MotoDave
Explorer
I will probably use some custom defrost ducts from vintage air in the top of the dash connected to a later YJ heater unit.
I'll admit i am biased, but I love the look of the Scout 80 defrost ducts
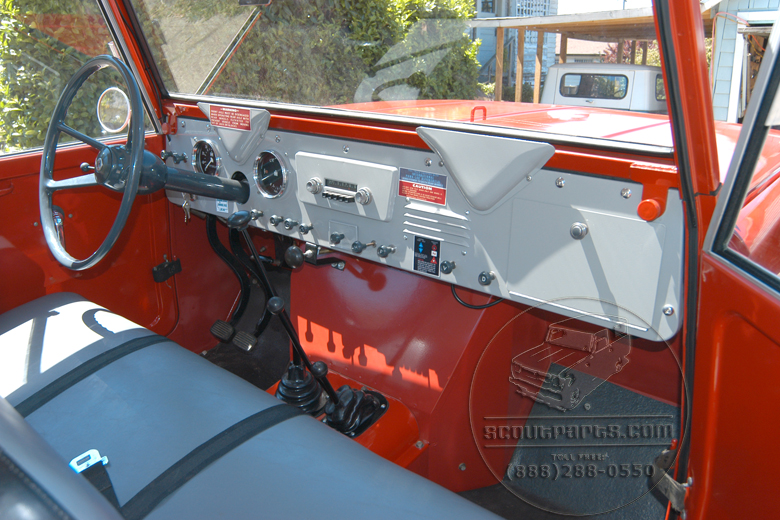
I will probably use some custom defrost ducts from vintage air in the top of the dash connected to a later YJ heater unit.
I'll admit i am biased, but I love the look of the Scout 80 defrost ducts
![]()
Ok.... I'm gonna admit that while I know your project will be jaw dropping when you get going on it, I'm stymied at the computer renderings. I (sadly) have no idea how one does stuff like that on a computer. Sure wish I did because it could be helpful for designing my custom tool trailer. *sigh*
Ok... back to offering moral support.![]()
Oh I don't think its boring at all. I have no idea how its done and think its cool. I just wish I could do it myself.![]()
Maybe you could just get one of those 3D printers and make me a complete jeep?![]()