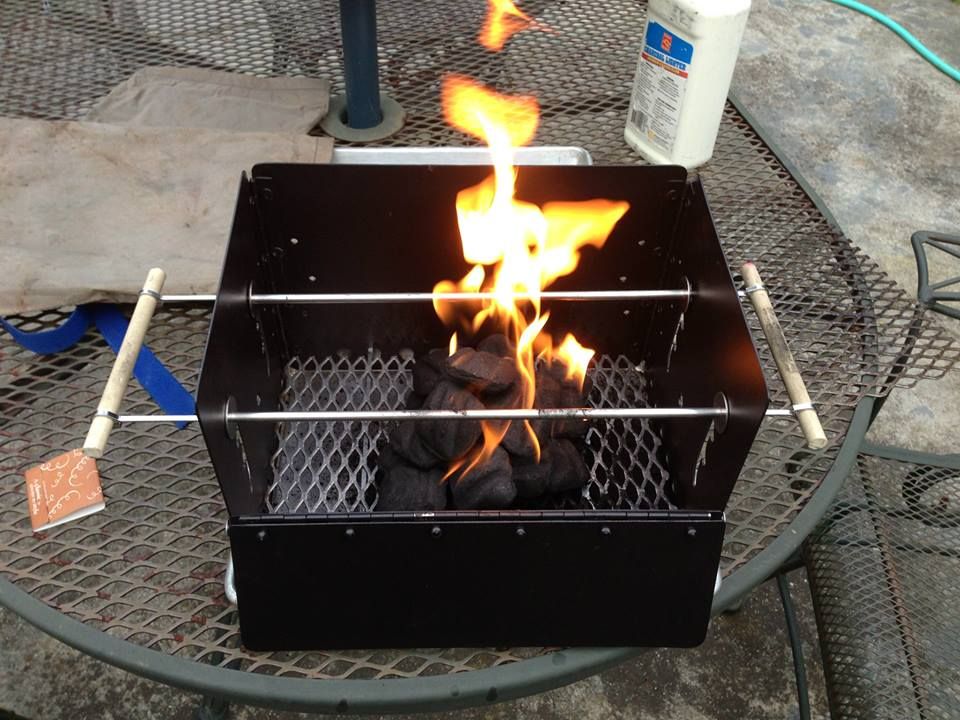
6:45 The coals are ready.
There are air holes along the bottom on all four sides. The coals rest are on 13 gauge expanded metal.
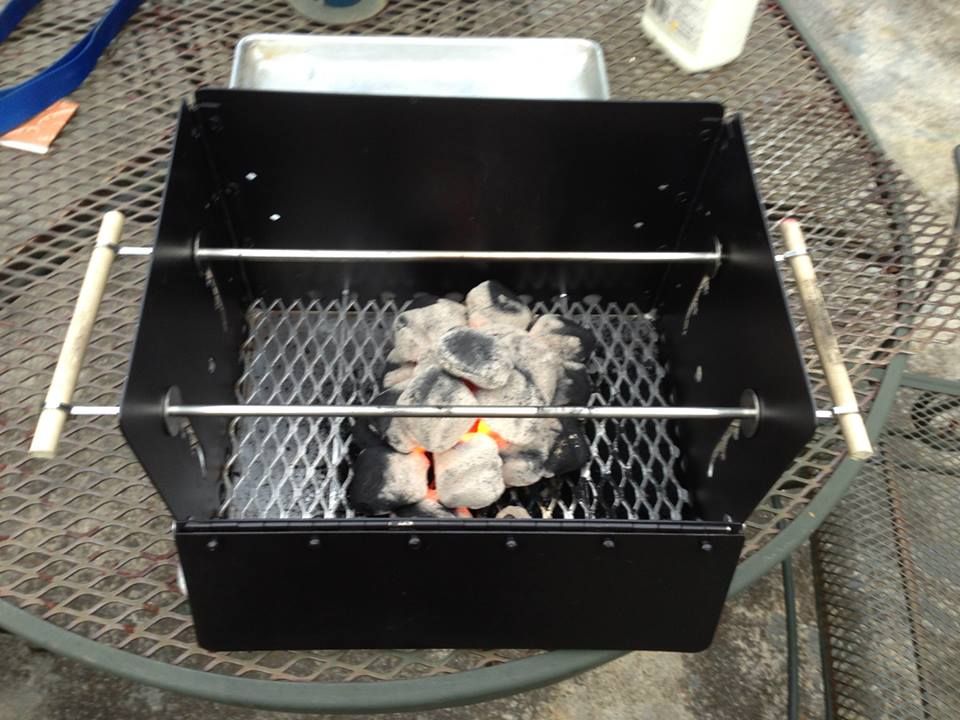
The cooking surface is also 13 gauge expanded metal. It rests on two stainless steel tubes that have press fitted washers to keep them snug in the slide channels for raising and lowering the grill. The handles are ½” wood dowel fitted into skewers that slide into the stainless steel tubes.
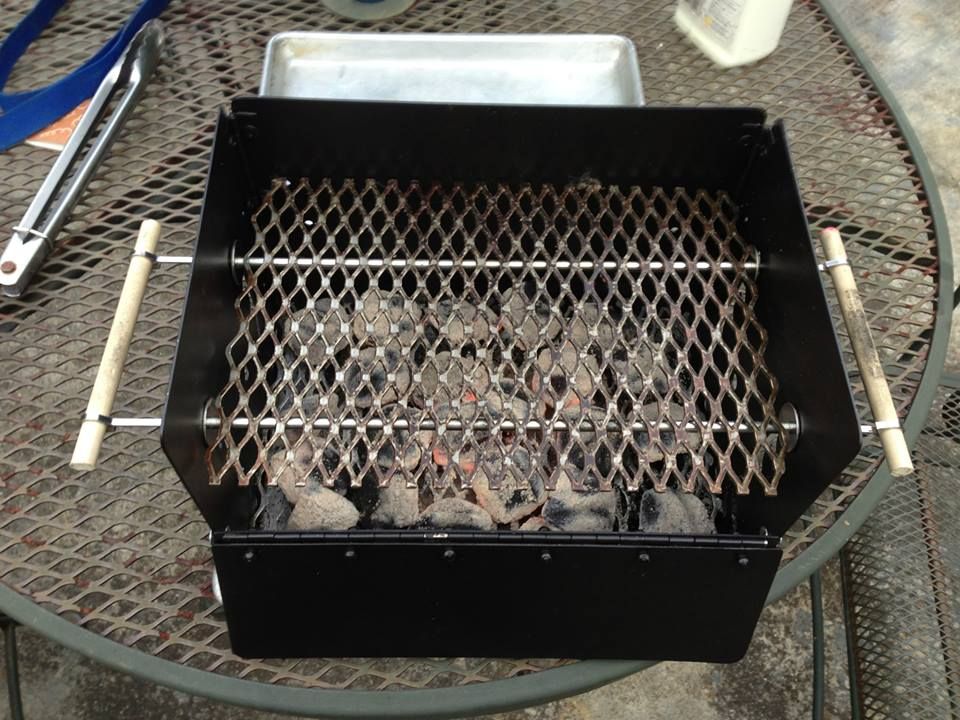
Here, the grill is on the lowest setting, just above the coals. Great for squeezing that last bit of heat from the dying coals.
