Metcalf
Expedition Leader
I got a few interesting packages in the mail today....
I have been playing around with having some parts 3D printed. I also purchased a 2.25 to 3" merge pipe in purge TIG welded stainless.
This is how the 3D printed parts work in combination with a little cheap/free 2" heavy wall packing tubes.....
This took me all of about 15 minutes to mock up....
This is NOT my idea. I just reversed engineered it for my use. The original idea came from ICE engine works.
http://www.icengineworks.com/
They pioneered this type of system for the construction of custom headers.
I twisted the idea around a little bit for my use. I wanted to use the same technology to plan out the forward Y-pipe part of my exhaust. They do not offer a 'block' in 2.25" diameter with a 3.5" CLR bend. I was able to reverse engineer the idea for my uses and have then 3D printed for me.
My improvement for my use of the idea, in exhaust work, was to be able to use some cardboard shipping tube for the longer straight sections. I designed a 1" long block that can either be used to fit between bends or can either be inserted into cardboard packing tubes with a 2" diameter. The heavy wall 2" ID shipping tubes just happen to be 2.3" OD which is close enough to simulate the 2.25" OD tubing I am using. The thicker tubes are easy enough to cut with a fine tooth wood saw.
A few more views.
I can't wait to use the 'data' provided by the mockup to order the amount of 'bend' I need. I will be able to map out each side easy enough. I will not have to waste expensive stainless steel tubing doing a trial and error fitment. Once you have a complete model of one side, you can look at how you might be able to eliminate weld joints by using the tangent 'legs' on common bend angles. Very neat technology....
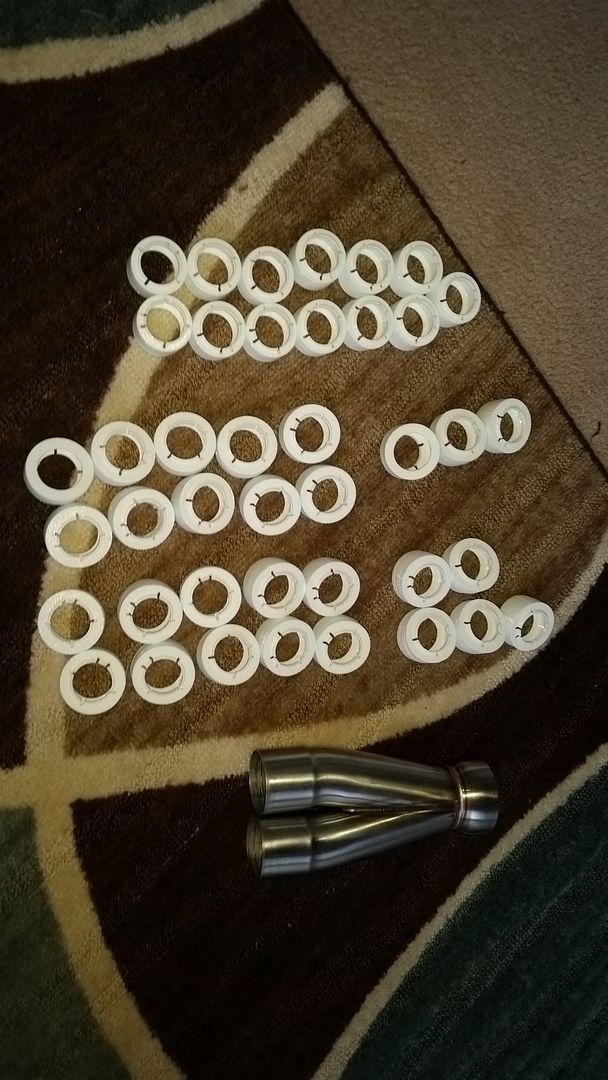
I have been playing around with having some parts 3D printed. I also purchased a 2.25 to 3" merge pipe in purge TIG welded stainless.
This is how the 3D printed parts work in combination with a little cheap/free 2" heavy wall packing tubes.....
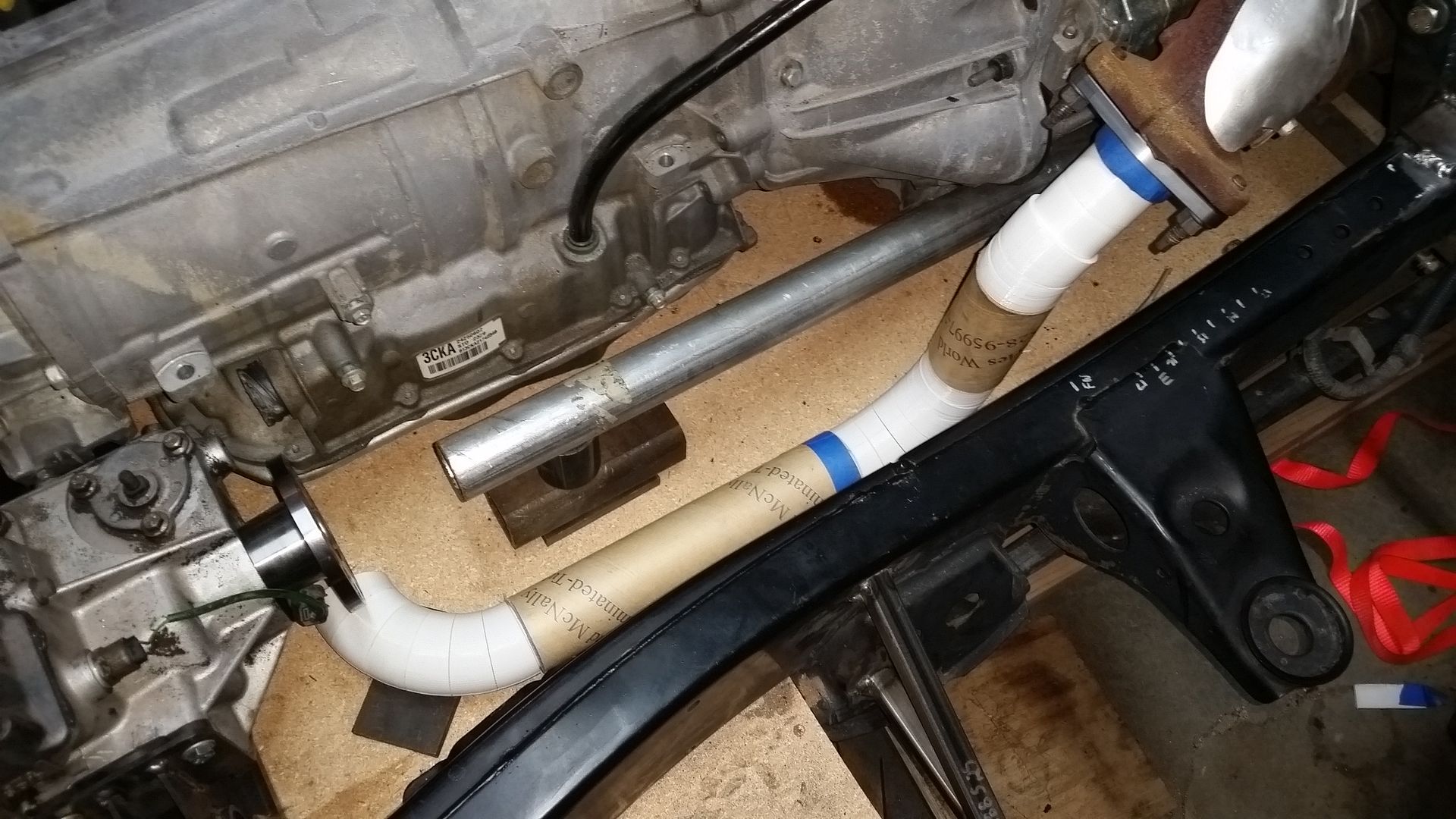
This took me all of about 15 minutes to mock up....
This is NOT my idea. I just reversed engineered it for my use. The original idea came from ICE engine works.
http://www.icengineworks.com/
They pioneered this type of system for the construction of custom headers.
I twisted the idea around a little bit for my use. I wanted to use the same technology to plan out the forward Y-pipe part of my exhaust. They do not offer a 'block' in 2.25" diameter with a 3.5" CLR bend. I was able to reverse engineer the idea for my uses and have then 3D printed for me.
My improvement for my use of the idea, in exhaust work, was to be able to use some cardboard shipping tube for the longer straight sections. I designed a 1" long block that can either be used to fit between bends or can either be inserted into cardboard packing tubes with a 2" diameter. The heavy wall 2" ID shipping tubes just happen to be 2.3" OD which is close enough to simulate the 2.25" OD tubing I am using. The thicker tubes are easy enough to cut with a fine tooth wood saw.
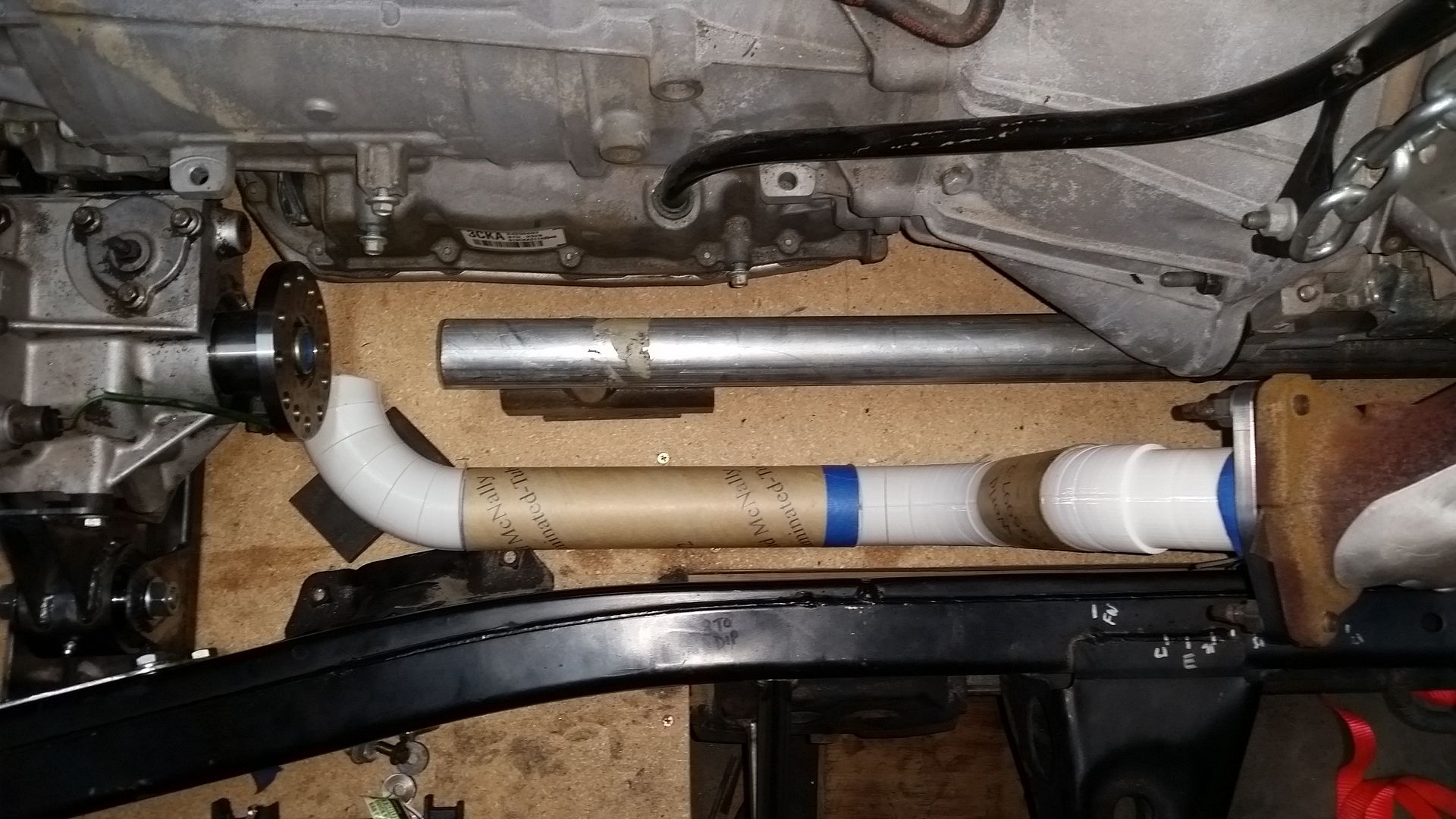
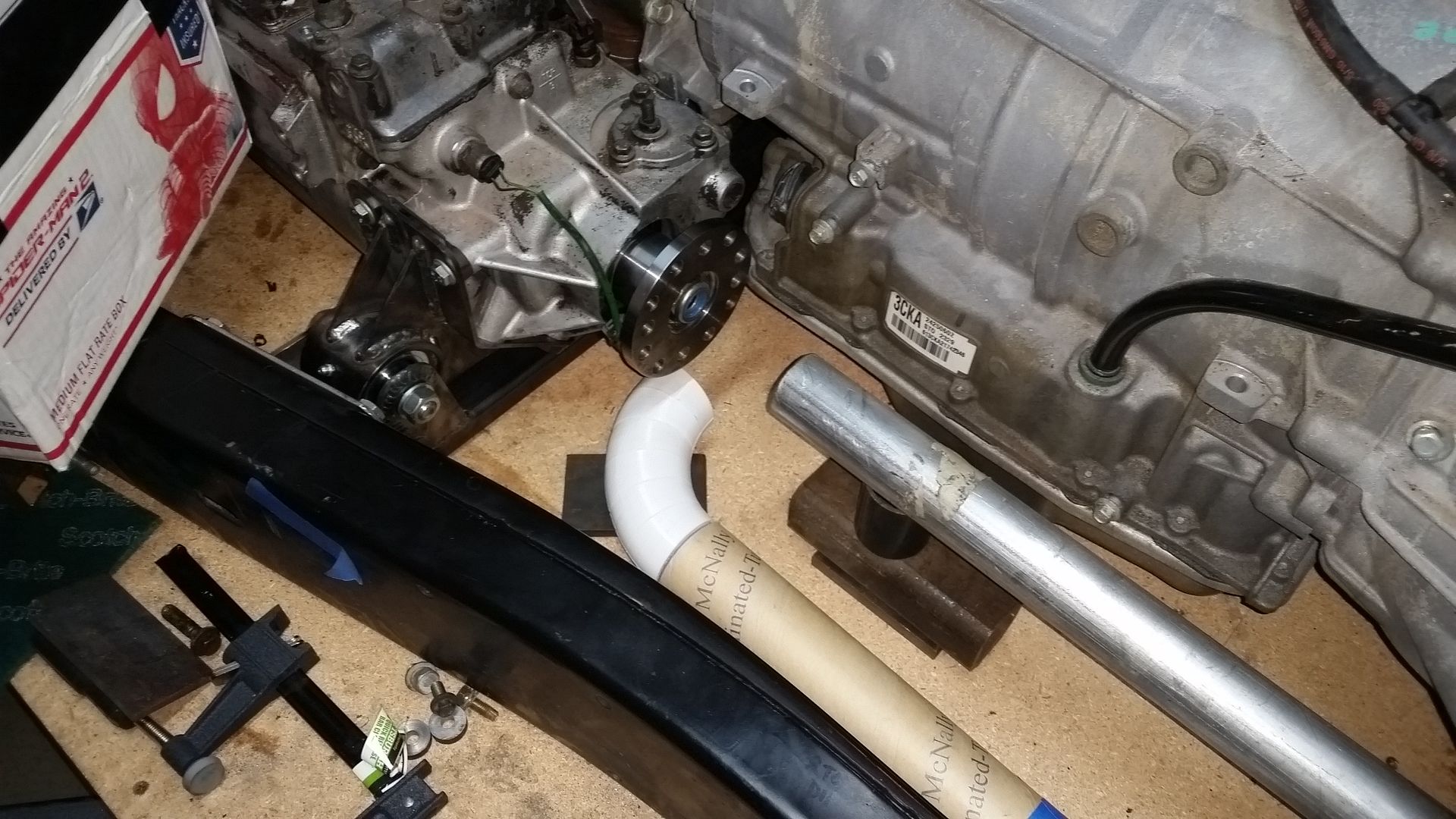
A few more views.
I can't wait to use the 'data' provided by the mockup to order the amount of 'bend' I need. I will be able to map out each side easy enough. I will not have to waste expensive stainless steel tubing doing a trial and error fitment. Once you have a complete model of one side, you can look at how you might be able to eliminate weld joints by using the tangent 'legs' on common bend angles. Very neat technology....