jscherb
Expedition Leader
A while back I picked up a side panel that bad been broken off an early model 2dr hardtop, I got it to use for prototyping the early 2dr window retrofit kit. It looked like this when I got it:
Shortly after I got it I repaired it and put a flange on the top mostly to add some stiffness to the panel, and that work turned out to be the beginning of the planning for this modular conversion project.
The other day I put a bolt flange on the back of it to make it compatible with the modular hardtop conversion. In this next photo the roof and rear panel are from the late model hardtop but the side panel is the one above and being from an early model "small window" hardtop it shows the interchangeability of the modular parts.
And with that interchangeability comes the ability to reconfigure the hardtop for different uses, here I've swapped a cargo hatch panel in place of the window panel.
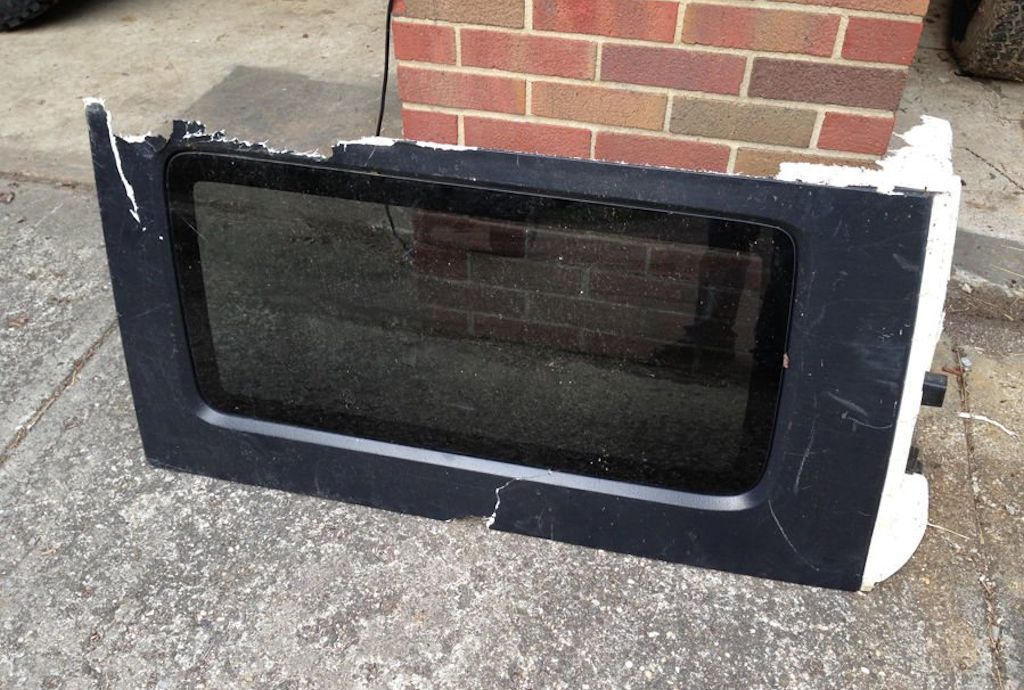
Shortly after I got it I repaired it and put a flange on the top mostly to add some stiffness to the panel, and that work turned out to be the beginning of the planning for this modular conversion project.