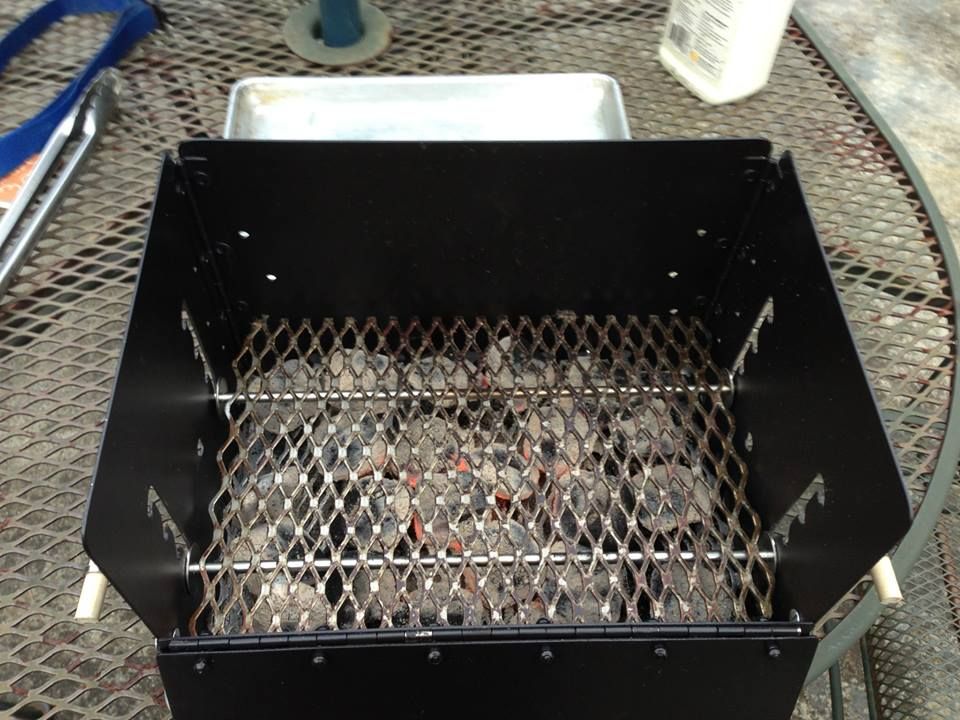
The Front is hinged to completely enclose the grill.
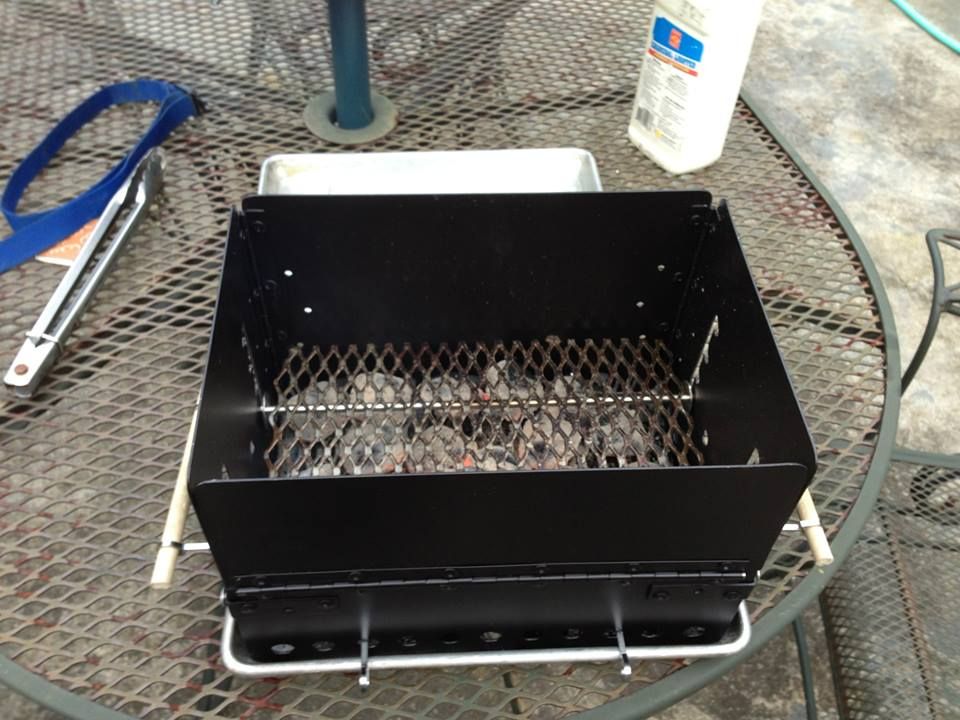
Here's a close up of the handle and slot for changing grill height. You can also see the air holes at the bottom and the latch the secures the front to the screw post.
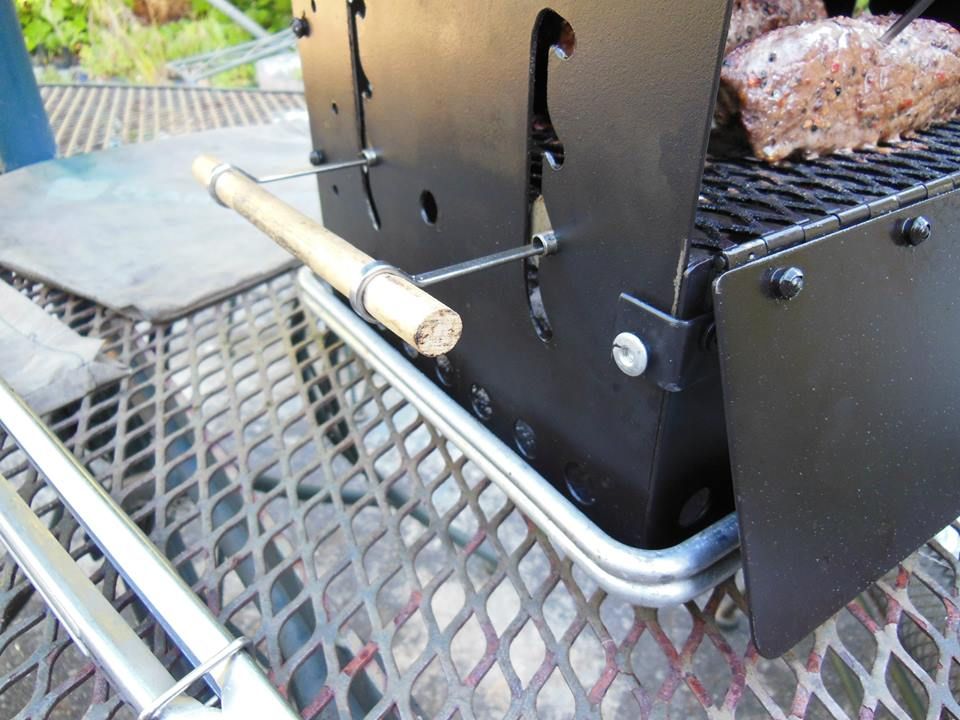
Here is a close up of the inside. You can see the press-fitted washer that secures the stainless steel grill rod and the piano hinge that allows the front to fold down.
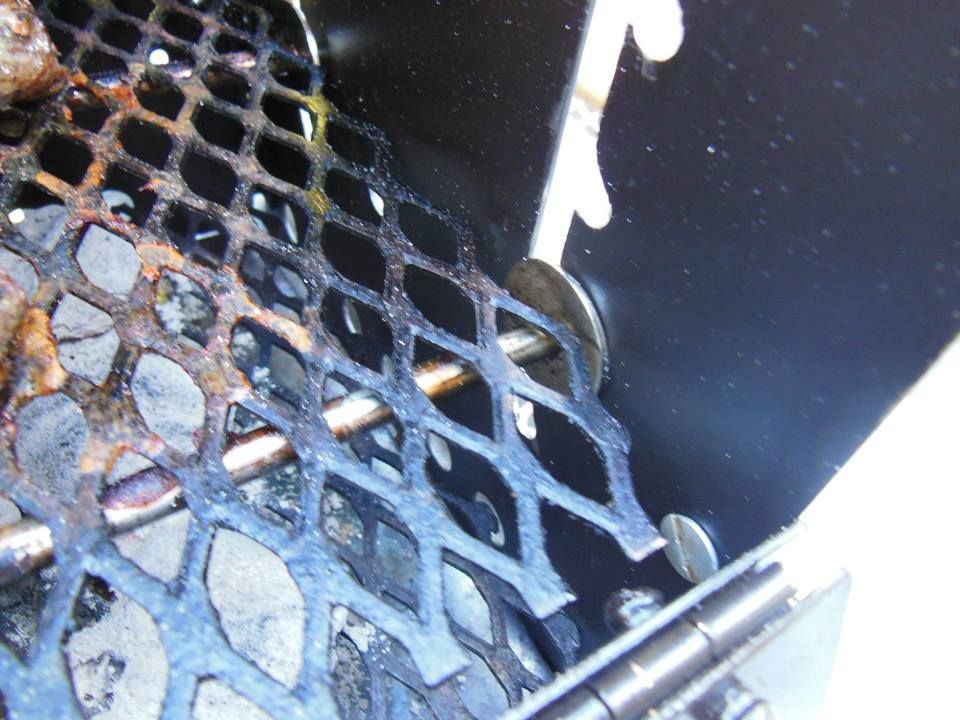
Time to grill up some tri-tip!
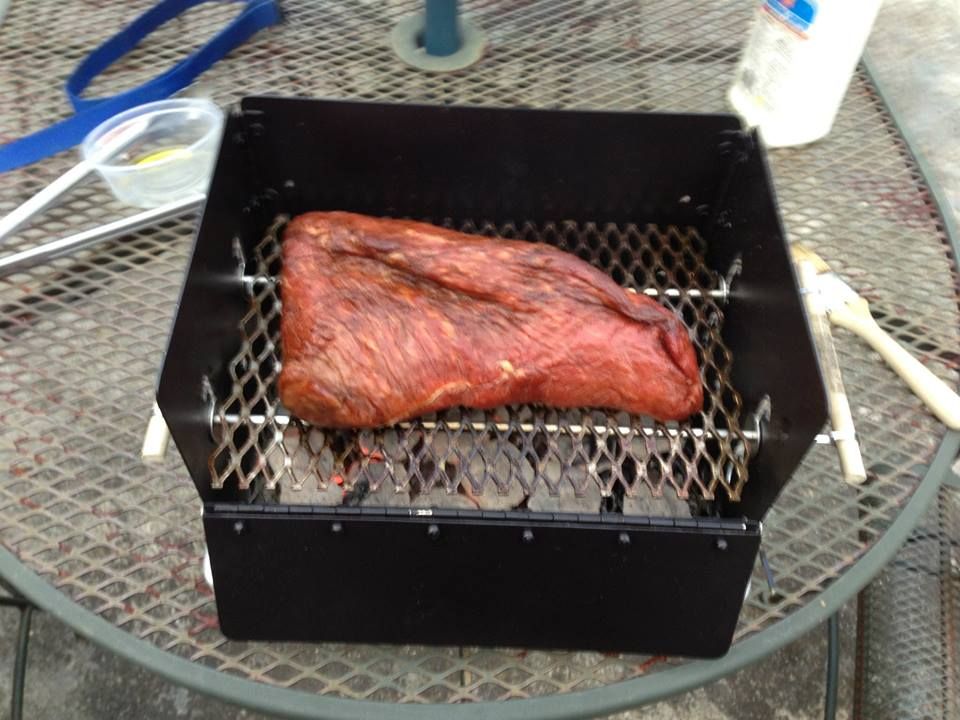
The grill can be completely enclosed by adding the top cookie sheet. The temperature inside is hotter than 220 degrees F - that's as high as my thermometer goes. Here you can also see a pair of skewers that support the expanded metal that the coals rest on.
