Metcalf
Expedition Leader
When in doubt, cut more out of the floor and drill more holes in everything!
I removed 4" of material behind the transfer case to help with the ability to r&r the transfer case in the vehicle. I also removed the rest of the old 'hump' in the floor....
In order to level the floor I decided to use a scrap of angle iron. I could have clamped it, but that would have only gotten in the way. I ended up adding a 2" pattern of 1/8" holes in the angle iron to give me a template to use some Cleco fasteners to hold the floor up level. That worked great! Now the floor is dead level front to back. Note: the missing Cleco's in the pattern are areas where there was an existing conflict with a hat channel.
This is the panel I made to replace the 'hump' in the floor. It has a flange on the edge to provide support to the floor. That flange is welded to the existing flange on the front section....and to the left overs of the hat channel on the other end. This should help firm up the floor a lot on this side.
Same panel from the other side, tacked in place, and the clamps removed.
I am going to try to add a flange around the rest of the perimeter next. I don't think that will be too hard. I will just make some 3/4x3/4 L-flanges in my little press brake and fit them in place. I can even use the shrinker on a piece to fit the little hump in the floor. That should be fun. Use some clamps and/or cleco's to hold them in place. Then plug weld the holes. I think that will work.....
I think I have decided to make the tunnel a removable unit. I will likely split it into a front and rear unit. Then to make as much work as possible I will add some access panels in critical areas....transmission shifter, transfer case shifter, front driveshaft, etc.

I removed 4" of material behind the transfer case to help with the ability to r&r the transfer case in the vehicle. I also removed the rest of the old 'hump' in the floor....
In order to level the floor I decided to use a scrap of angle iron. I could have clamped it, but that would have only gotten in the way. I ended up adding a 2" pattern of 1/8" holes in the angle iron to give me a template to use some Cleco fasteners to hold the floor up level. That worked great! Now the floor is dead level front to back. Note: the missing Cleco's in the pattern are areas where there was an existing conflict with a hat channel.
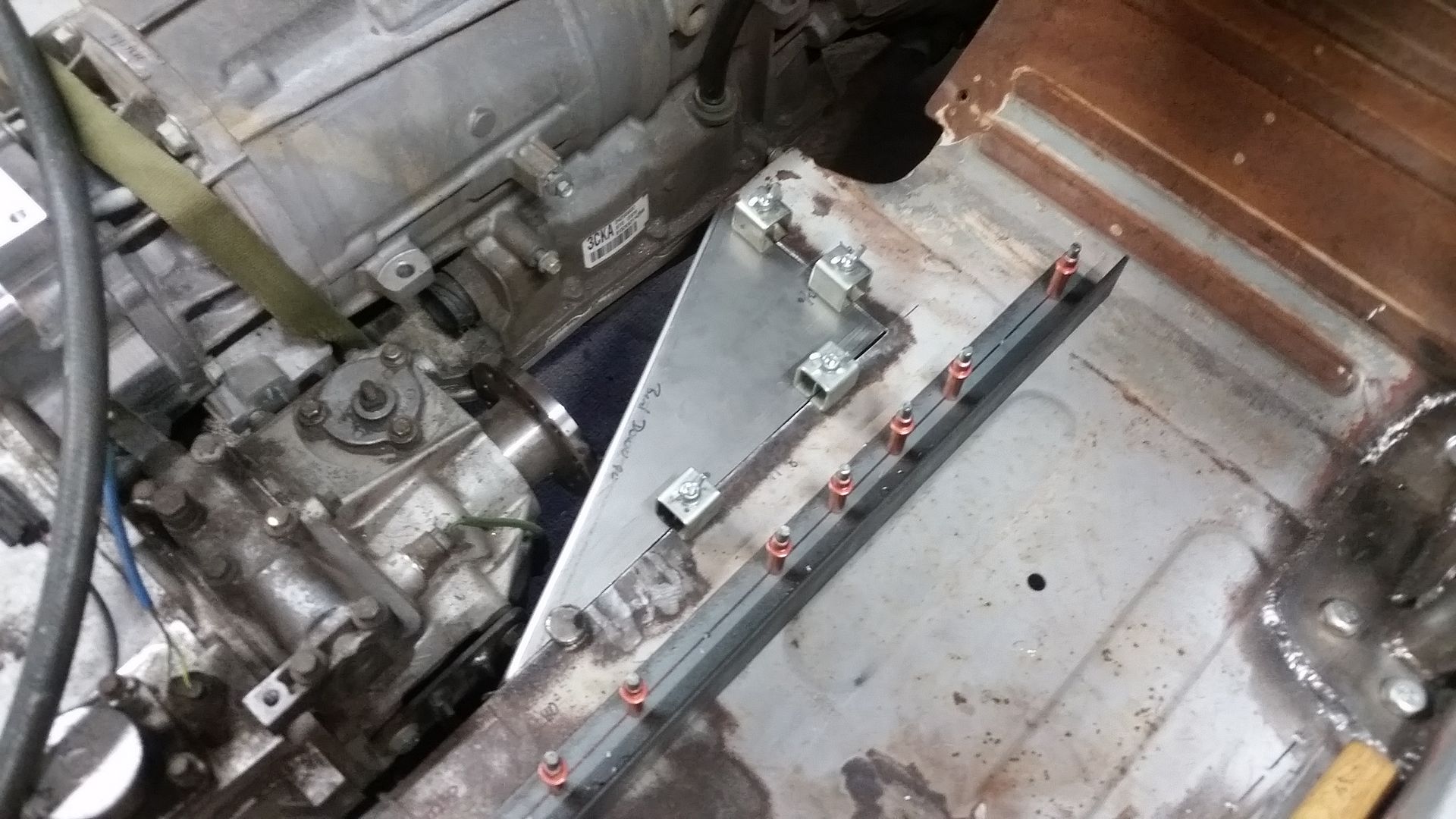
This is the panel I made to replace the 'hump' in the floor. It has a flange on the edge to provide support to the floor. That flange is welded to the existing flange on the front section....and to the left overs of the hat channel on the other end. This should help firm up the floor a lot on this side.
