Metcalf
Expedition Leader
More on the rocker panel modifications....
This is what the final flange ended up looking like. Overall it really wasn't to bad to form. The 'bendy stick' tool ended up working very well. It has a little bit of a learning curve. It definitely works better on a complete panel on the vehicle. It does take about 9-10 passes to make a 90 degree flange....
You can watch the angle of the 'bendy stick' I progressed through the bending process. I also made a pass along the flange with a body hammer to crisp up the bend a little bit.
As far as I can tell the bend has the same profile as the stock bend.
Next I moved onto mocking up the position of the future rocker tube...
This is with 3x2 tubing, I will be using 3/16 wall for the final product. This short cut I had laying around is 1/8" wall I think. The corner radius on the thicker will be slightly softer.
This mock-up is with a 1" offset from the body. I think that will be a nice balance. It should be enough to keep things off the body, but not so much as to get in the way. I hate it when you ********** your shin, or mud up your pant leg, when you entry or exit the vehicle. It also isn't big enough to be tempted to use it as a step. I think that is a good thing. I'm not a fan of jumping on the rocker tube honestly. I think I may add a step on the back of the rocker just past the cab. I am going built in about 1/4" of clearance between the rocker tube and the body. This should prevent the body from contacting the rocker panel when the chassis flexes.
I am looking for some ideas on what to do with the rocker in general. How to terminate the ends? How perhaps to use the space inside the rocker for storage? I was also thinking about perhaps adding some hidden recovery points to the outriggers. Sometimes I think it would be nice to be able to hold the vehicle from the side when doing a complex recovery.
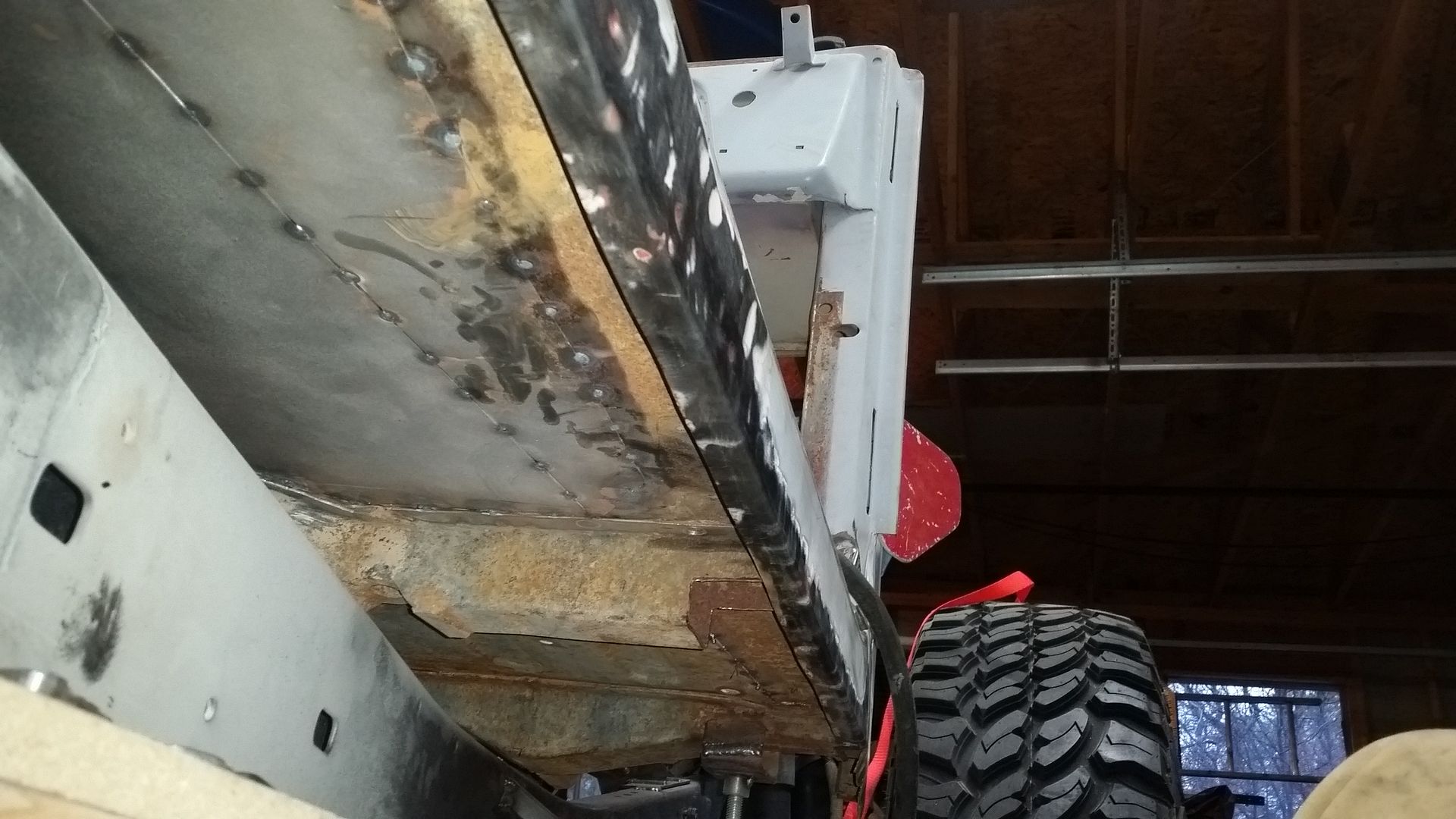
This is what the final flange ended up looking like. Overall it really wasn't to bad to form. The 'bendy stick' tool ended up working very well. It has a little bit of a learning curve. It definitely works better on a complete panel on the vehicle. It does take about 9-10 passes to make a 90 degree flange....
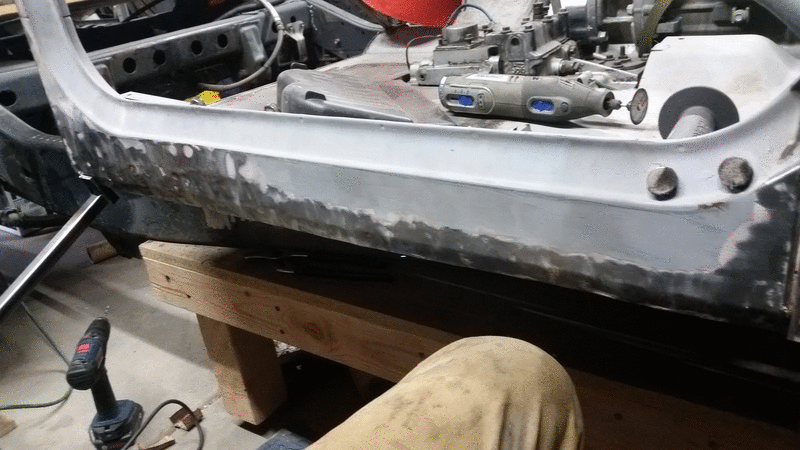
You can watch the angle of the 'bendy stick' I progressed through the bending process. I also made a pass along the flange with a body hammer to crisp up the bend a little bit.
As far as I can tell the bend has the same profile as the stock bend.
Next I moved onto mocking up the position of the future rocker tube...