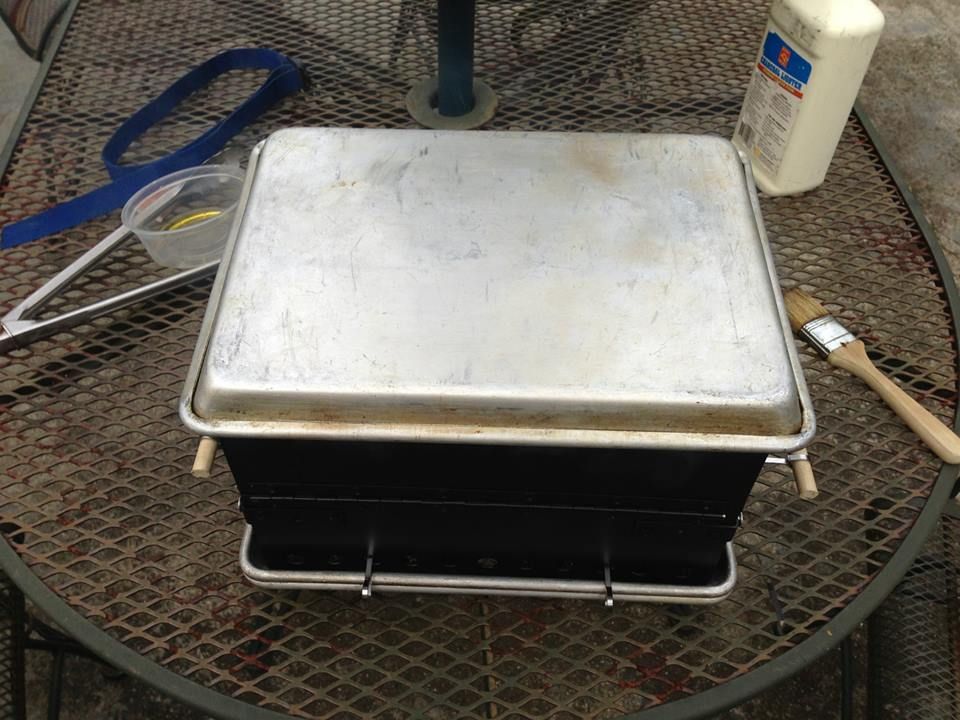
The top cookie sheet can also be set at an angle so the door can be opened.
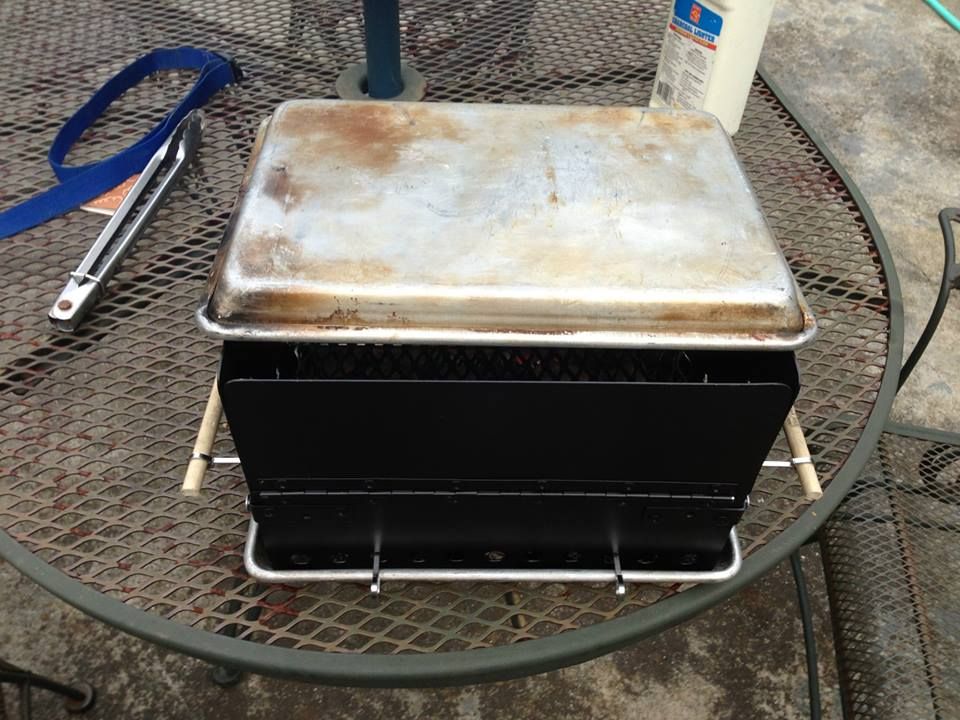
7:00 PM First side is done.
