GeoTracker90
Adventurer
5-31-08 Part 2
Part 2
I started to slack for a little bit with the picture taking and got ahead of myself. The rear bumper, main frame rails, cross members, front main cross member and the pre-assembled main box side panel all got tacked into place before I could stop myself.
Second pre-assembled side panel tacked into place.
In order to have everything line up and keep it flush a little care needs to be taken. In my case it is as simple as a flat scrap of metal and a couple clamps.
The front and rear upper main box cross bars are in place and keeping the two side panels tied together.
And for a little extra support for the front I added a verticle center support. Trust me, this thing is going to be beefy.
End of part 2
Mike
Part 2
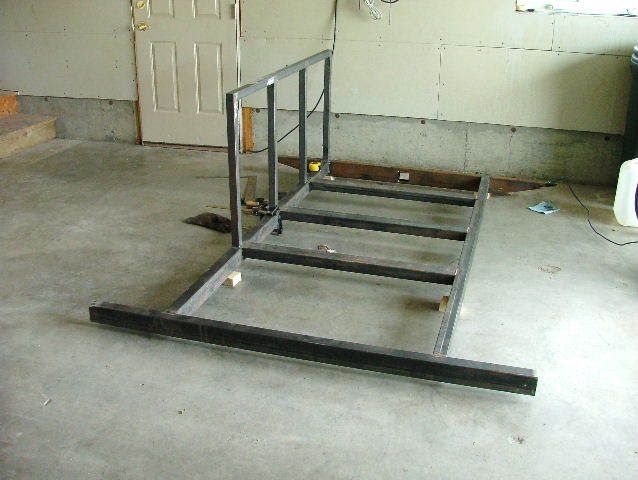
I started to slack for a little bit with the picture taking and got ahead of myself. The rear bumper, main frame rails, cross members, front main cross member and the pre-assembled main box side panel all got tacked into place before I could stop myself.
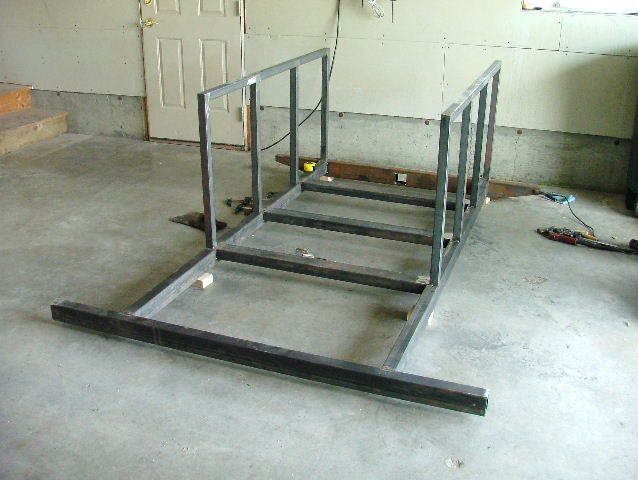
Second pre-assembled side panel tacked into place.
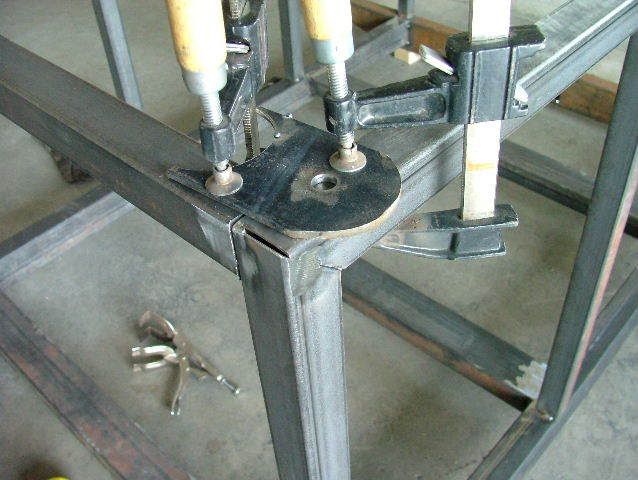
In order to have everything line up and keep it flush a little care needs to be taken. In my case it is as simple as a flat scrap of metal and a couple clamps.
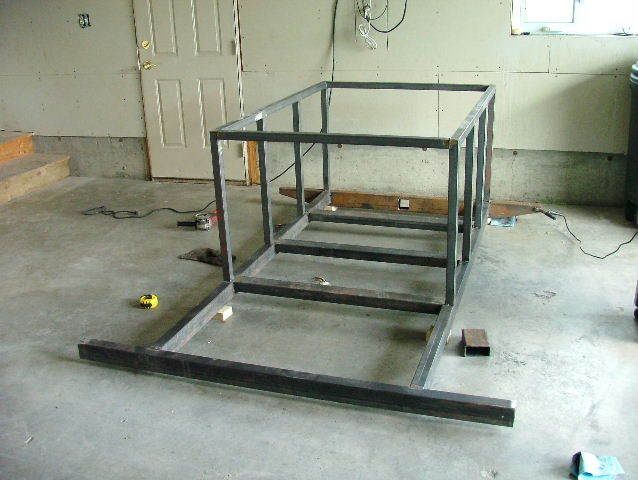
The front and rear upper main box cross bars are in place and keeping the two side panels tied together.
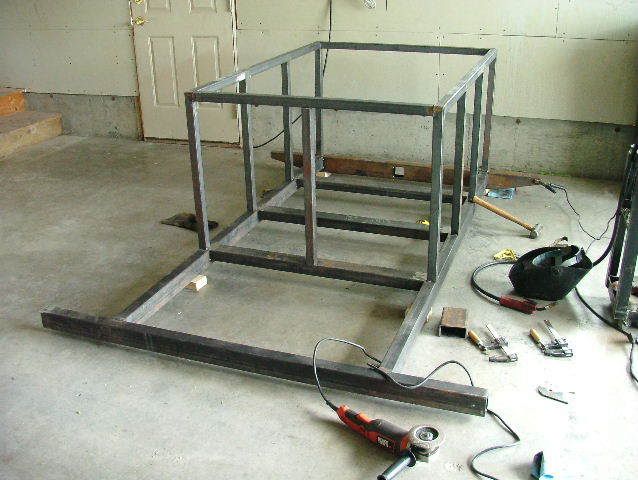
And for a little extra support for the front I added a verticle center support. Trust me, this thing is going to be beefy.
End of part 2
Mike
Last edited: