jscherb
Expedition Leader
Hey Brian,
Got your email with the photos, thanks. Your trailer and rig are really cool... so I did a quick rendering of what a matched TrailTop chuck wagon/roof top tent platform might look like on it... I hope you like it
The original photo for comparison...
Got your email with the photos, thanks. Your trailer and rig are really cool... so I did a quick rendering of what a matched TrailTop chuck wagon/roof top tent platform might look like on it... I hope you like it

The original photo for comparison...
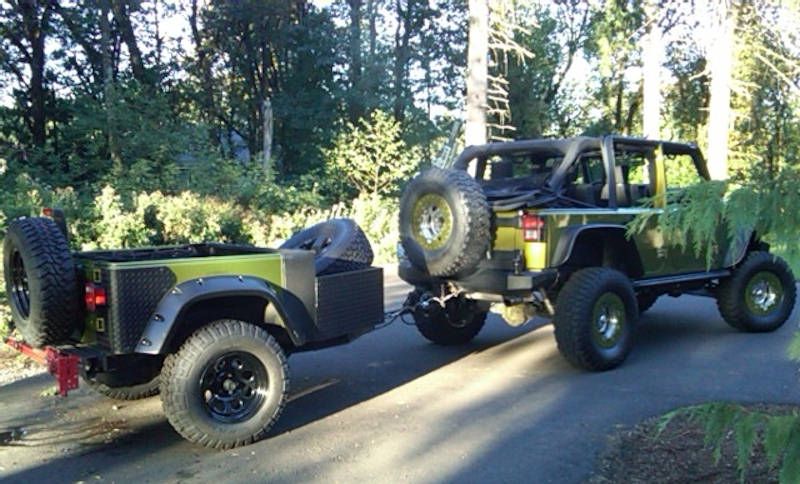
Last edited: