Metcalf
Expedition Leader
And now I need to clean stuff.....
Everything in the bottom end looked really good. I will be reassembling the shortblock with new seals, bearings, and rings. Everything is standard as far as I can tell. I will probably ball/flex-hone it and clean it really well.
I plastigaged some of the mains and rods. Everything was about .001-.0015
Nothing looked out of place or different between any of the bearings. The crank measured standard/standard
Anyone use one of these style ring compressors?
http://www.summitracing.com/parts/sme-90a3700/overview/
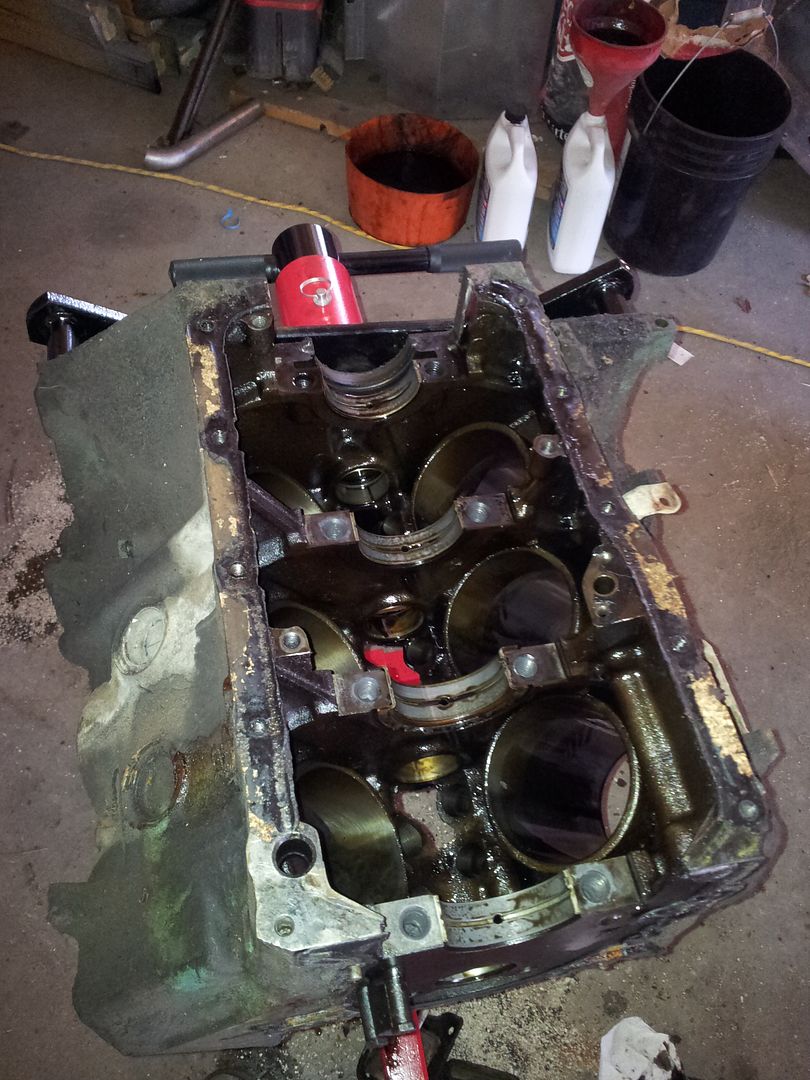
Everything in the bottom end looked really good. I will be reassembling the shortblock with new seals, bearings, and rings. Everything is standard as far as I can tell. I will probably ball/flex-hone it and clean it really well.
I plastigaged some of the mains and rods. Everything was about .001-.0015
Nothing looked out of place or different between any of the bearings. The crank measured standard/standard
Anyone use one of these style ring compressors?
http://www.summitracing.com/parts/sme-90a3700/overview/