amgvr4
Adventurer
I got the t-case yoke and spring bushings in yesterday. I'm a little worried that the yoke might be the wrong one as it has the normal type splines and not the funky square ones everyone has said are specific to the 4407. The add was clearly labeled for bw 4407 so I will know more when I try to install it tomorrow. I will not be able to get to the shackle flip so I will mostly try to concentrate on the drive shaft and get that sorted. I also got my lathe up and running again so I could properly separate the slip splines from the tubing on both of the shafts.
I used a parting tool to cut the tube at the weld that way I ended up with nice and clean/perfectly square ends
Here is what the end of the f250 slip spline looks like. There isn't enough meat there to turn it down to 2.320" and slide the f350 tube on so I picked up up some .250 wall DOM to sleeve over the tube and spline end.
Here are the two ends removed from their respective tubes. 250 on the left 350 on the right
The DOM I picked up at the steel yard has a precision honed inner surface that makes me think is was hydraulic cylinder tubing. It is 2.493" and the OD for the f350 shaft is 2.50" so I should be able to just slide it over the tubing for a nice interference fit with a little heating. I have plenty of metal on the slip end to turn it down to 2.50". This should make it very easy to ensure a straight connection between the two parts. I will plan on having it balanced after I test it out and make sure everything works as intended. I also installed the .250" wheel spacers I got and even though they do not eliminate the tire rub they allow more steering angle and it makes a big difference maneuvering in parking lots. I will still need to come up with a way to fix it completely but anything helps at this point and for $15 it was money well spent.
Hopefully I will get lucky tomorrow and the t-case flange will be the correct one and I can get the drive shaft dialed in and ready to rebuild and balance. If not I will have to figure out where to get a proper yoke from. I will wait to start the rear until I have at least a full day free to hammer it out
I used a parting tool to cut the tube at the weld that way I ended up with nice and clean/perfectly square ends
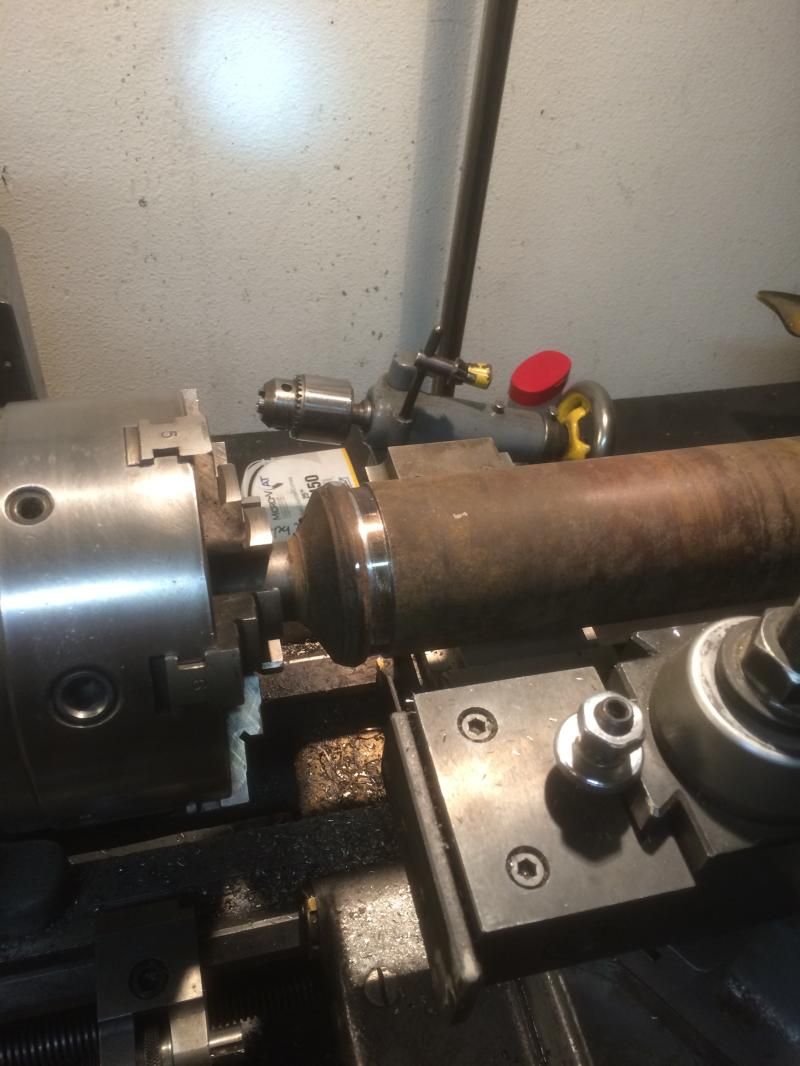
Here is what the end of the f250 slip spline looks like. There isn't enough meat there to turn it down to 2.320" and slide the f350 tube on so I picked up up some .250 wall DOM to sleeve over the tube and spline end.
