Metcalf
Expedition Leader
Well dang....two projects keeps me pretty busy....
I pulled the transmission out of the Willys today to swap in the replacement. The current transmission (sm420) was in the vehicle when I bought it. Its always had some issues, but it lasted the 8 years or so. This spring it finally gave up. I heard a bang when I pulled it out of the snow this spring....
Getting the transmission out was fun....not. The install by the previous owner was TIGHT. The v-6 is a little close to the firewall and high in the chassis. This made getting the tranny out HARD. I ended up having to trim the tunnel a bit to get the top of the bell housing down and out. Getting it back together is going to be fun.
ouch. The tunnel was heavily modified by the previous owner. I would suspect that the engine/trans/t-case was installed without the body tub on the chassis. I should be able to weld everything back to where it was when I get it all back together.
Here is the trans and t-case out of the jeep. Its sure compact. The 1/2" thick adapter is COMPACT for sure.
The front driveshaft uses a small style u-joint similar to the th400/d18 version. This is the only way the driveshaft u-joint can clear the transmission with the compact adapter.
Here is the factory twin stick shifter snugged up against the transmission. This thing BARELY fits. There is a custom shaft for the shifters that has a set screw on the end. I'm amazed it all fits.
Here are some shots of the 1/2" thick adapter plate. Boy it makes things TIGHT! It does give me a nice long drive line though....
This is the custom input gear....
It is made from a factory D18 input gear that is bored out and pressed over a turned down sm420 2wd drive shaft yoke....