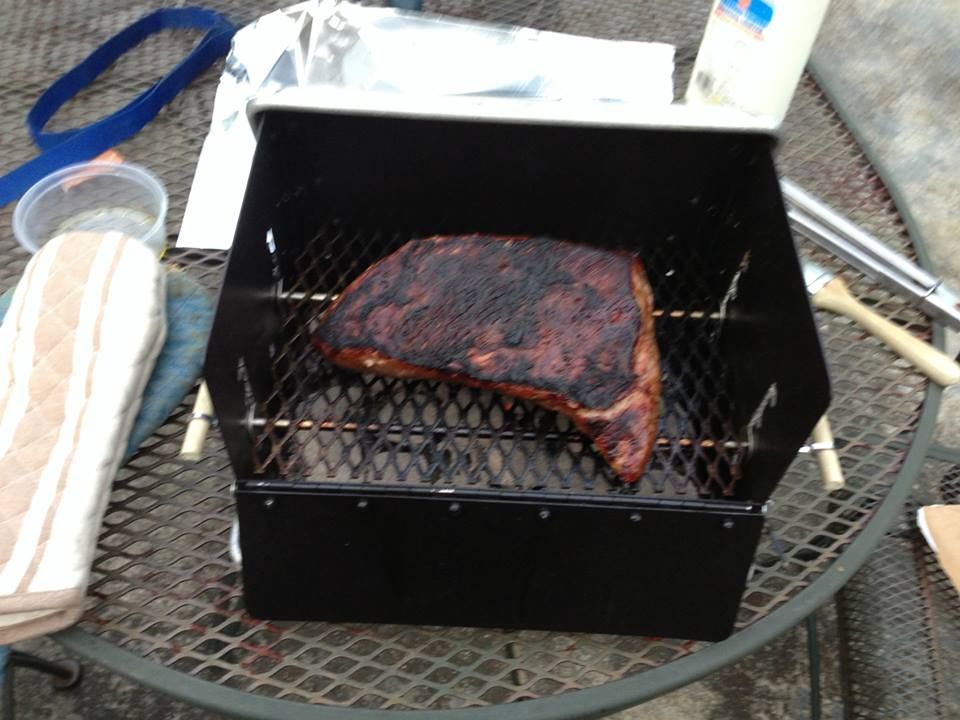
The expanded metal is difficult to clean but it has the advantage of letting you grill veggies that tend to fall between traditional grill bars.