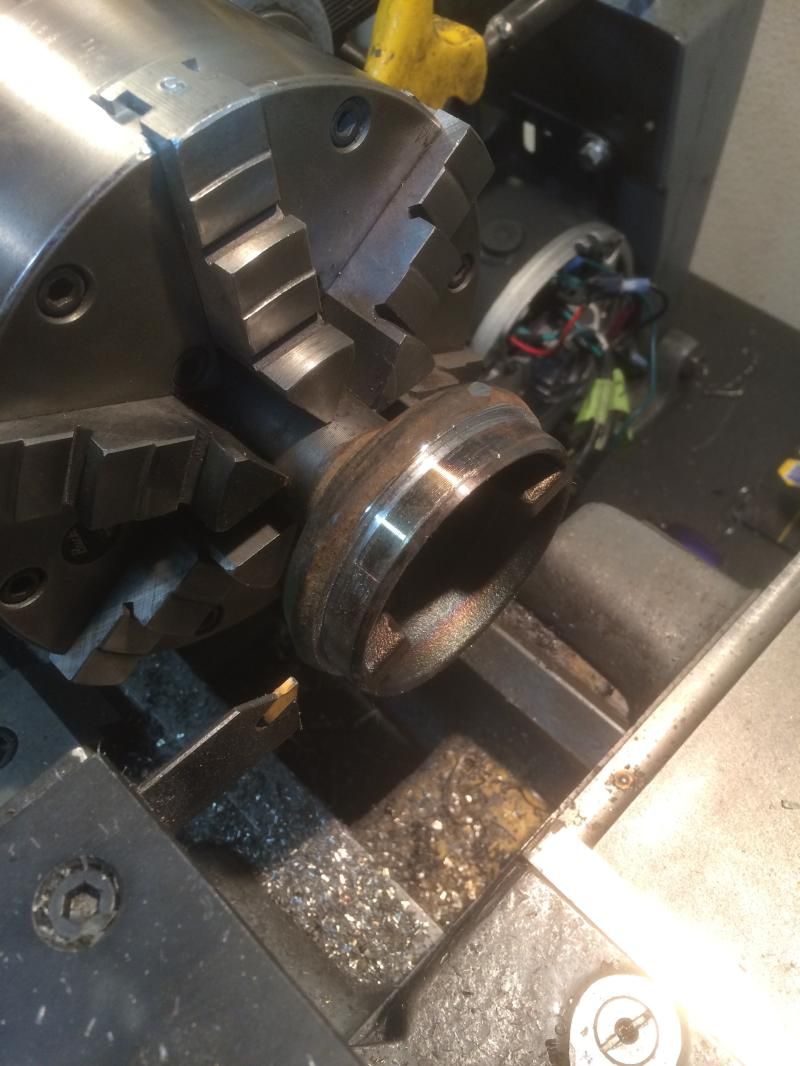
Here are the two ends removed from their respective tubes. 250 on the left 350 on the right
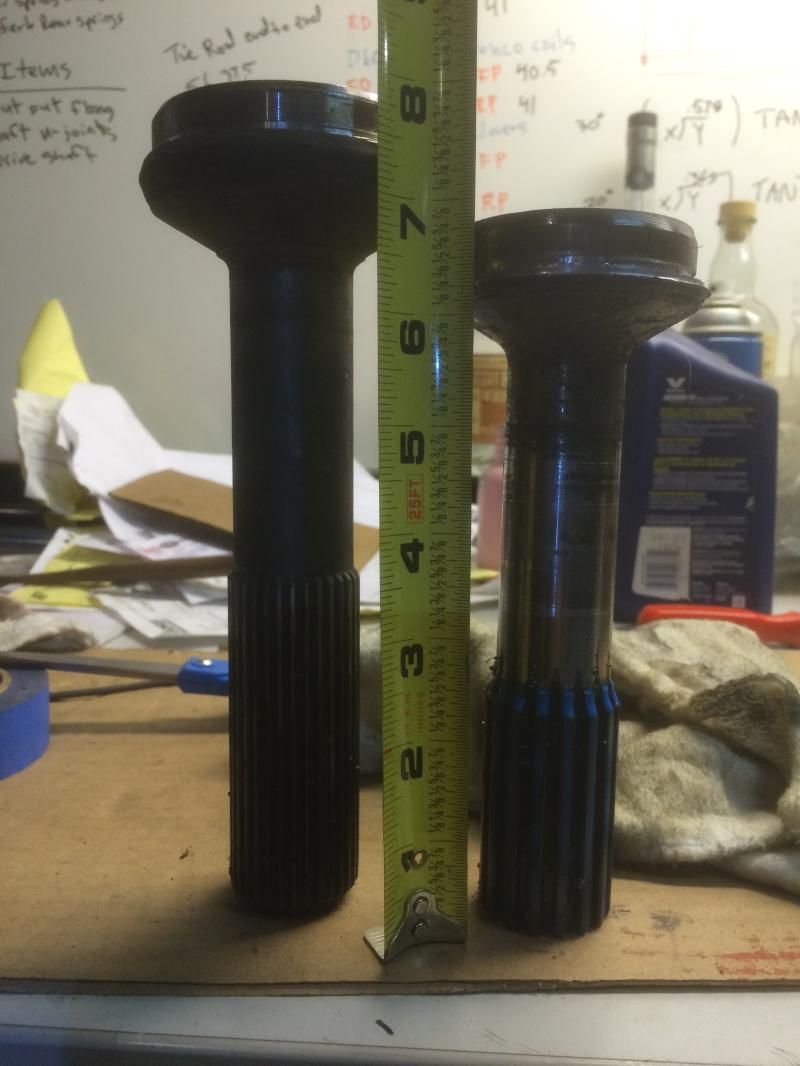
The DOM I picked up at the steel yard has a precision honed inner surface that makes me think is was hydraulic cylinder tubing. It is 2.493" and the OD for the f350 shaft is 2.50" so I should be able to just slide it over the tubing for a nice interference fit with a little heating. I have plenty of metal on the slip end to turn it down to 2.50". This should make it very easy to ensure a straight connection between the two parts. I will plan on having it balanced after I test it out and make sure everything works as intended. I also installed the .250" wheel spacers I got and even though they do not eliminate the tire rub they allow more steering angle and it makes a big difference maneuvering in parking lots. I will still need to come up with a way to fix it completely but anything helps at this point and for $15 it was money well spent.
Hopefully I will get lucky tomorrow and the t-case flange will be the correct one and I can get the drive shaft dialed in and ready to rebuild and balance. If not I will have to figure out where to get a proper yoke from. I will wait to start the rear until I have at least a full day free to hammer it out