The rear output bearing one the sm420 was destroyed. It must have rusted this winter and popped when I pulled it out for the first time this spring. I'm pretty sure it had been going out of a long time.
I pulled the transmission out of the Willys today to swap in the replacement. The current transmission (sm420) was in the vehicle when I bought it. Its always had some issues, but it lasted the 8 years or so. This spring it finally gave up. I heard a bang when I pulled it out of the snow this spring....
Getting the transmission out was fun....not. The install by the previous owner was TIGHT. The v-6 is a little close to the firewall and high in the chassis. This made getting the tranny out HARD. I ended up having to trim the tunnel a bit to get the top of the bell housing down and out. Getting it back together is going to be fun.
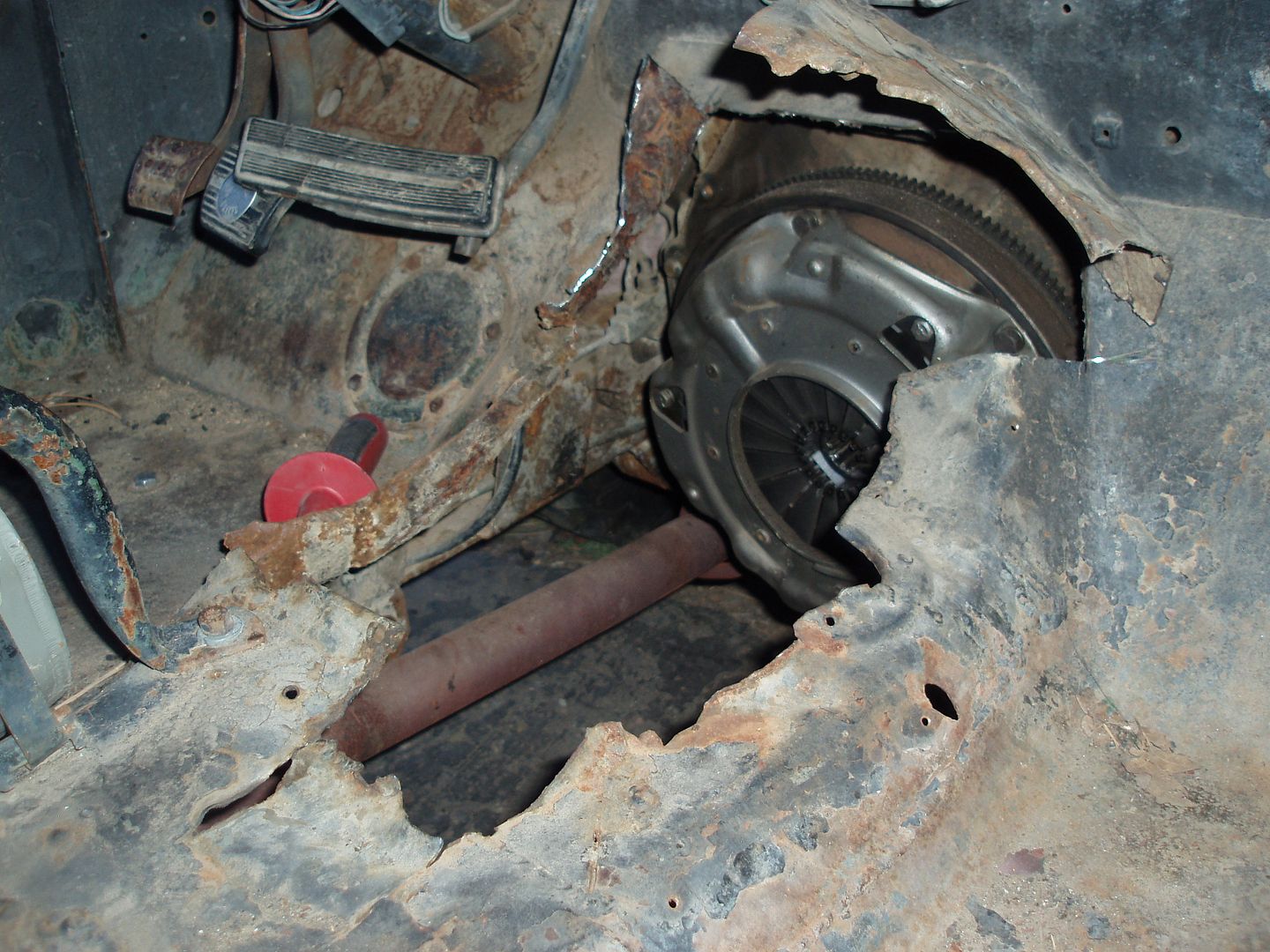