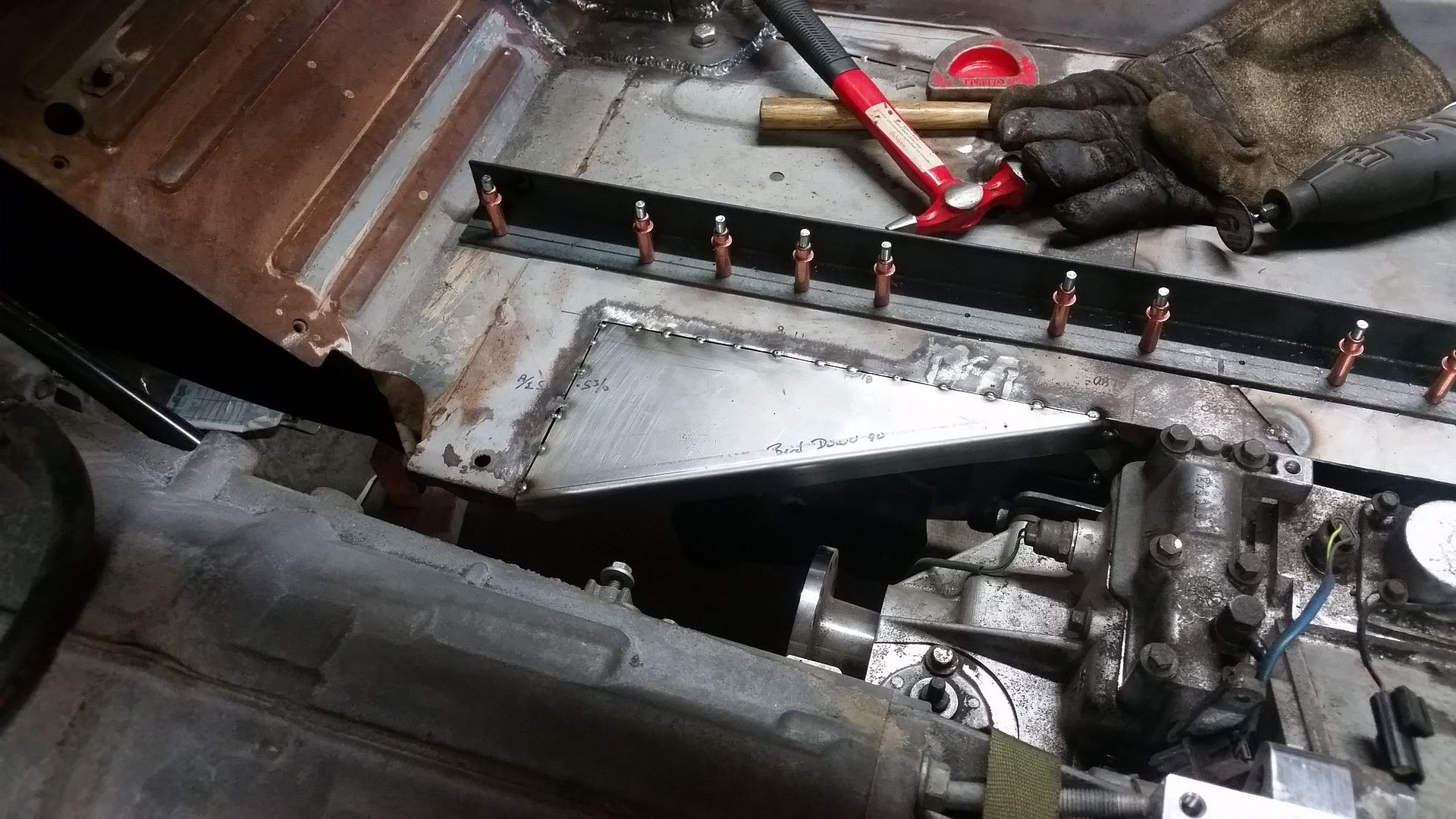
Same panel from the other side, tacked in place, and the clamps removed.
I am going to try to add a flange around the rest of the perimeter next. I don't think that will be too hard. I will just make some 3/4x3/4 L-flanges in my little press brake and fit them in place. I can even use the shrinker on a piece to fit the little hump in the floor. That should be fun. Use some clamps and/or cleco's to hold them in place. Then plug weld the holes. I think that will work.....
I think I have decided to make the tunnel a removable unit. I will likely split it into a front and rear unit. Then to make as much work as possible I will add some access panels in critical areas....transmission shifter, transfer case shifter, front driveshaft, etc.