jscherb
Expedition Leader
I shot the gelcoat on the parts I'm molding today about 90 minutes ago; it usually takes gelcoat about 2 hours to cure to the proper point where it's ready for the fiberglass layup to begin. So I'm killing time with drawing again, here's a concept similar to the previous concept with the 36" radius curved bottoms, this one's a little more rectangular.
This one could also have a galley in the back similar to a teardrop galley. The curve in the hatch would be made from on of the fiberglass 12" radius skin sections that I just made the mold for. Here's how the hatch would open:
The door on this one is a 20"-wide x 42"-high unit I found on eBay.
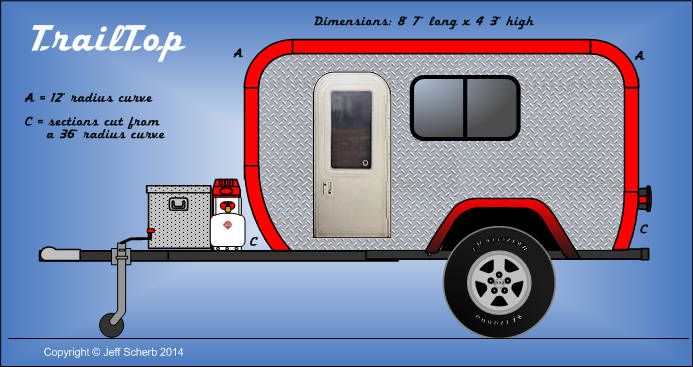
This one could also have a galley in the back similar to a teardrop galley. The curve in the hatch would be made from on of the fiberglass 12" radius skin sections that I just made the mold for. Here's how the hatch would open:
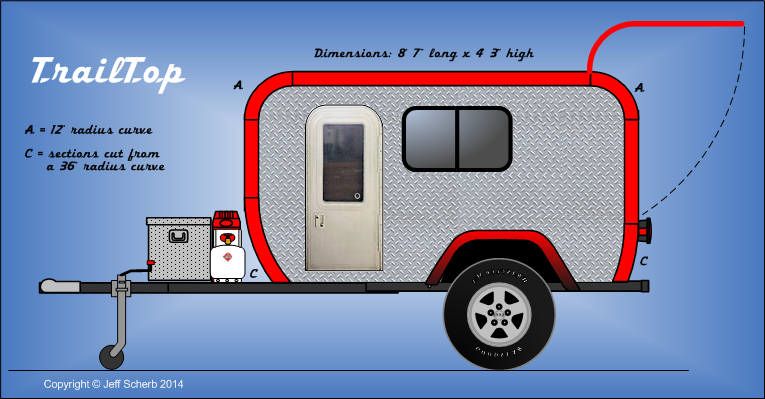
The door on this one is a 20"-wide x 42"-high unit I found on eBay.