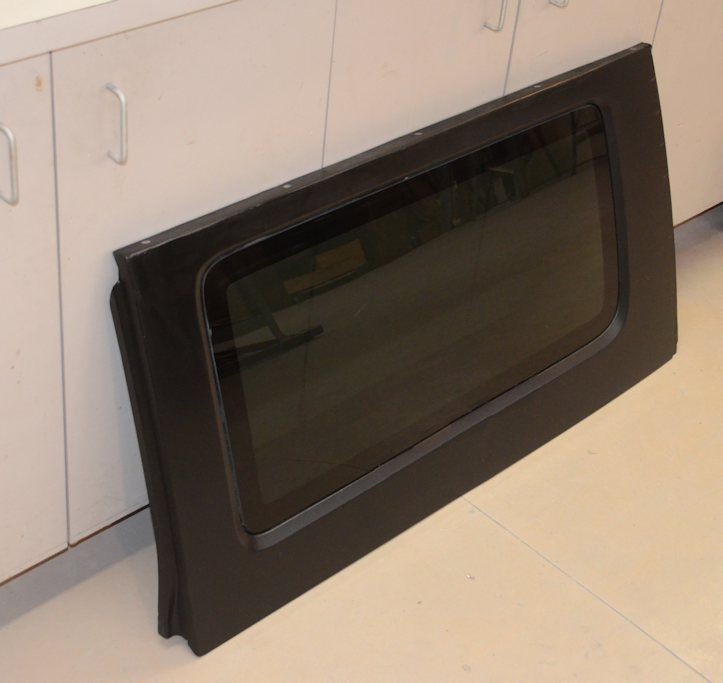
The other day I put a bolt flange on the back of it to make it compatible with the modular hardtop conversion. In this next photo the roof and rear panel are from the late model hardtop but the side panel is the one above and being from an early model "small window" hardtop it shows the interchangeability of the modular parts.
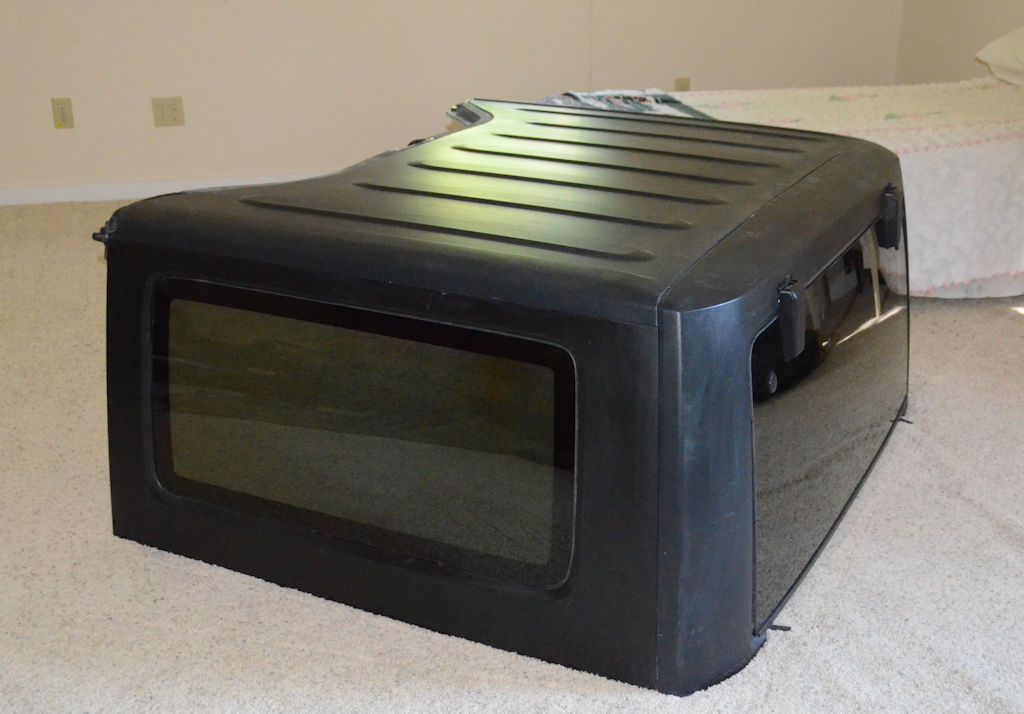
And with that interchangeability comes the ability to reconfigure the hardtop for different uses, here I've swapped a cargo hatch panel in place of the window panel.
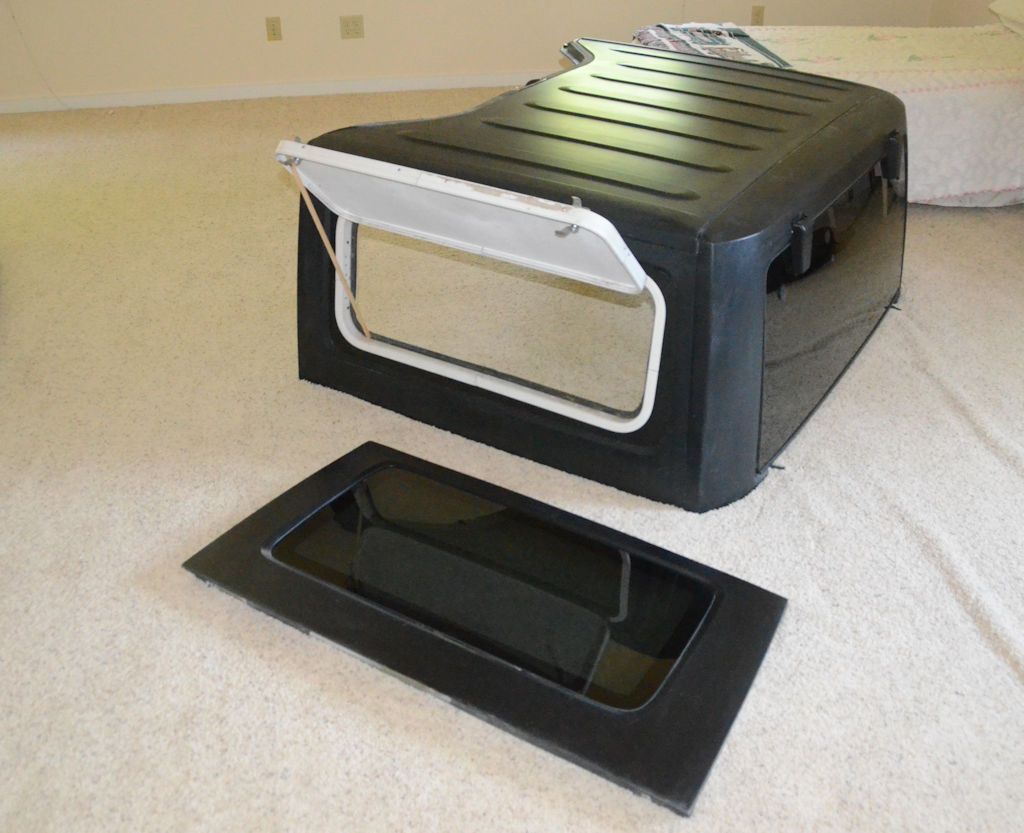
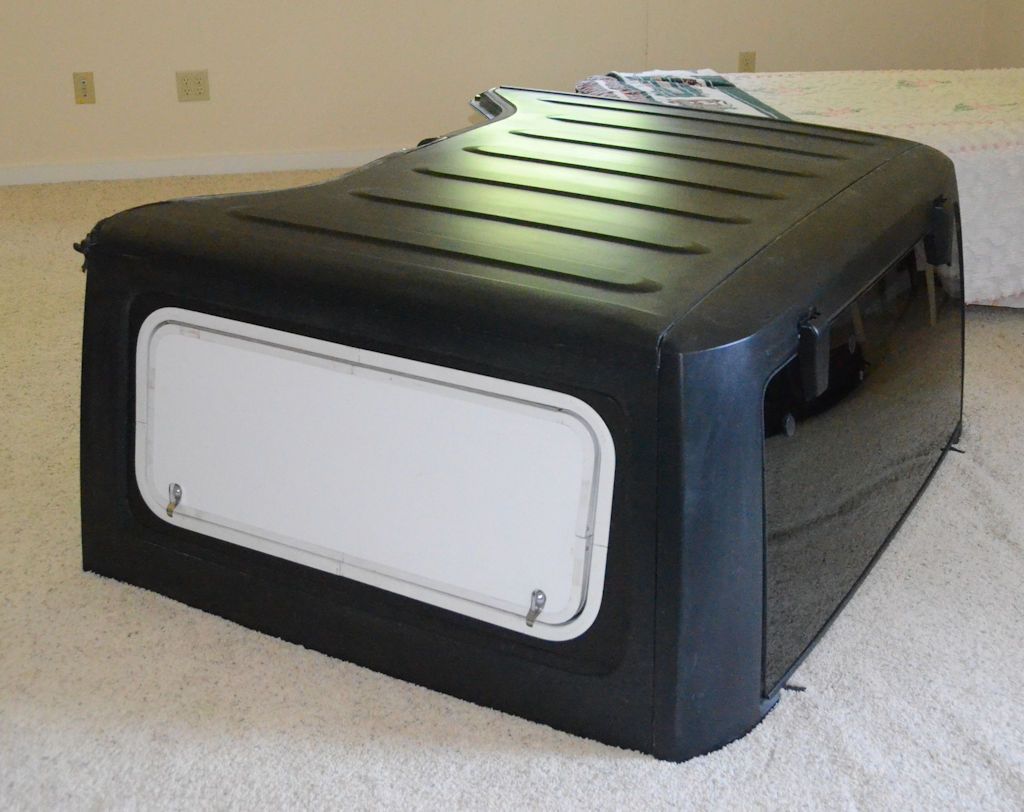
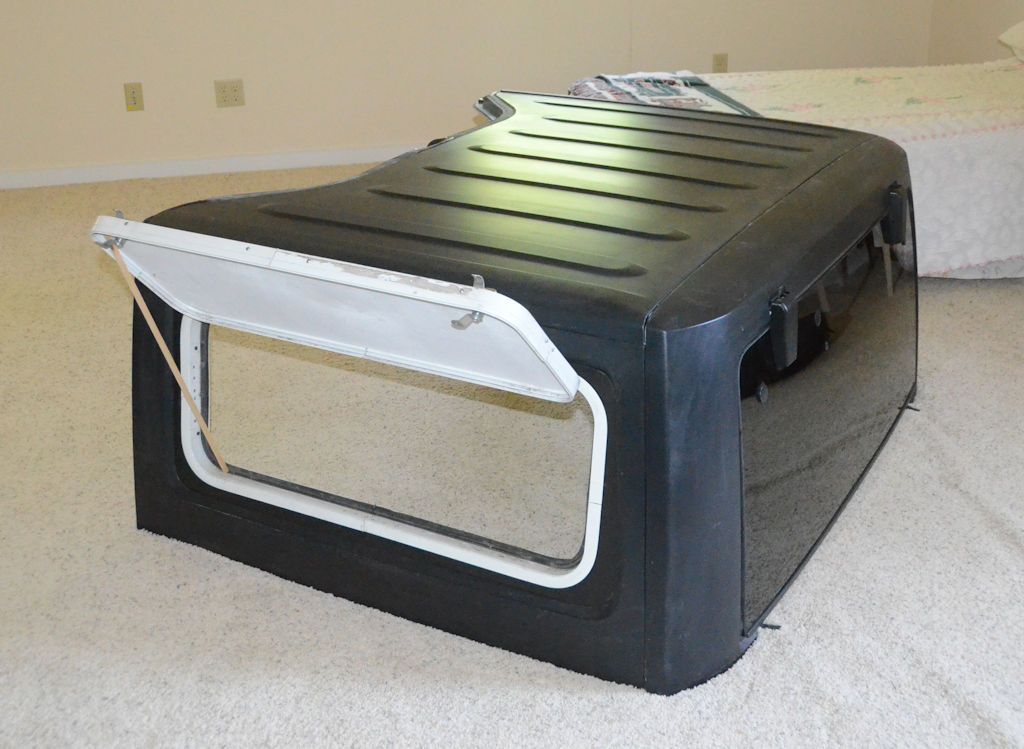