ouch. The tunnel was heavily modified by the previous owner. I would suspect that the engine/trans/t-case was installed without the body tub on the chassis. I should be able to weld everything back to where it was when I get it all back together.
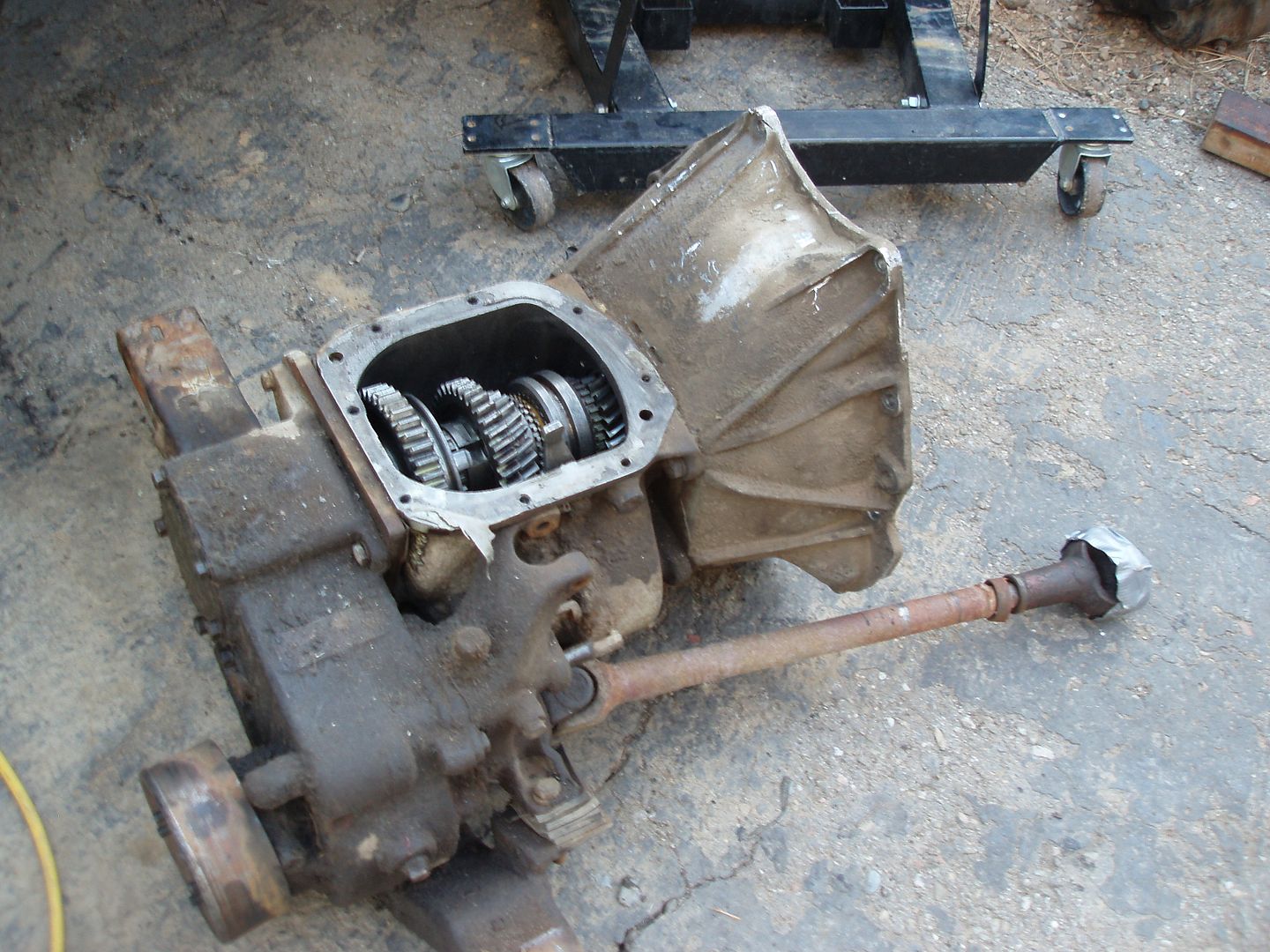
Here is the trans and t-case out of the jeep. Its sure compact. The 1/2" thick adapter is COMPACT for sure.
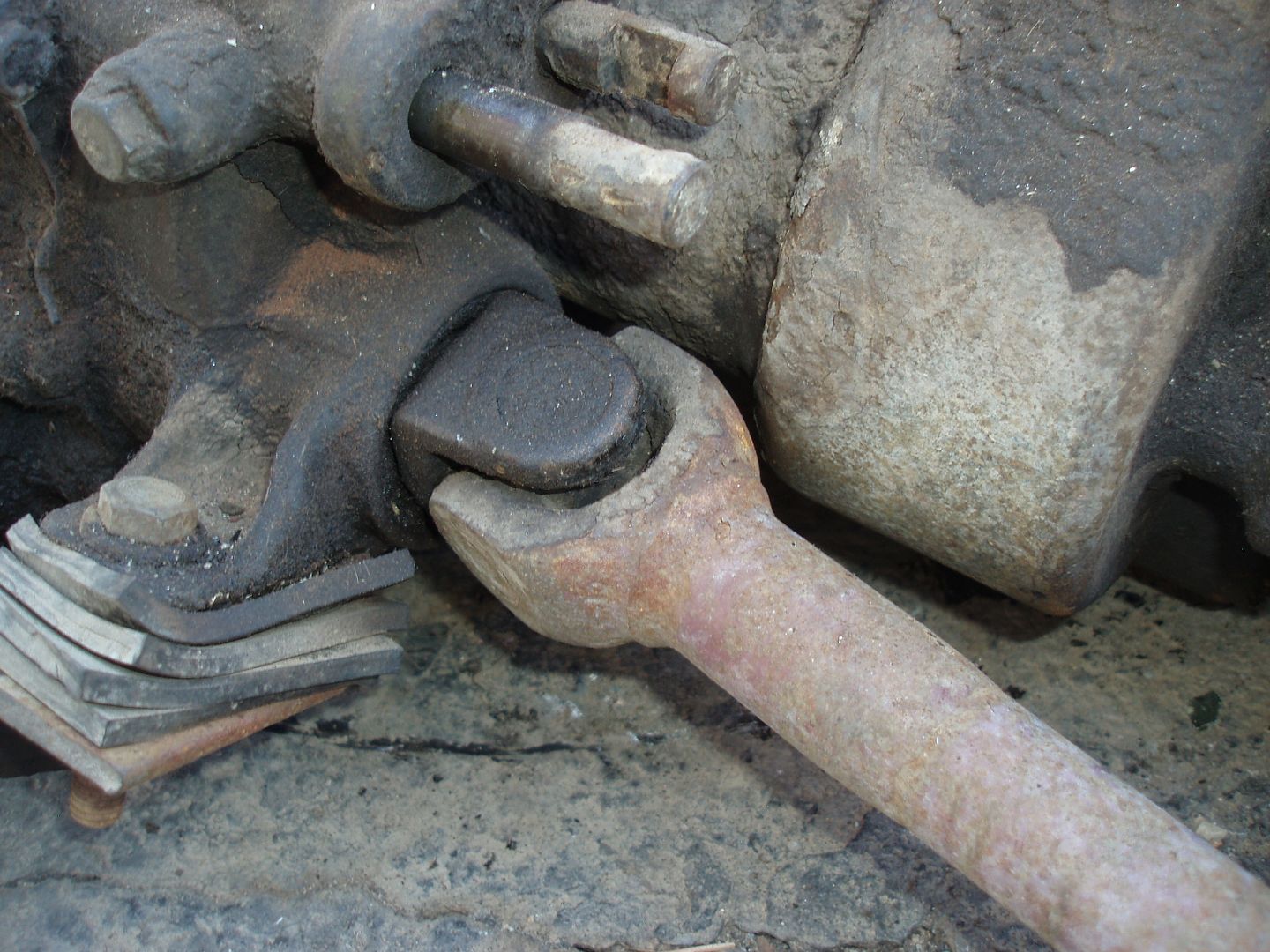
The front driveshaft uses a small style u-joint similar to the th400/d18 version. This is the only way the driveshaft u-joint can clear the transmission with the compact adapter.
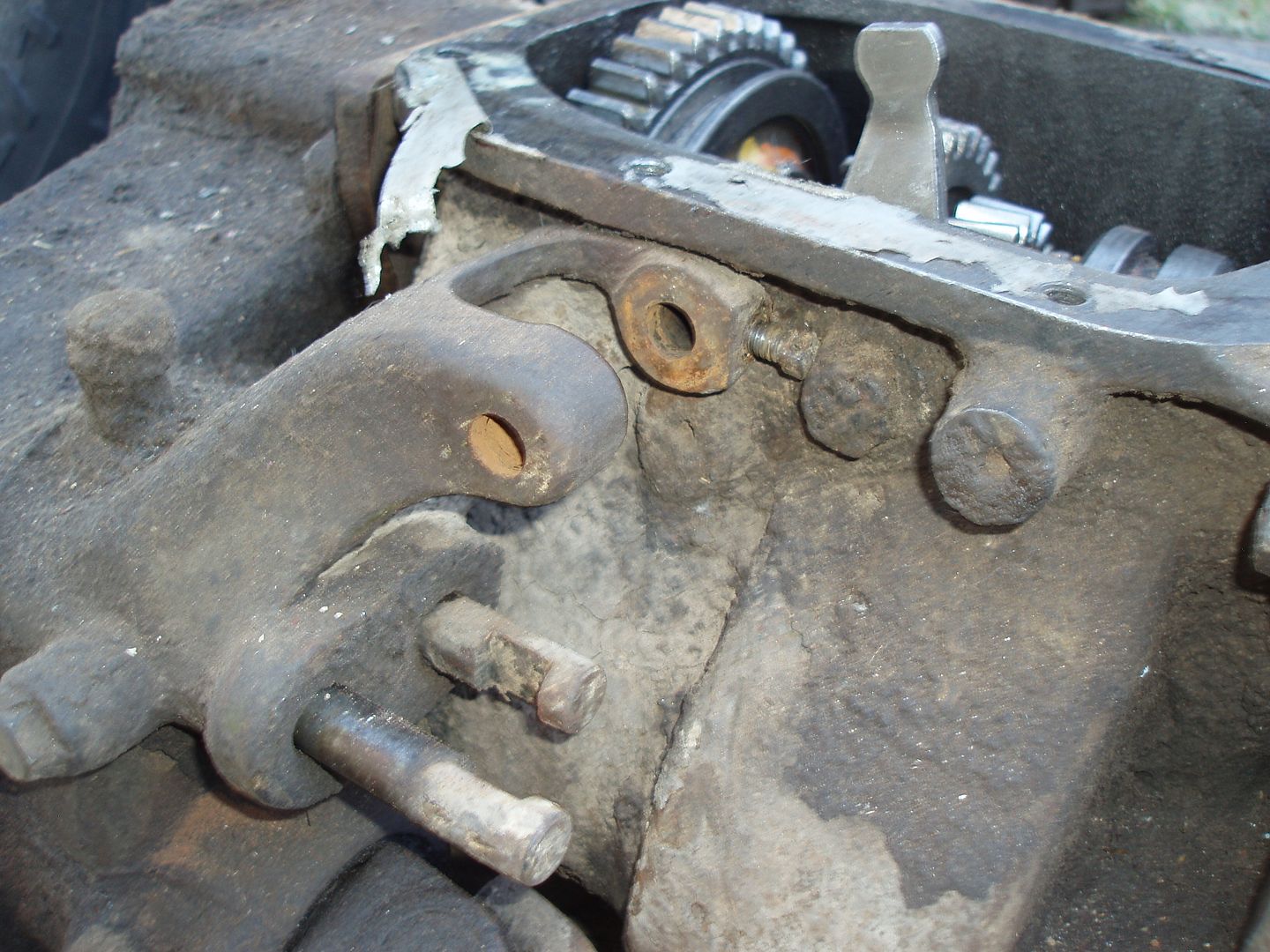
Here is the factory twin stick shifter snugged up against the transmission. This thing BARELY fits. There is a custom shaft for the shifters that has a set screw on the end. I'm amazed it all fits.
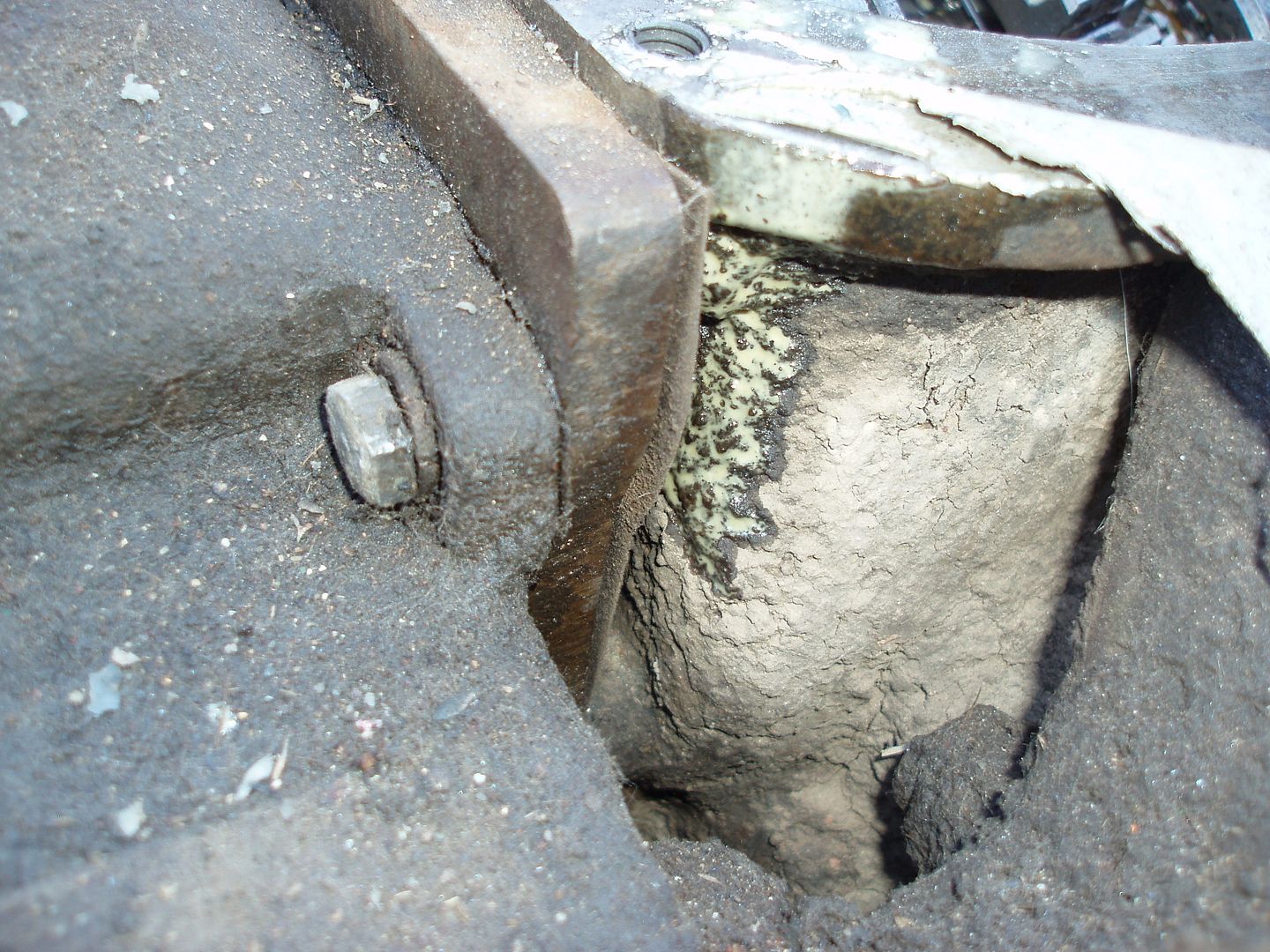
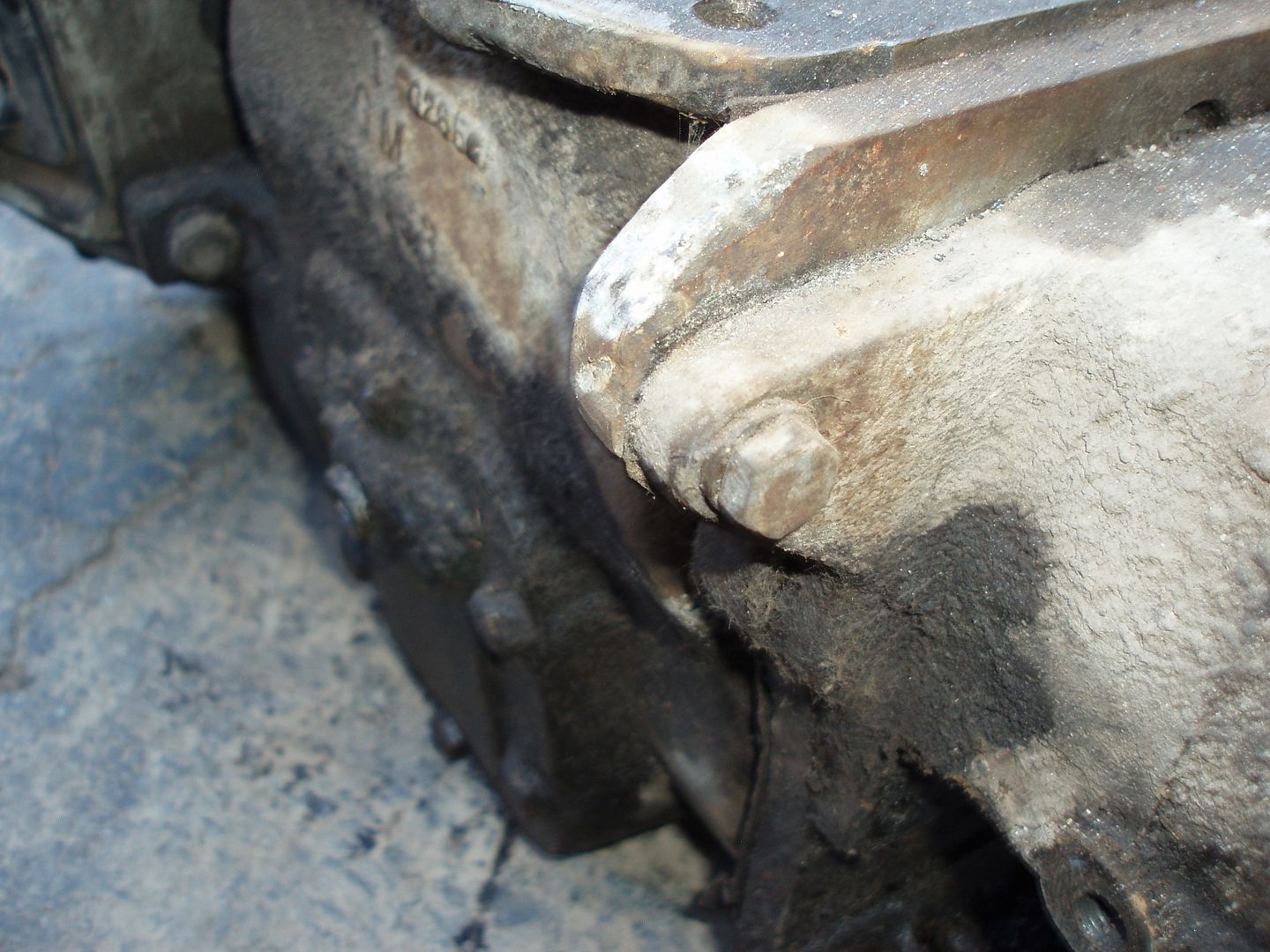
Here are some shots of the 1/2" thick adapter plate. Boy it makes things TIGHT! It does give me a nice long drive line though....

This is the custom input gear....
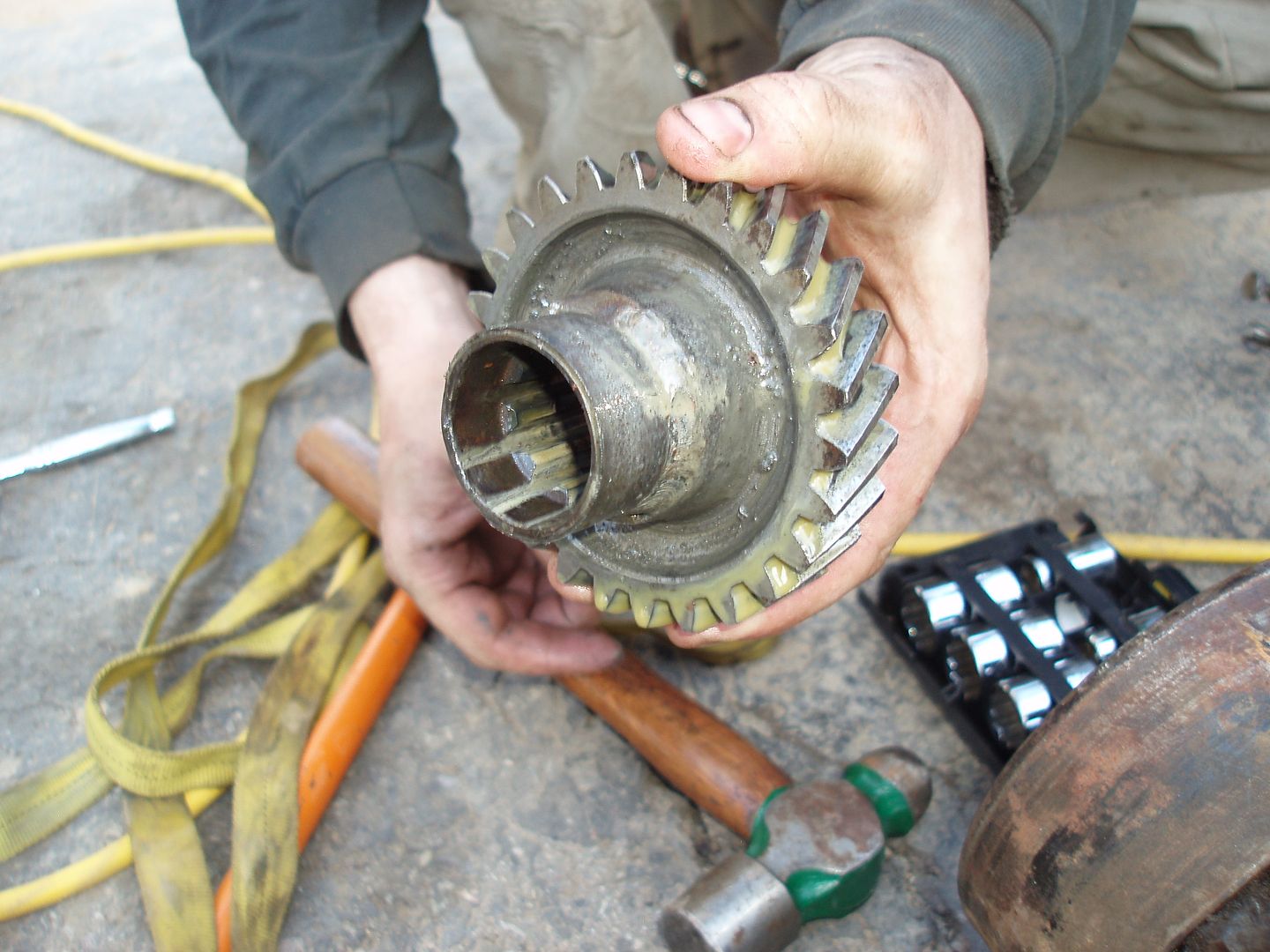
It is made from a factory D18 input gear that is bored out and pressed over a turned down sm420 2wd drive shaft yoke....