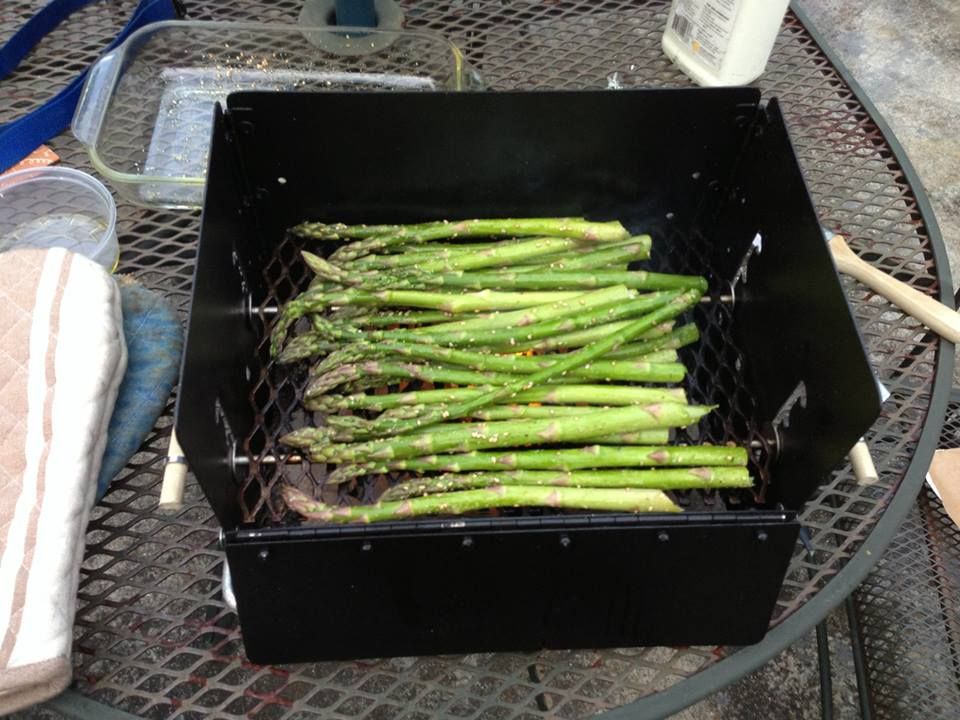
Here you can see the bottom cookie sheet.
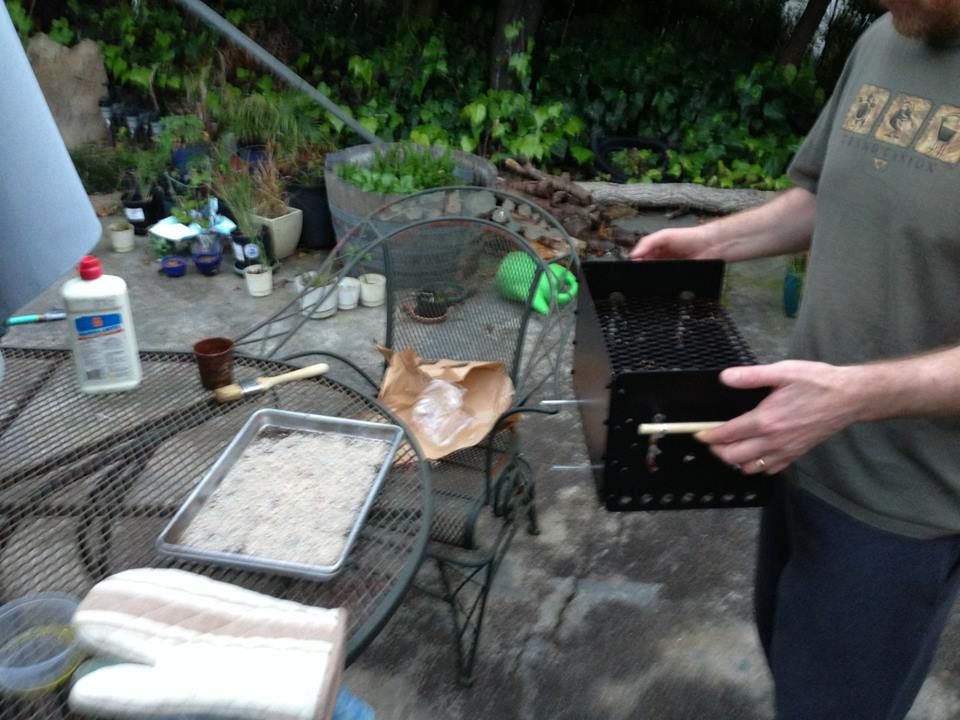
I use two cookie sheets on the bottom to provide enough insulation to keep the bottom from getting too hot. It would have been easy enough to fabricate a stand but I use the cookie sheets for other purposes.

Here is tonight's eggplant. Even though the grill surface is only 8 x 12, it can grill 5 large hamburgers. I just had to stack them and rotate which one was on bottom until they had shrunk so that I could grill them side by side. I did the same thing with the eggplant.

Bon Appétit!
Last edited: