jscherb
Expedition Leader
The LJ hit a milestone today:
I bought it in 2009 with 22,500 miles on the clock.
In the almost 180,000 miles I've owned it it's been to 45 of the lower 48, including all 4 corners of the country; it's been to the Arctic Ocean at the north end of the Dalton Highway in Alaska and it's done thousands of trail miles in Colorado, Utah, California and other places. It's never let me down, and it's pretty much only needed basic maintenance and replacement of wear items - seals, brakes, clutch, cats, etc.
In 2010 I designed and built the Safari Cab hardtop for it and in 2014 I completed the CJ Grille Kit so it's looked as it does today for many years.
Of the three Jeeps I have it's always been and still is the one I enjoy driving the most.
I fear the day when parts become unavailable and some unavailable stupid sensor or something makes it undriveable.
If all goes according to plan, it'll be doing another Colorado trail trip this July.
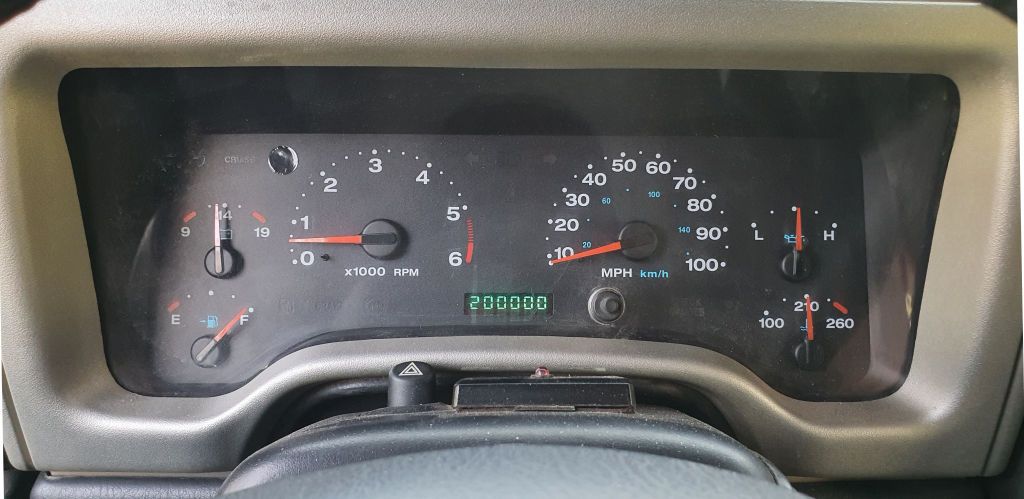
I bought it in 2009 with 22,500 miles on the clock.
In the almost 180,000 miles I've owned it it's been to 45 of the lower 48, including all 4 corners of the country; it's been to the Arctic Ocean at the north end of the Dalton Highway in Alaska and it's done thousands of trail miles in Colorado, Utah, California and other places. It's never let me down, and it's pretty much only needed basic maintenance and replacement of wear items - seals, brakes, clutch, cats, etc.
In 2010 I designed and built the Safari Cab hardtop for it and in 2014 I completed the CJ Grille Kit so it's looked as it does today for many years.
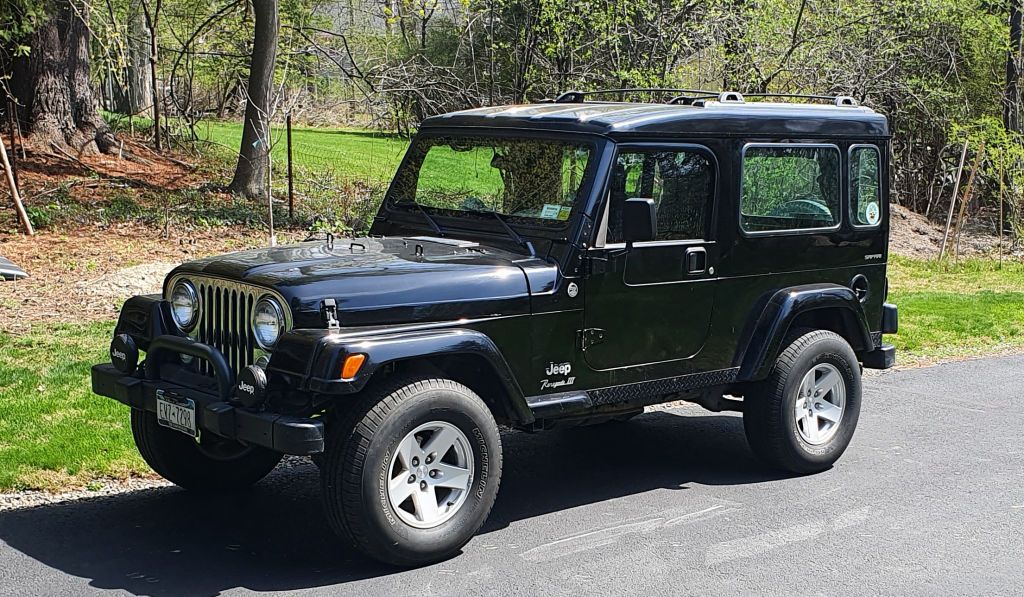
Of the three Jeeps I have it's always been and still is the one I enjoy driving the most.
I fear the day when parts become unavailable and some unavailable stupid sensor or something makes it undriveable.
If all goes according to plan, it'll be doing another Colorado trail trip this July.