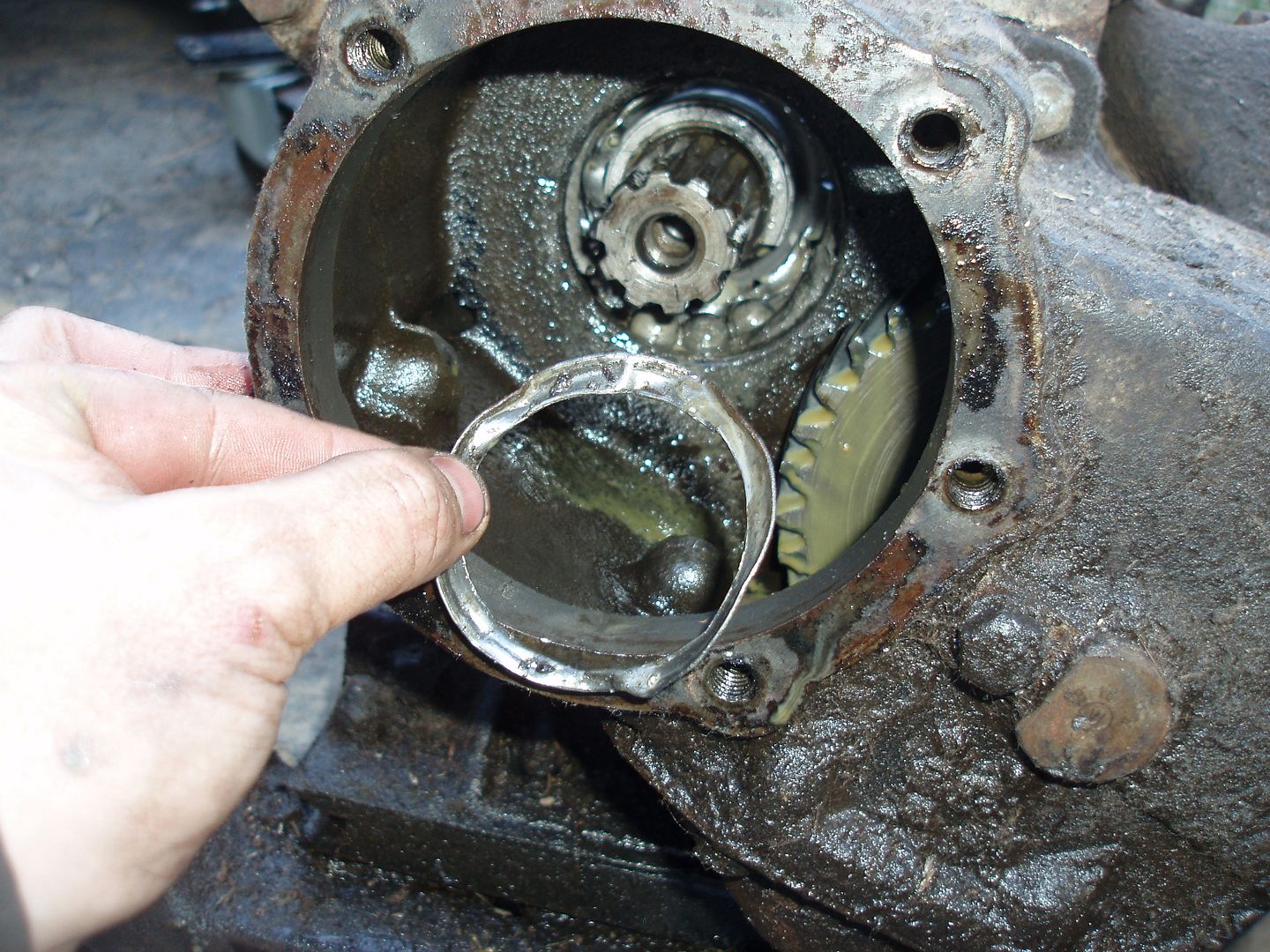
The rear output bearing one the sm420 was destroyed. It must have rusted this winter and popped when I pulled it out for the first time this spring. I'm pretty sure it had been going out of a long time.