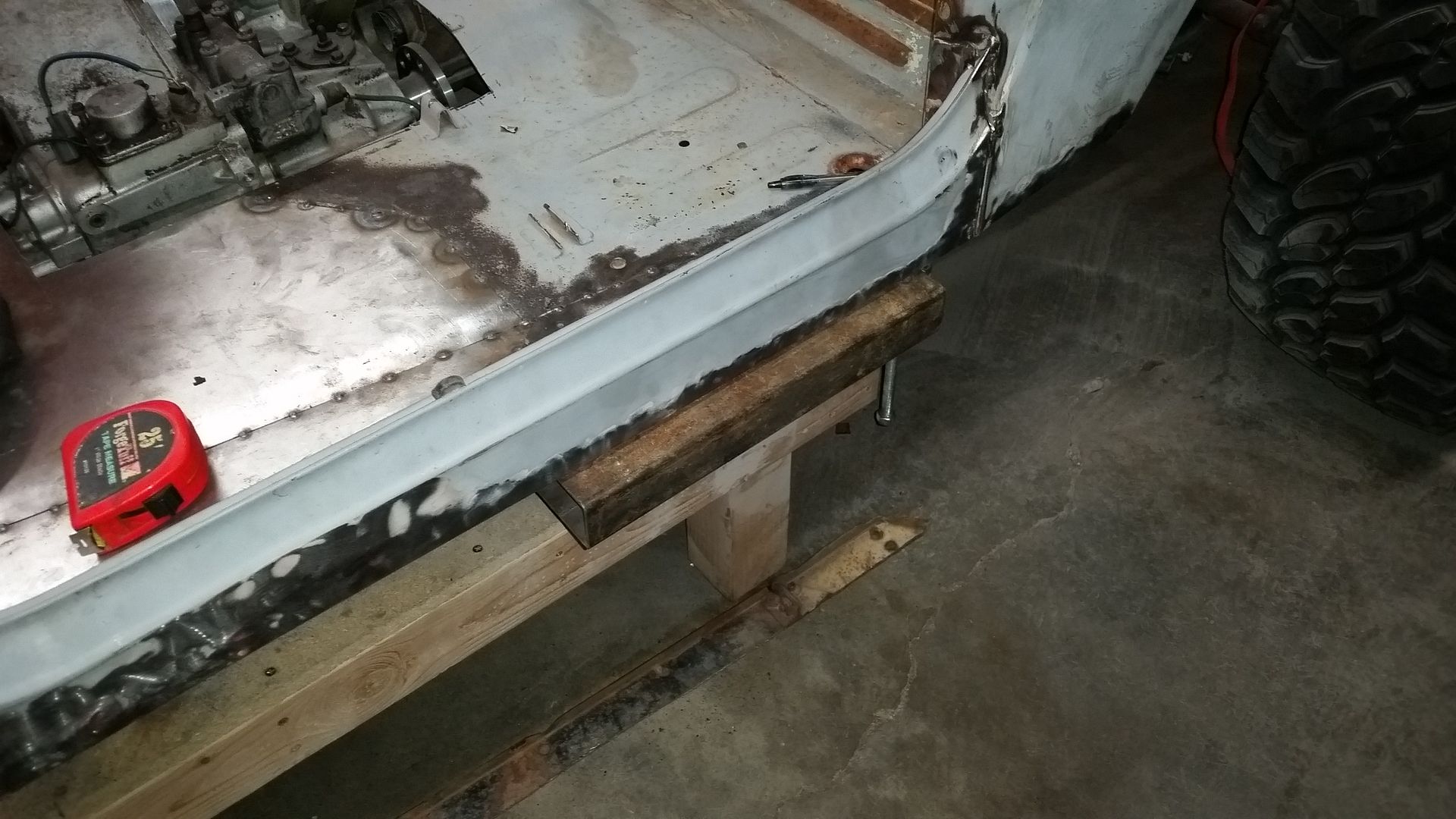
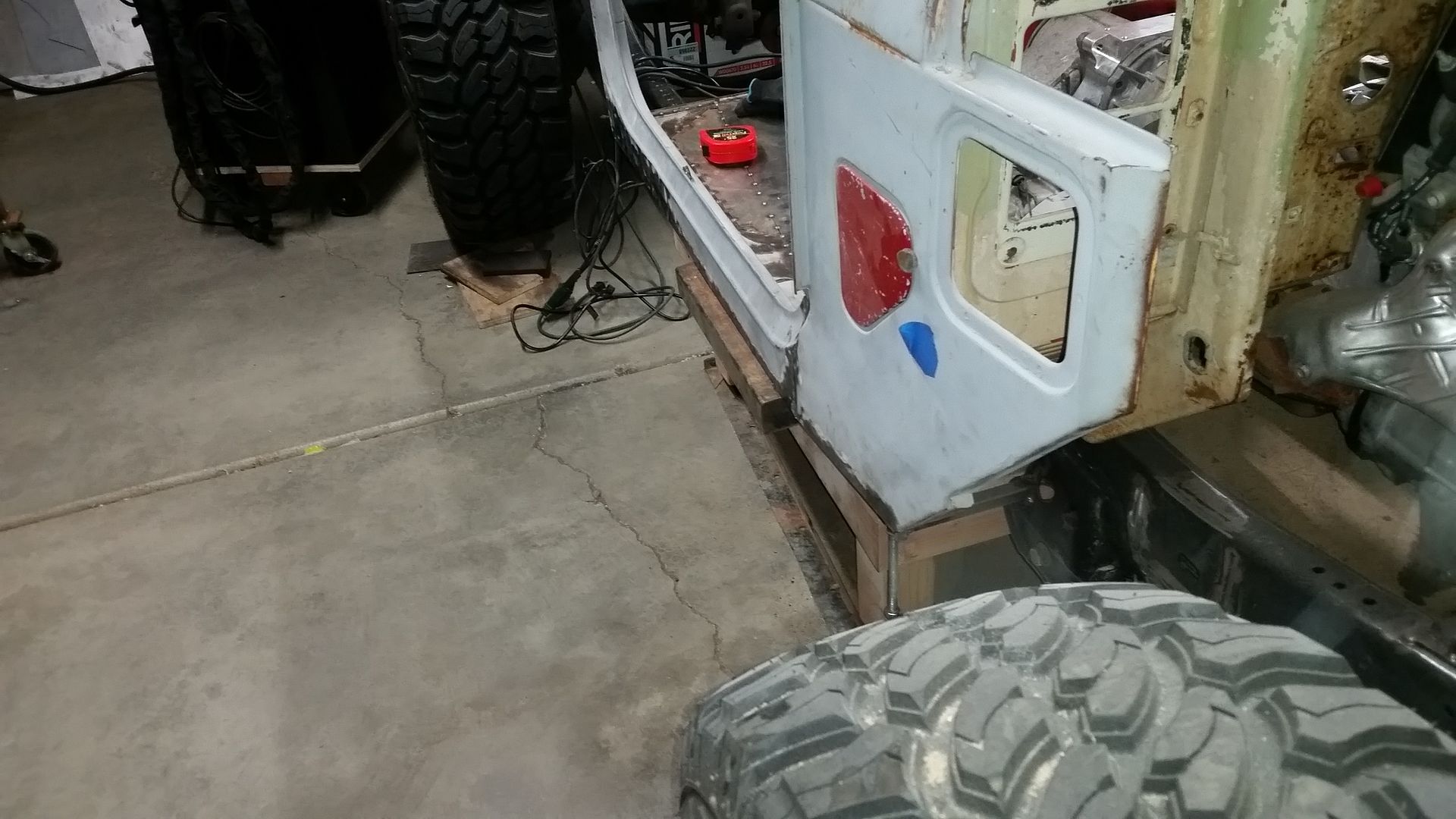
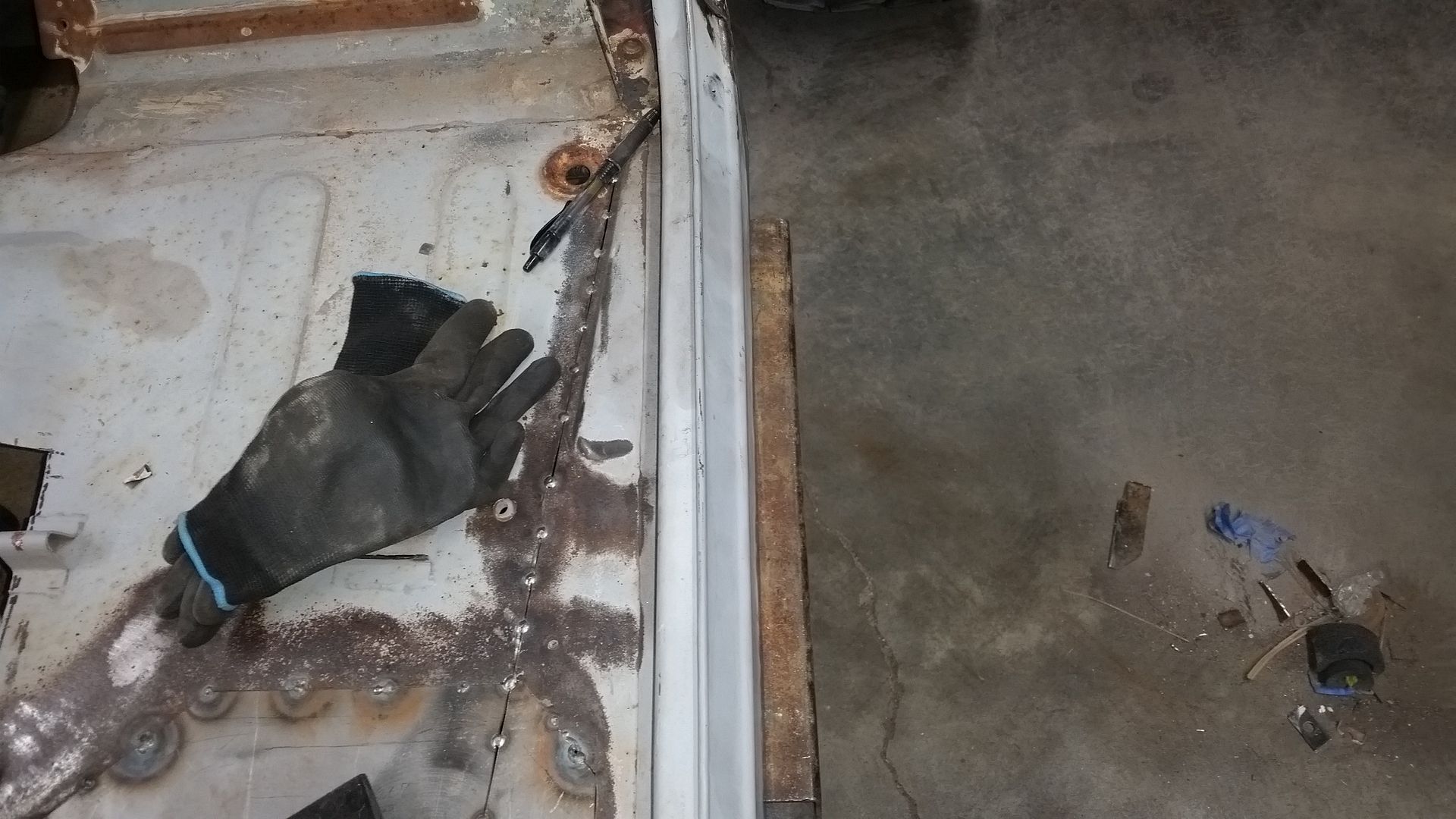
This is with 3x2 tubing, I will be using 3/16 wall for the final product. This short cut I had laying around is 1/8" wall I think. The corner radius on the thicker will be slightly softer.
This mock-up is with a 1" offset from the body. I think that will be a nice balance. It should be enough to keep things off the body, but not so much as to get in the way. I hate it when you ********** your shin, or mud up your pant leg, when you entry or exit the vehicle. It also isn't big enough to be tempted to use it as a step. I think that is a good thing. I'm not a fan of jumping on the rocker tube honestly. I think I may add a step on the back of the rocker just past the cab. I am going built in about 1/4" of clearance between the rocker tube and the body. This should prevent the body from contacting the rocker panel when the chassis flexes.
I am looking for some ideas on what to do with the rocker in general. How to terminate the ends? How perhaps to use the space inside the rocker for storage? I was also thinking about perhaps adding some hidden recovery points to the outriggers. Sometimes I think it would be nice to be able to hold the vehicle from the side when doing a complex recovery.