Metcalf
Expedition Leader
Just duplicating the A-pillar rocker outrigger on the drivers side...
This is how I pressed the part that needed to form around the multiple steps on the rear of the mount. There are 3 levels in this. I was able to assemble a simple one off press brake die using scraps I had laying around. By stacking up different levels of material, then stacking a thick plate over everything, and squishing it in the 20 ton press, I was able to make the part I needed without investing a lot of time in a one off tool.
I have no idea how I come up with this stuff sometimes. I am REALLY surprised that worked as well as it did both times.
The body side of the mount is all fabricated. I need to tack everything on the vehicle and then spend a few hours TIG welding it up. Fun Fun.
The outrigger parts should be much the same as the passenger side. I already have templates for those so it will just be checking/changing the mounting hole locations which is bound to be slightly different.
I guess I will probably be waiting on my dimple die set....darn. I can still start to make the top and bottoms however. I think I would dimple die them just before welding.
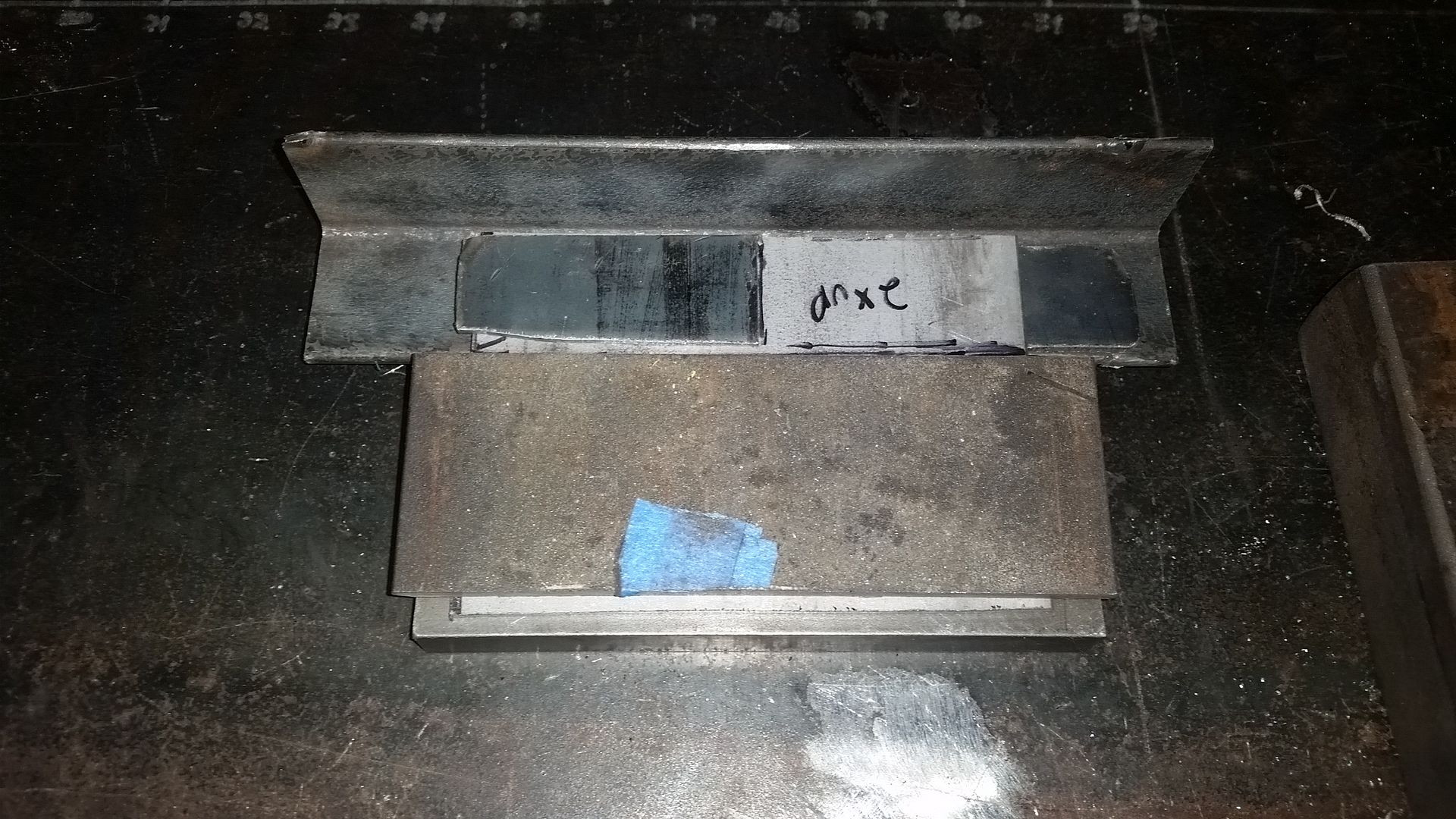
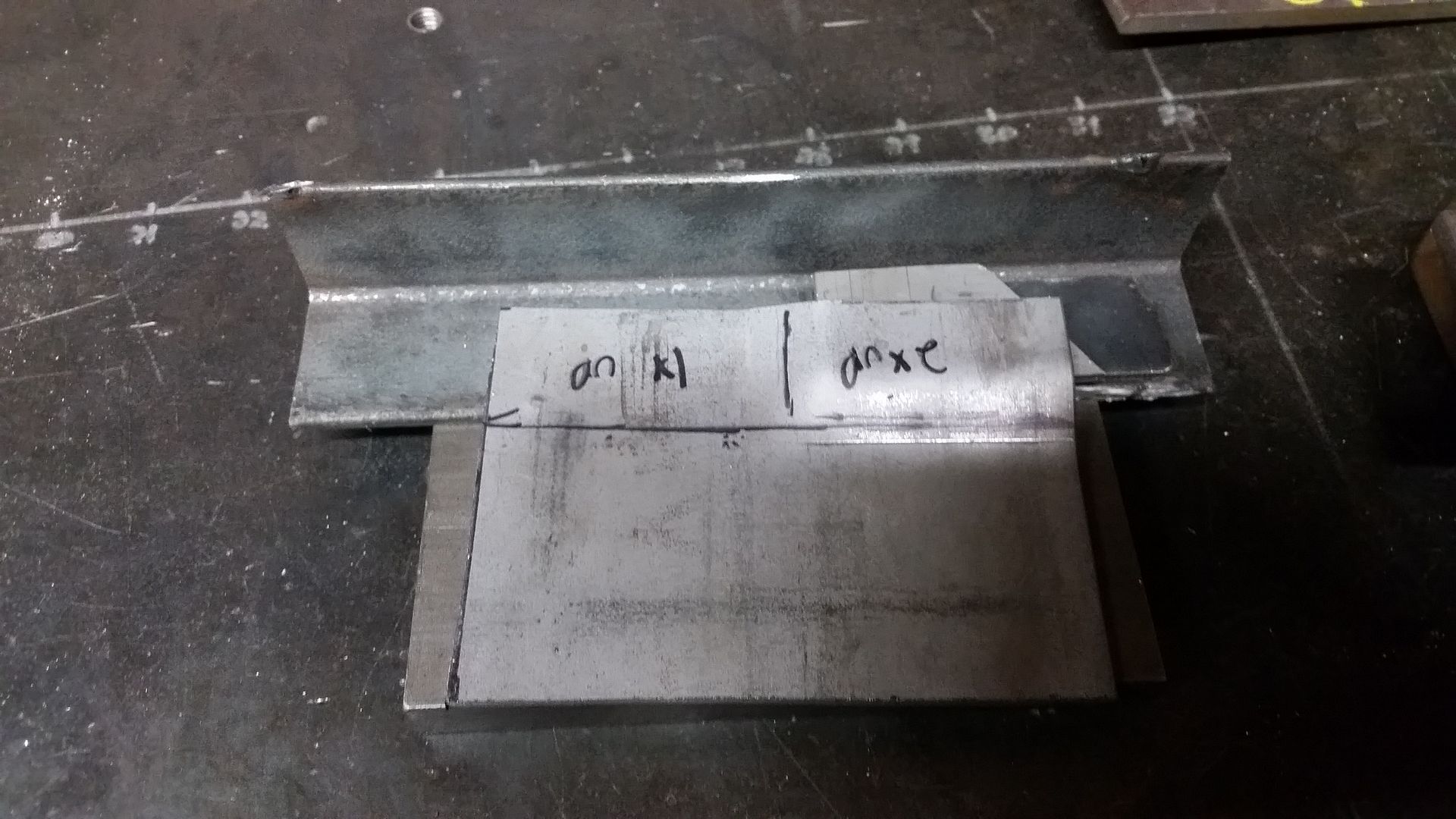
This is how I pressed the part that needed to form around the multiple steps on the rear of the mount. There are 3 levels in this. I was able to assemble a simple one off press brake die using scraps I had laying around. By stacking up different levels of material, then stacking a thick plate over everything, and squishing it in the 20 ton press, I was able to make the part I needed without investing a lot of time in a one off tool.
I have no idea how I come up with this stuff sometimes. I am REALLY surprised that worked as well as it did both times.
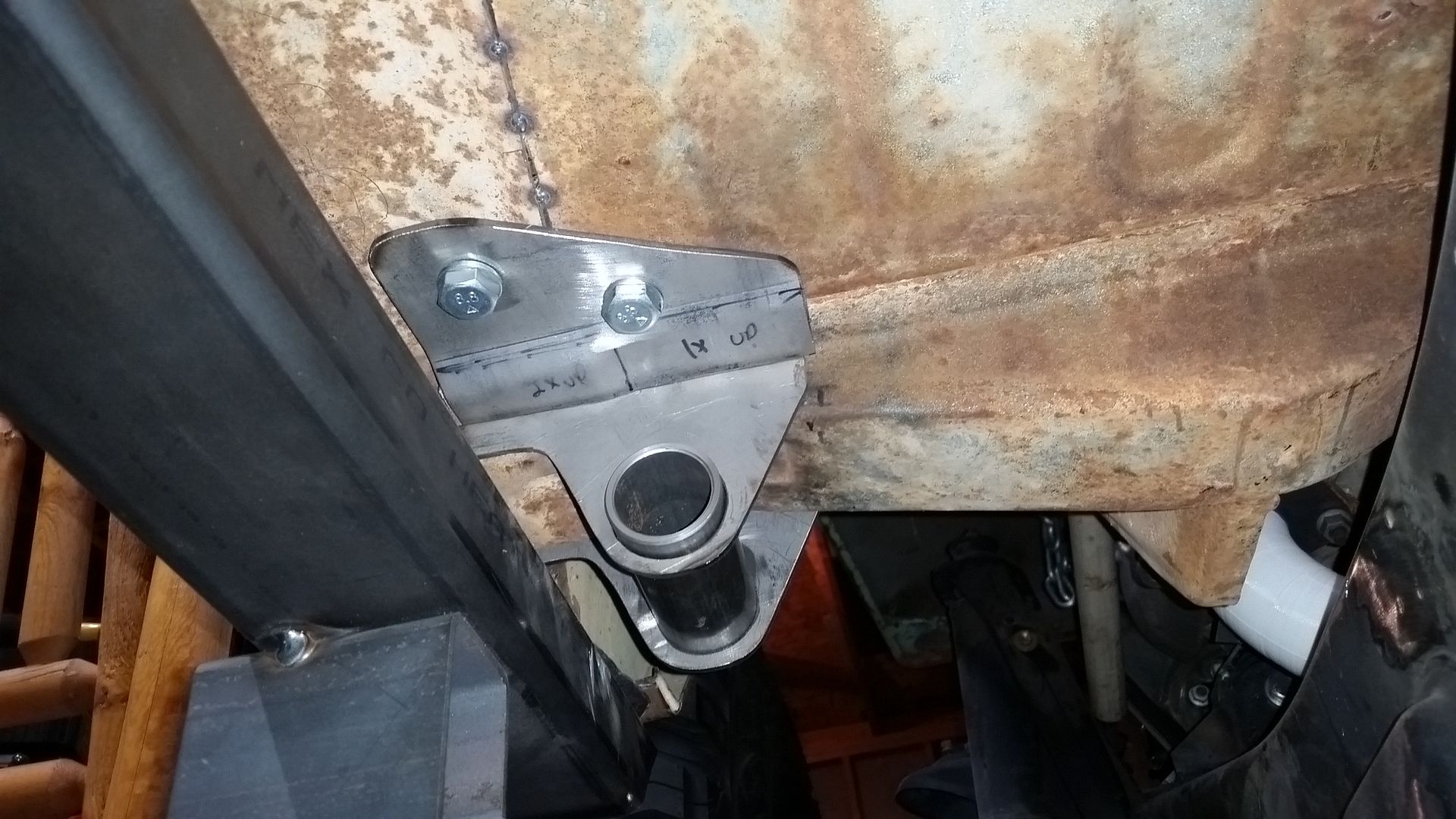
The body side of the mount is all fabricated. I need to tack everything on the vehicle and then spend a few hours TIG welding it up. Fun Fun.
The outrigger parts should be much the same as the passenger side. I already have templates for those so it will just be checking/changing the mounting hole locations which is bound to be slightly different.
I guess I will probably be waiting on my dimple die set....darn. I can still start to make the top and bottoms however. I think I would dimple die them just before welding.