jscherb
Expedition Leader
This is the paint I'm planning to use for the prototype trailer and frame: http://www.tcpglobal.com/Customshop...y2=Gallon-Kit&websitecategory3=Medium+Reducer. It's a two-part urethane with a low gloss (roughly 20%, so about an eggshell finish), and it also contains UV inhibitors for a longer life. BTW it's quite a bit less expensive if you order it through Amazon.
I researched a lot of different paint solutions, including paints offered in the military restoration market and normal two-stage automotive paint plus a flat clear coat. Originally I planned to ask my local auto paint jobber (Elmira Auto Paint) to custom mix some automotive paint for me to match the rattle can paint I used to do the 1/4 scale model, but after they did their homework, the best they were going to be able to offer me would have required a separate low-gloss clear coat step. Not that a separate flat clear coat bothers me, but given that I've got to do the top and bottom of the frame, and the top and bottom of the tub, the clear coat steps would have added 4 days to my paint plan.
So the Hot Rod Flatz combination of UV protection, the built-in low gloss finish (no need for a separate clear coat), and the two-part urethane for hardness and durability made the most sense to me from cost, time involved in painting and durability standpoints. I reviewed this choice with my friends at Elmira Auto Paint and they agreed it's the best way for me to go with this project. I do still plan to have Elmira Auto Paint mix up some Raptor bed liner color matched to this paint.
Based on the delivery date for the paint, it doesn't look like I'll be able to start the color painting until Friday. I'll be able to do the epoxy primer before then, but I don't want to do that too early - paint bonds best to epoxy primer within 3 days of when the primer is applied, so I'll probably start shooting primer on Wednesday.
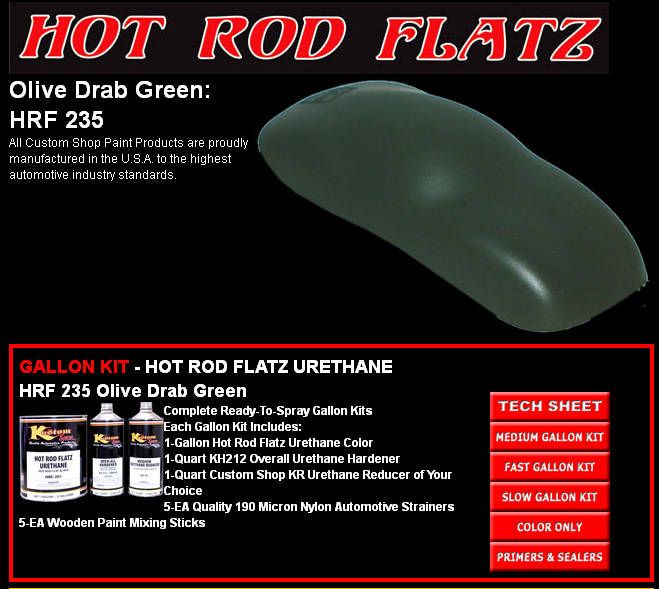
I researched a lot of different paint solutions, including paints offered in the military restoration market and normal two-stage automotive paint plus a flat clear coat. Originally I planned to ask my local auto paint jobber (Elmira Auto Paint) to custom mix some automotive paint for me to match the rattle can paint I used to do the 1/4 scale model, but after they did their homework, the best they were going to be able to offer me would have required a separate low-gloss clear coat step. Not that a separate flat clear coat bothers me, but given that I've got to do the top and bottom of the frame, and the top and bottom of the tub, the clear coat steps would have added 4 days to my paint plan.
So the Hot Rod Flatz combination of UV protection, the built-in low gloss finish (no need for a separate clear coat), and the two-part urethane for hardness and durability made the most sense to me from cost, time involved in painting and durability standpoints. I reviewed this choice with my friends at Elmira Auto Paint and they agreed it's the best way for me to go with this project. I do still plan to have Elmira Auto Paint mix up some Raptor bed liner color matched to this paint.
Based on the delivery date for the paint, it doesn't look like I'll be able to start the color painting until Friday. I'll be able to do the epoxy primer before then, but I don't want to do that too early - paint bonds best to epoxy primer within 3 days of when the primer is applied, so I'll probably start shooting primer on Wednesday.
Last edited: