Metcalf
Expedition Leader
A little more last night.....
This is the start of the skidplate/bucket to cover up the sheetmetal pan on the transfer case. It ended up being kinda like a modern art project towards the end. I wanted it to mate to existing surfaces instead of having to make new brackets for all the mounting points. That takes a bit more time and a bit more parts.......and clamps....and magnets....
I ran out of material last night but found some more this morning in the short cut rack at work. It shouldn't take me too long to finish up the fab. The welding and cleanup on the other hand will take a little longer!
More progress tonight.
To the people watching that aren't saying anything.....that is pretty boring...
Anyways.....
The design and fab work is pretty much done on the transfer case skidplate. I need to drill the mounting holes in the mounting tabs, final weld, finish sand, prime, and paint. Most of that stuff is pretty mindless.....
For mounting points I am going to have six 3/8-16 screws, probably some buttom head allen style units. There will be 2 in the outer frame mounting tab. I think those will have to be riv-nuts since I don't really want to drill a huge hole and weld in the bottom of the main frame rail upside down. The other 4 mounting points will be in the transfer case crossmember. I will mark those and pull it for the work. I also have to tap the two holes for the rear mounting tab on the engine oil mounting skidplate.
All in all I am pretty happy how things turned out. I wanted some more protection on the sheet metal pans without going overkill. I haven't really hit the belly much in the last two years of 'wheeling so I didn't want to weigh the chassis down with a ton of extra steel. The total skidplate package is maybe 25lbs. For protection from the engine oil pan to the transfer case pan I don't think that is too bad at all.
Hopefully this weekend I can do all the finish work and move onto the rocker guards.....
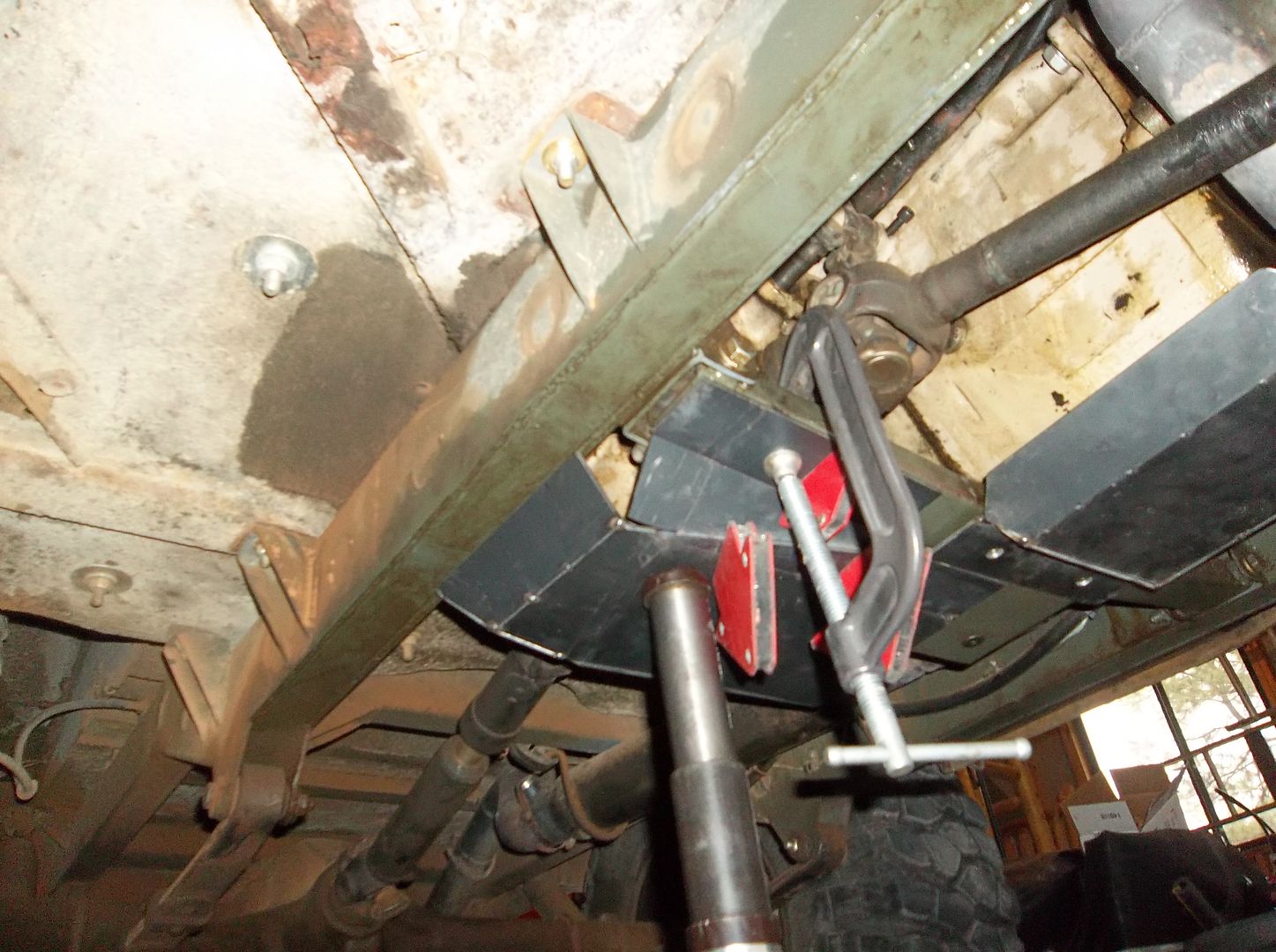
This is the start of the skidplate/bucket to cover up the sheetmetal pan on the transfer case. It ended up being kinda like a modern art project towards the end. I wanted it to mate to existing surfaces instead of having to make new brackets for all the mounting points. That takes a bit more time and a bit more parts.......and clamps....and magnets....
I ran out of material last night but found some more this morning in the short cut rack at work. It shouldn't take me too long to finish up the fab. The welding and cleanup on the other hand will take a little longer!
More progress tonight.
To the people watching that aren't saying anything.....that is pretty boring...
Anyways.....
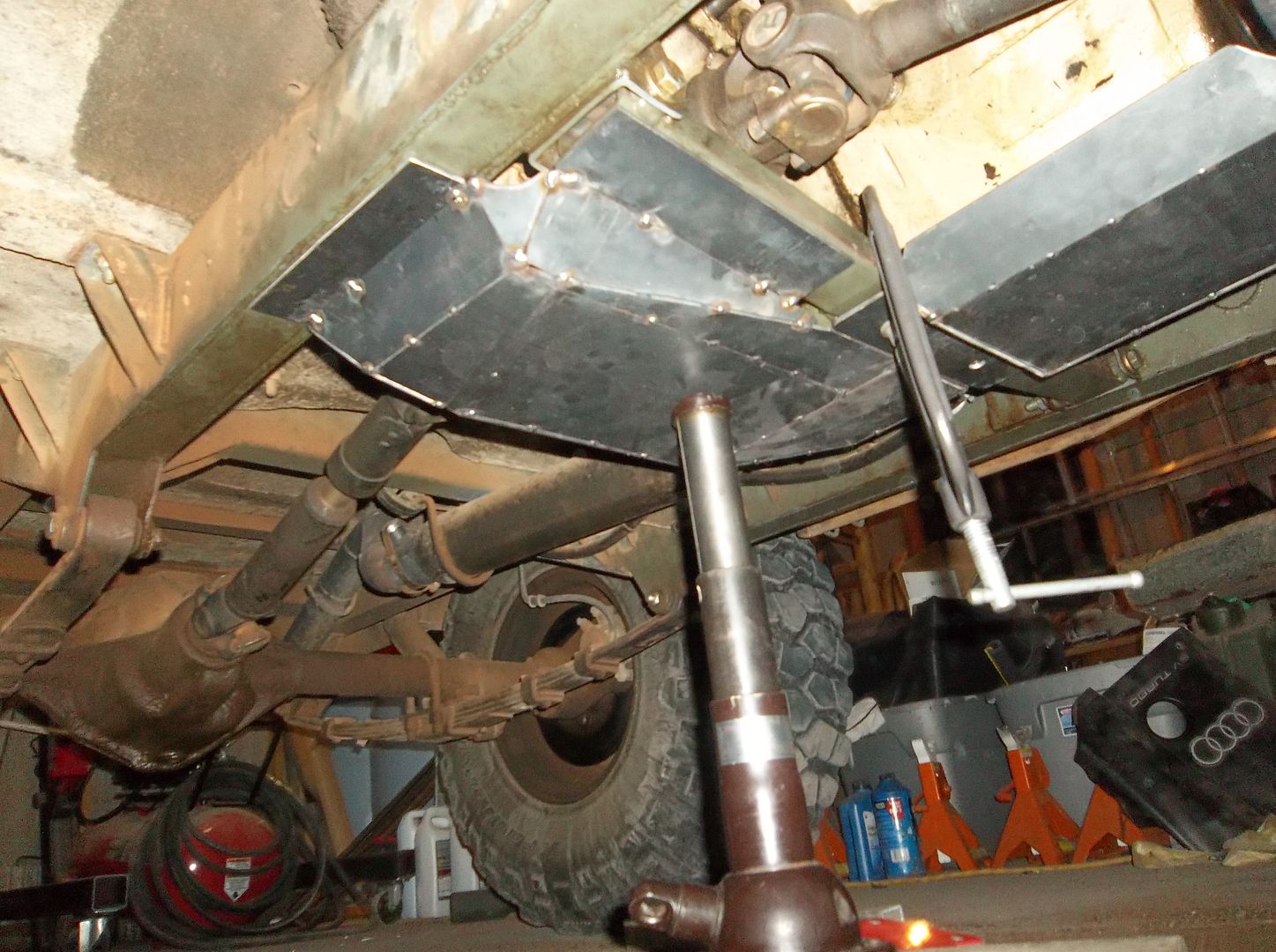
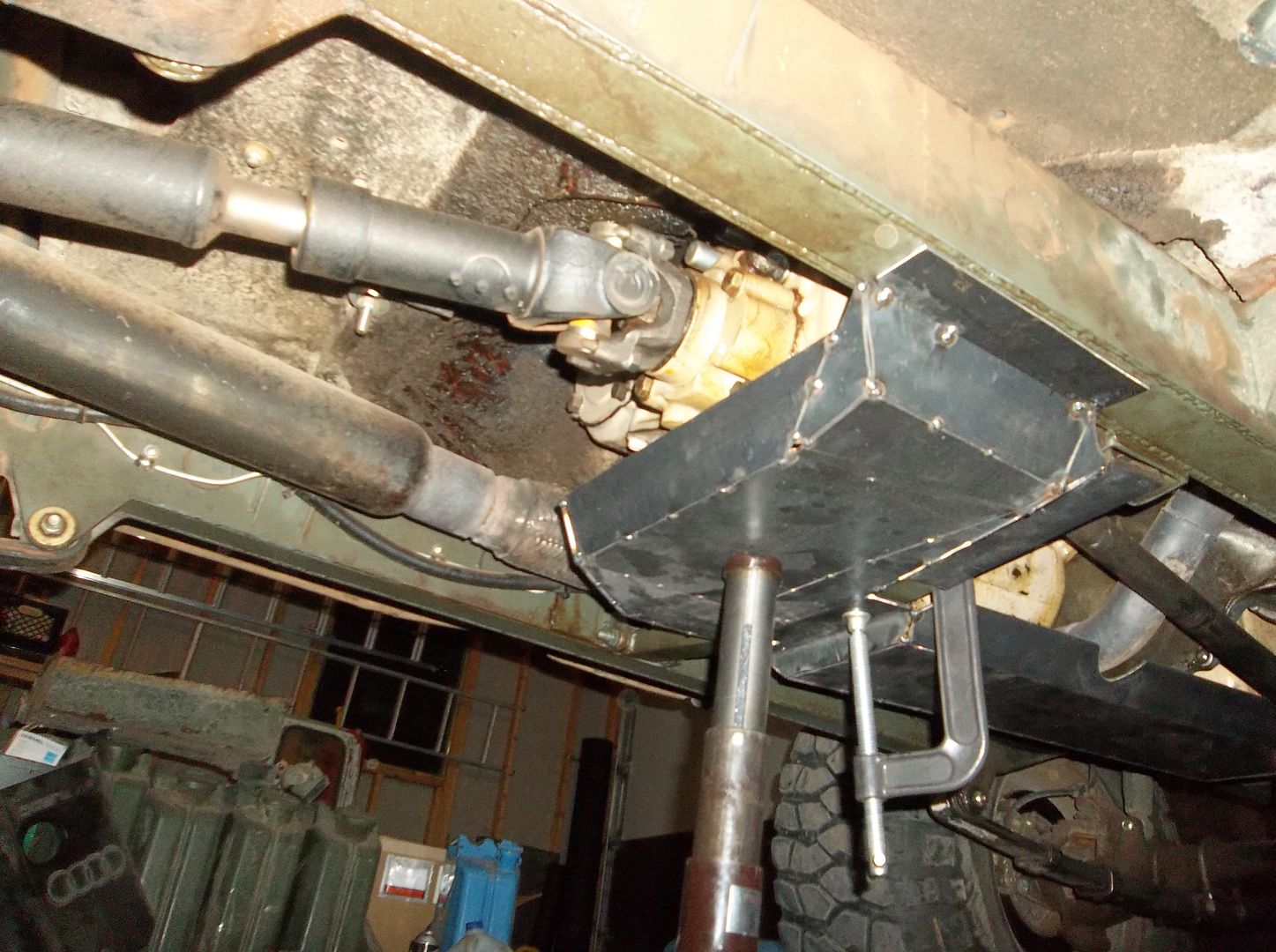
The design and fab work is pretty much done on the transfer case skidplate. I need to drill the mounting holes in the mounting tabs, final weld, finish sand, prime, and paint. Most of that stuff is pretty mindless.....
For mounting points I am going to have six 3/8-16 screws, probably some buttom head allen style units. There will be 2 in the outer frame mounting tab. I think those will have to be riv-nuts since I don't really want to drill a huge hole and weld in the bottom of the main frame rail upside down. The other 4 mounting points will be in the transfer case crossmember. I will mark those and pull it for the work. I also have to tap the two holes for the rear mounting tab on the engine oil mounting skidplate.
All in all I am pretty happy how things turned out. I wanted some more protection on the sheet metal pans without going overkill. I haven't really hit the belly much in the last two years of 'wheeling so I didn't want to weigh the chassis down with a ton of extra steel. The total skidplate package is maybe 25lbs. For protection from the engine oil pan to the transfer case pan I don't think that is too bad at all.
Hopefully this weekend I can do all the finish work and move onto the rocker guards.....